下载PDF
DENSO discovers and understands relevant maintenance information, fast
技术
- 分析与建模 - 数据挖掘
- 分析与建模 - 预测分析
- 功能应用 - 企业资产管理系统 (EAM)
适用行业
- 汽车
适用功能
- 维护
- 质量保证
用例
- 机器状态监测
- 预测性维护
- 根因分析与诊断
服务
- 软件设计与工程服务
- 系统集成
挑战
Japanese manufacturer DENSO is the world’s second-largest producer of automotive parts. With over 130 global sites, production line staff perform tens of thousands of maintenance checks and produce over 20,000 maintenance notes each year. DENSO sought to reduce equipment downtime and increase productivity by improving search around maintenance notes. Accessing past notes and relevant fixes enabled production line engineers to repair faster, but it was difficult and time-consuming to search this mass of information. Engineers would submit requests to management, who would manually review past notes to guide repairs. This created a bottleneck, impeding productivity, especially for engineers in overseas factories. DENSO needed an accurate, categorized search system for maintenance notes, a way for line engineers to directly access and search past records, and unification of the note search system across all global sites.
关于客户
DENSO is a Japanese manufacturer and the world’s second-largest producer of automotive parts. The company operates over 130 global sites, where production line staff perform tens of thousands of maintenance checks and produce over 20,000 maintenance notes each year. DENSO's extensive operations span across various regions, necessitating efficient and effective maintenance processes to ensure minimal equipment downtime and high productivity. The company is committed to leveraging advanced technologies to streamline its operations and enhance the efficiency of its maintenance activities.
解决方案
DENSO used Luminoso to create a maintenance note search system that was fast and easy to use. The system enables line engineers to instantly view past notes and repair information most relevant to their current issue – across more than 1 million documents. Without any training data, DENSO created a conceptual understanding of its notes in minutes. With no manual tagging, the system understands not only distinctive words, such as automotive parts, but also DENSO-specific terms, such as equipment names, engineer shorthand – like “RB” for robot – and even misspellings. The company also plans to use Luminoso to identify root causes of maintenance issues unique to specific sites or equipment, analyzing decades of past knowledge to find optimal repair solutions.
运营影响
数量效益
相关案例.
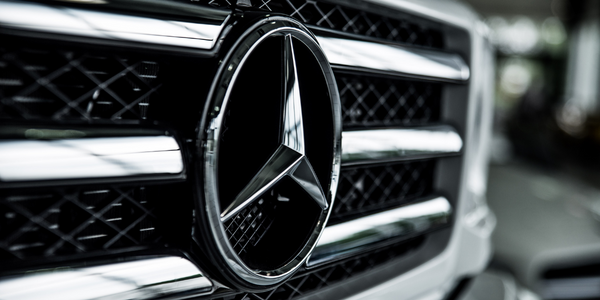
Case Study
Integral Plant Maintenance
Mercedes-Benz and his partner GAZ chose Siemens to be its maintenance partner at a new engine plant in Yaroslavl, Russia. The new plant offers a capacity to manufacture diesel engines for the Russian market, for locally produced Sprinter Classic. In addition to engines for the local market, the Yaroslavl plant will also produce spare parts. Mercedes-Benz Russia and his partner needed a service partner in order to ensure the operation of these lines in a maintenance partnership arrangement. The challenges included coordinating the entire maintenance management operation, in particular inspections, corrective and predictive maintenance activities, and the optimizing spare parts management. Siemens developed a customized maintenance solution that includes all electronic and mechanical maintenance activities (Integral Plant Maintenance).
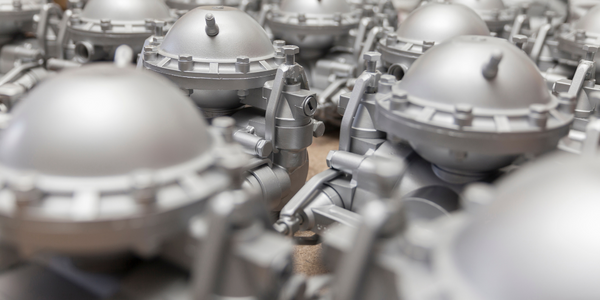
Case Study
Monitoring of Pressure Pumps in Automotive Industry
A large German/American producer of auto parts uses high-pressure pumps to deburr machined parts as a part of its production and quality check process. They decided to monitor these pumps to make sure they work properly and that they can see any indications leading to a potential failure before it affects their process.