下载PDF
DMG MORI Redesigns Robotic End-Effector using Topology Optimization & Reusable Workflows
技术
- 分析与建模 - Generative AI
- 分析与建模 - 预测分析
- 功能应用 - 制造执行系统 (MES)
适用行业
- 汽车
- 航天
- 消费品
适用功能
- 产品研发
用例
- 预测性维护
- 工厂可见化与智能化
- 自动化制造系统
服务
- 软件设计与工程服务
- 系统集成
挑战
ADDITIVE INTELLIGENCE, DMG MORI’s additive manufacturing design consultancy, was tasked with maximizing the stiffness-to-weight ratio of the head of the robotic end-effector while improving handling precision and reducing manufacturing costs. A key design requirement was to keep the external form factor of the component unaltered. At the same time, the robot head had to house the embedded channels of the pneumatic system and the end effector’s electrical components.
关于客户
DMG MORI is a leader in metal-cutting manufacturing equipment, producing high-quality CNC machines for over a century. The Robo2Go system is integral to the company’s factory automation offering. ADDITIVE INTELLIGENCE, DMG MORI’s additive manufacturing design consultancy, was tasked with maximizing the stiffness-to-weight ratio of the head of the robotic end-effector while improving handling precision and reducing manufacturing costs. A key design requirement was to keep the external form factor of the component unaltered. At the same time, the robot head had to house the embedded channels of the pneumatic system and the end effector’s electrical components.
解决方案
Since the engineers could not alter the external form of the part, the results of topology optimization could not be used directly as the final design. However, they could be used to vary the thickness of the outer shell. This process helped the team to grasp some of the structural benefits of topology optimization without changing the part’s exterior. The engineers of DMG MORI filled the shell with a conformal lattice to increase the stiffness of the part and create a permanent support structure for additive manufacturing. The team used nTopology’s engineering simulation capabilities to rapidly iterate between the available options and select a suitable lattice design. Instead of creating a one-off design, the engineers of DMG MORI developed a robust and reusable optimization process. Using as input the color-coded surfaces of each subsystem of the imported CAD file, the nTop workflow that the team developed can automatically rerun — even if the geometry changes due to design iterations or future projects.
运营影响
数量效益
相关案例.
.png)
Case Study
Improving Vending Machine Profitability with the Internet of Things (IoT)
The vending industry is undergoing a sea change, taking advantage of new technologies to go beyond just delivering snacks to creating a new retail location. Intelligent vending machines can be found in many public locations as well as company facilities, selling different types of goods and services, including even computer accessories, gold bars, tickets, and office supplies. With increasing sophistication, they may also provide time- and location-based data pertaining to sales, inventory, and customer preferences. But at the end of the day, vending machine operators know greater profitability is driven by higher sales and lower operating costs.
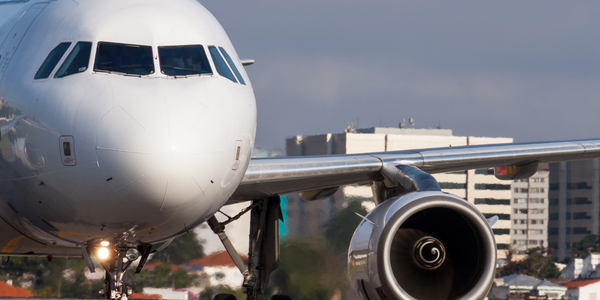
Case Study
Airbus Soars with Wearable Technology
Building an Airbus aircraft involves complex manufacturing processes consisting of thousands of moving parts. Speed and accuracy are critical to business and competitive advantage. Improvements in both would have high impact on Airbus’ bottom line. Airbus wanted to help operators reduce the complexity of assembling cabin seats and decrease the time required to complete this task.
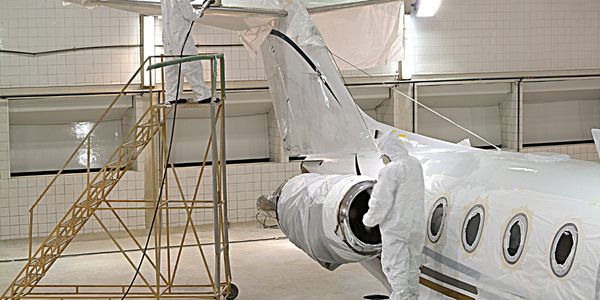
Case Study
Aircraft Predictive Maintenance and Workflow Optimization
First, aircraft manufacturer have trouble monitoring the health of aircraft systems with health prognostics and deliver predictive maintenance insights. Second, aircraft manufacturer wants a solution that can provide an in-context advisory and align job assignments to match technician experience and expertise.
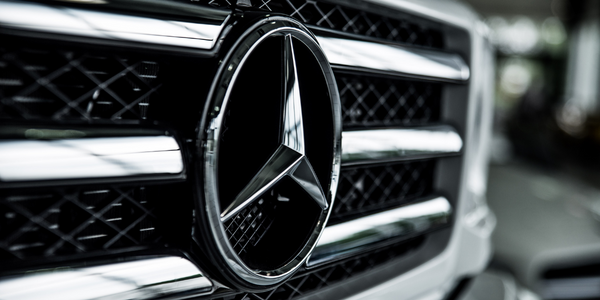
Case Study
Integral Plant Maintenance
Mercedes-Benz and his partner GAZ chose Siemens to be its maintenance partner at a new engine plant in Yaroslavl, Russia. The new plant offers a capacity to manufacture diesel engines for the Russian market, for locally produced Sprinter Classic. In addition to engines for the local market, the Yaroslavl plant will also produce spare parts. Mercedes-Benz Russia and his partner needed a service partner in order to ensure the operation of these lines in a maintenance partnership arrangement. The challenges included coordinating the entire maintenance management operation, in particular inspections, corrective and predictive maintenance activities, and the optimizing spare parts management. Siemens developed a customized maintenance solution that includes all electronic and mechanical maintenance activities (Integral Plant Maintenance).