下载PDF
DS PLM SUCCESS STORY - TÜV SÜD: Certifying nuclear power plants with Abaqus FEA from SIMULIA
技术
- 分析与建模 - 数字孪生/模拟
适用功能
- 质量保证
用例
- 预测性维护
服务
- 测试与认证
挑战
TÜV SÜD, a leading global technical service corporation in Filderstadt, Germany, is responsible for independently testing, inspecting, and certifying nuclear facilities for licensing by the German government. The company needed to ensure the safety of nuclear plant reactors by identifying and correcting problems that threaten the longevity of the plants. The systems, structures, and components of nuclear plants can change with time and use. Components can wear out, corrode, or degrade; instrument and control systems may become obsolete as technologies evolve. The properties of critical materials may change through heat and neutron irradiation. Identifying and correcting longevity issues can extend the operating license of a plant by several decades, which is why upgrading older facilities is a major focus of nuclear regulatory bodies and plant operators.
关于客户
TÜV SÜD is a leading global technical service corporation based in Filderstadt, Germany. The company is responsible for independently testing, inspecting, and certifying nuclear facilities for licensing by the German government. Their work involves identifying and correcting longevity issues that help extend the operating license of a plant and that ensure new facilities a lifetime of safe operation. The company's goal is to ensure that the structural integrity and operational management of nuclear facilities are secured far into the future, regardless of the type or age of the plant.
解决方案
To assist in the evaluation of nuclear plant integrity, TÜV SÜD relies on Abaqus FEA from SIMULIA. The company uses Abaqus to analyze stress loads over a wide range of scenarios such as rapid temperature and/or pressure changes, airplane impact, earthquakes, and radiation embrittlement. The software is used to analyze everything from key mechanical components - including pumps, piping systems, vessels, supports, and tanks - to fuel assemblies, building structures, and lifting devices. TÜV engineers used Abaqus/CAE to build and mesh computer models of the vessel and the four water pipe nozzles that fed into it. The TÜV SÜD team then used Abaqus/Standard for linear elastic simulation of the rapid cooling of the vessel, calculating the effects of a large increase in tensile stresses on the inner vessel wall.
运营影响
相关案例.
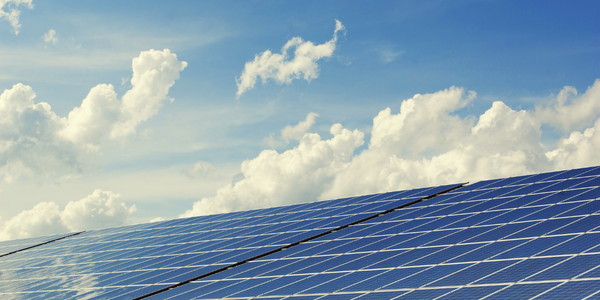
Case Study
Remote Monitoring & Predictive Maintenance App for a Solar Energy System
The maintenance & tracking of various modules was an overhead for the customer due to the huge labor costs involved. Being an advanced solar solutions provider, they wanted to ensure early detection of issues and provide the best-in-class customer experience. Hence they wanted to automate the whole process.
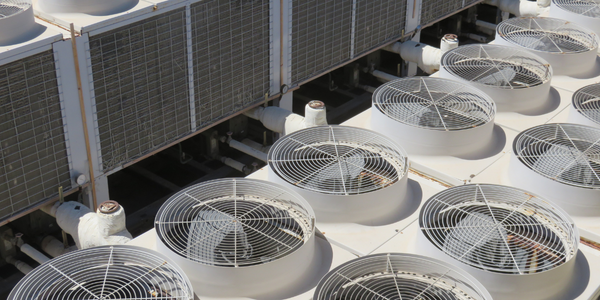
Case Study
Predictive Maintenance for Industrial Chillers
For global leaders in the industrial chiller manufacturing, reliability of the entire production process is of the utmost importance. Chillers are refrigeration systems that produce ice water to provide cooling for a process or industrial application. One of those leaders sought a way to respond to asset performance issues, even before they occur. The intelligence to guarantee maximum reliability of cooling devices is embedded (pre-alarming). A pre-alarming phase means that the cooling device still works, but symptoms may appear, telling manufacturers that a failure is likely to occur in the near future. Chillers who are not internet connected at that moment, provide little insight in this pre-alarming phase.
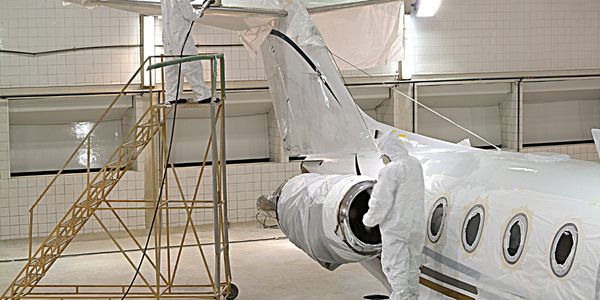
Case Study
Aircraft Predictive Maintenance and Workflow Optimization
First, aircraft manufacturer have trouble monitoring the health of aircraft systems with health prognostics and deliver predictive maintenance insights. Second, aircraft manufacturer wants a solution that can provide an in-context advisory and align job assignments to match technician experience and expertise.
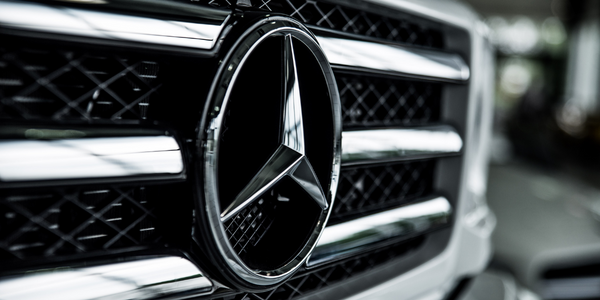
Case Study
Integral Plant Maintenance
Mercedes-Benz and his partner GAZ chose Siemens to be its maintenance partner at a new engine plant in Yaroslavl, Russia. The new plant offers a capacity to manufacture diesel engines for the Russian market, for locally produced Sprinter Classic. In addition to engines for the local market, the Yaroslavl plant will also produce spare parts. Mercedes-Benz Russia and his partner needed a service partner in order to ensure the operation of these lines in a maintenance partnership arrangement. The challenges included coordinating the entire maintenance management operation, in particular inspections, corrective and predictive maintenance activities, and the optimizing spare parts management. Siemens developed a customized maintenance solution that includes all electronic and mechanical maintenance activities (Integral Plant Maintenance).

Case Study
Asset Management and Predictive Maintenance
The customer prides itself on excellent engineering and customer centric philosophy, allowing its customer’s minds to be at ease and not worry about machine failure. They can easily deliver the excellent maintenance services to their customers, but there are some processes that can be automated to deliver less downtime for the customer and more efficient maintenance schedules.