下载PDF
FAGE USA Dairy expands into the US, its 28th country
技术
- 自动化与控制 - 自动化与过程控制系统
- 功能应用 - 仓库管理系统 (WMS)
- 功能应用 - 远程监控系统
适用行业
- 食品与饮料
- 消费品
适用功能
- 仓库和库存管理
- 物流运输
用例
- 库存管理
- 仓库自动化
- 预测性维护
服务
- 系统集成
- 软件设计与工程服务
挑战
FAGE has 3 state-of-the-art plants in Greece, which are substantially automated. The company philosophy incorporates automation as a means of competing efficiently, and maintaining product safety. Their experience with automation and its rewards, means they are well versed in the specific features they required from an AS/RS. Their requirements include the handling of buffer product from manufacturing, full pallet movement, case picking, and buffered pre-picked material back into the AS/RS for future retrieval for truck loading. FAGE USA handles individual orders, distribution center orders, and combinations of both. FAGE’s yogurt and cheese products come on trays and cases. Each pallet has either 240 or 180 trays, depending on the size of the product. The AS/RS handles pallets 40’w x 48’l x 78”h. Pallets are loaded into the AS/RS with a single SKU from manufacturing via the cooling tunnel, or via the docks where some cheese SKU’s arrive from Greece. Pallets must be loaded so the product on the bottom can handle the sustained weight, forcing shorter load heights in certain cases. And as future growth demands, the number of SKU’s and case sizes will grow and change.
关于客户
FAGE, based in Athens, Greece, has taken the dairy world by storm with its all-natural, premium yogurt that has a distinctly rich, creamy, and fresh taste. After much success in Europe, the company is expanding into the US market – its 28th country. FAGE USA Dairy’s new plant in Johnstown, NY has a complete Westfalia Technologies, Inc. High Density Automated Storage & Retrieval System (AS/RS) with Savanna.NET® Warehouse Management System (WMS). Westfalia’s AS/RS will handle storage and picking in the 40° F warehouse.
解决方案
To meet these requirements Westfalia initially designed and built a 1,600 pallet free-standing rack warehouse utilizing our high-density AS/RS. Within three years, demand and growth were such that the crane aisle has been extended, with more racking and gravity flow pick lanes installed to accommodate an additional 2,460 pallets. Today, Westfalia’s automated storage and retrieval system consists of one Storage/Retrieval Machine (S/RM), a complete pallet conveying system, gravity flow pick lanes, bar code scanners, stretch wrappers, label printing and placement equipment, and Savanna.NET® WMS to control the product flow throughout the facility. The AS/RS measures 33’ high, has 4 levels, and stores in total over 4,100 pallets. Our Satellite® entry vehicle stores pallet loads 5-deep on one side of the aisle and 11-deep on the other side. All pallets are supported on our 3-rail system which provides a safer, more reliable system as pallet deflection/breakage is eliminated. Gravity flow rail pick lanes are located in the first level of the rack on the dock side of the warehouse for filling less than full pallet orders. Products can flow from the AS/RS to the picking lane or to the full pallet output where fork lift trucks can pick up pallets and load the trucks.
运营影响
数量效益
相关案例.
.png)
Case Study
Improving Vending Machine Profitability with the Internet of Things (IoT)
The vending industry is undergoing a sea change, taking advantage of new technologies to go beyond just delivering snacks to creating a new retail location. Intelligent vending machines can be found in many public locations as well as company facilities, selling different types of goods and services, including even computer accessories, gold bars, tickets, and office supplies. With increasing sophistication, they may also provide time- and location-based data pertaining to sales, inventory, and customer preferences. But at the end of the day, vending machine operators know greater profitability is driven by higher sales and lower operating costs.
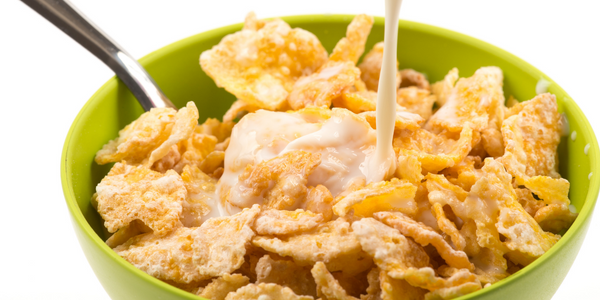
Case Study
The Kellogg Company
Kellogg keeps a close eye on its trade spend, analyzing large volumes of data and running complex simulations to predict which promotional activities will be the most effective. Kellogg needed to decrease the trade spend but its traditional relational database on premises could not keep up with the pace of demand.
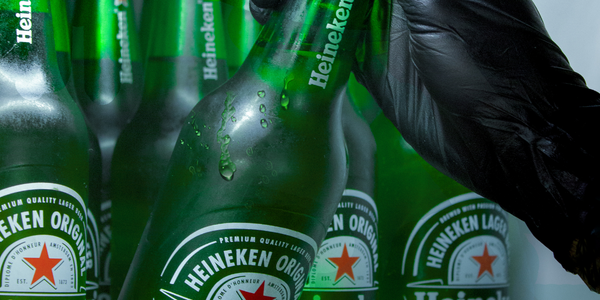
Case Study
HEINEKEN Uses the Cloud to Reach 10.5 Million Consumers
For 2012 campaign, the Bond promotion, it planned to launch the campaign at the same time everywhere on the planet. That created unprecedented challenges for HEINEKEN—nowhere more so than in its technology operation. The primary digital content for the campaign was a 100-megabyte movie that had to play flawlessly for millions of viewers worldwide. After all, Bond never fails. No one was going to tolerate a technology failure that might bruise his brand.Previously, HEINEKEN had supported digital media at its outsourced datacenter. But that datacenter lacked the computing resources HEINEKEN needed, and building them—especially to support peak traffic that would total millions of simultaneous hits—would have been both time-consuming and expensive. Nor would it have provided the geographic reach that HEINEKEN needed to minimize latency worldwide.
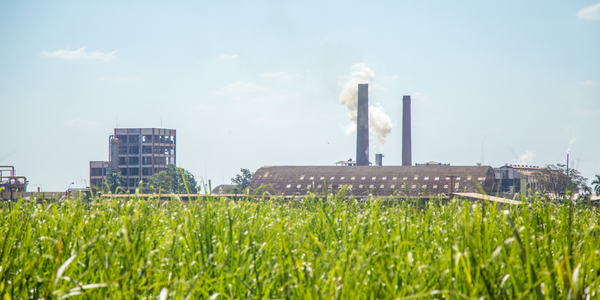
Case Study
Energy Management System at Sugar Industry
The company wanted to use the information from the system to claim under the renewable energy certificate scheme. The benefit to the company under the renewable energy certificates is Rs 75 million a year. To enable the above, an end-to-end solution for load monitoring, consumption monitoring, online data monitoring, automatic meter data acquisition which can be exported to SAP and other applications is required.
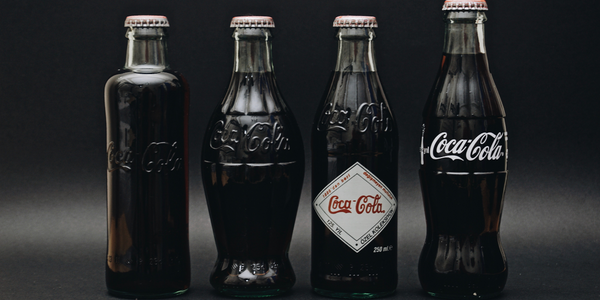
Case Study
Coca Cola Swaziland Conco Case Study
Coco Cola Swaziland, South Africa would like to find a solution that would enable the following results: - Reduce energy consumption by 20% in one year. - Formulate a series of strategic initiatives that would enlist the commitment of corporate management and create employee awareness while helping meet departmental targets and investing in tools that assist with energy management. - Formulate a series of tactical initiatives that would optimize energy usage on the shop floor. These would include charging forklifts and running cold rooms only during off-peak periods, running the dust extractors only during working hours and basing lights and air-conditioning on someone’s presence. - Increase visibility into the factory and other processes. - Enable limited, non-intrusive control functions for certain processes.