下载PDF
Faraone's Innovative Approach to Architectural Component Design with IoT
技术
- 分析与建模 - 数字孪生/模拟
- 传感器 - 电表
适用行业
- 玻璃
- 生命科学
适用功能
- 产品研发
- 质量保证
用例
- 时间敏感网络
- 虚拟现实
服务
- 测试与认证
挑战
Faraone SRL 是一家意大利建筑构件供应商,面临着设计新型全玻璃栏杆的挑战,栏杆底部采用特殊的铝型材以将玻璃结构固定到位。目标是节省开发时间、材料和生产成本,同时提高铝型材的刚度。 Faraone 的开发工程师需要新的设计策略和特殊的优化工具来帮助实现这些目标。栏杆等建筑构件的设计可能具有挑战性,因为设计不仅必须美观,还必须满足多项安全要求和标准。此外,所有设计都必须在尽可能短的时间内开发出来。为了应对这些挑战,Faraone 的工程师、建筑师和设计师一直在寻找能够缩短设计和测试周期的解决方案。
关于客户
Faraone SRL 是一家意大利建筑组件供应商。公司致力于不断投资最先进的分析工具、技术研究和新的创新产品的开发。设计在所有 Faraone 新产品中发挥着基础作用,设计师和工程师团队合作,为每款新产品寻找更智能的解决方案。该公司以其对质量和创新的承诺以及满足建筑行业挑战性需求的能力而闻名。 Faraone 最近的项目涉及设计一个新的全玻璃栏杆,底部有一个特殊的铝型材,用于将玻璃结构固定到位。
解决方案
Faraone 通过 SolidThinking Inspire 找到了解决方案,这是一款设计软件,可以在一个平台上进行结构优化和验证。工程团队从零开始,利用仿真和优化来驱动设计。他们首先创建了一个简单的配置文件,并使用它在solidThinking Inspire 中执行配置文件的拓扑优化。优化结果启发了最终设计,设计团队对最终设计进行了完善,最后在solidThinking Inspire 中进行了验证。典型的优化过程遵循以下步骤: 创建设计空间以及应用载荷和边界条件。优化工具使用输入来提出最佳结构。该设计方案提供了轻量化和结构效率的最佳组合。随后,快速完善零件以定义最终形状,然后再次使用 Inspire 进行分析以验证其结构性能。
运营影响
数量效益
相关案例.
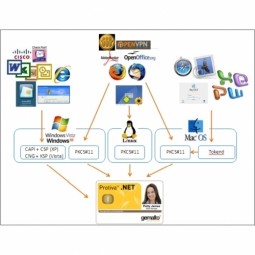
Case Study
Corporate Identity Solution Adds Convenience to Beckman Coulter
Beckman Coulter wanted to implement a single factor solution for physical and remote logical access to corporate network. Bechman Coulter's users were carrying smart card badges for doors, but also needed a one-time password token to access to our corporate network when they were not in the office. They wanted to simplify the process.
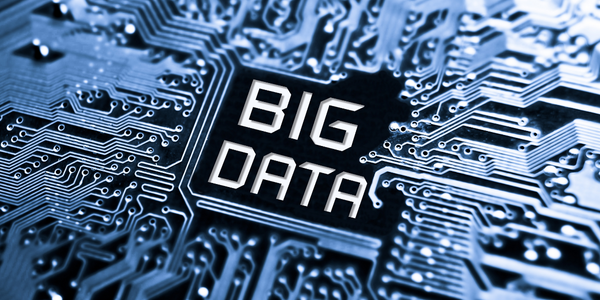
Case Study
Embracing Business Success in Real Time
· Increase control over growing Big Data to improve business decisions · Manage data for 28,000 biotechnology stockkeeping units in the fields of microbiology, molecular biology, animal cell cultures, plant tissue cultures, and lab ware for laboratory chemicals · Accelerate report generation and analysis with real-time data
.png)
Case Study
Discrete Manufacturing Industries (Fiberglass Pipe)
The implementation of ERP software in a Discrete Manufacturing organization needs to be strategic, irrespective of its size and capacity. The client had already implemented an ERP system which fulfilled their requirements but was not efficient enough. Efficiency here meant Synchronized Planning, Updating and Multisite Planning. Planning at client’s place was done outside the ERP system. Lack of proper synchronization to the ERP system paved way to huge delays in the changes getting updated in the system. These delays caused disruption in achieving delivery schedules. Multisite Planning is a solution to an organization which has multiple production units (may or may not be geographically separated) and thus needs planning across these units to synchronize production activities within them. The client also has multiple factories and hence Production Planning control is very essential in their case. Since Multisite planning was not possible with Baan ERP system, this was another bottleneck for the client.
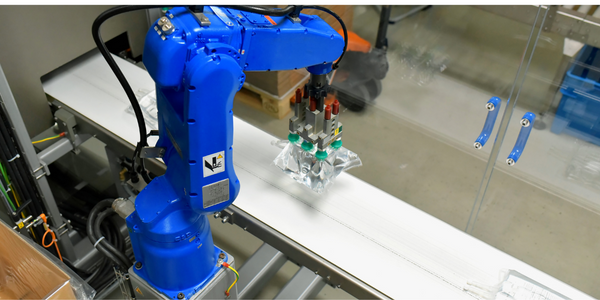
Case Study
Flow Robotics: Scaling Up Production and Accelerating Product Development with IoT
Flow Robotics, a Danish manufacturer, developed flowbot™ ONE pipetting robots to alleviate the strain on bioanalysts in life-science laboratories and hospitals across Europe. These robots were designed to automate part of the testing process, speeding up the time it takes to produce results and reducing pressure on staff. However, the company faced challenges in scaling up production and accelerating product development. High workloads and physically challenging conditions have long been an issue for laboratory professionals. Flow Robotics estimates that around half of medical lab technicians carry out the same arm movements for at least a quarter of their working day. The American Society for Clinical Pathology reported that 85% of laboratory professionals feel burnt out; 36% struggle with inadequate staffing; and 32% face a heavy workload and pressure to complete all testing on time.

Case Study
Asia Airfreight Terminal Enhances Operational Efficiency with CommScope's RUCKUS Solutions
Asia Airfreight Terminal (AAT), a leading cargo handling company based out of Hong Kong International Airport, was facing challenges with its Wi-Fi network, which was critical for the functioning of its automated Material Handling System (MHS) within the warehouse. Any interference or lost signals could directly impact their operational efficiency. AAT also had separate networks for their office and CCTV cameras, which made the job of their data center challenging. The company was in search of a Wi-Fi network configuration that could streamline their networks and reduce its network management workload. AAT was already running on equipment from a competing vendor, and the new solution needed to prove its worth in scalability and reliability.
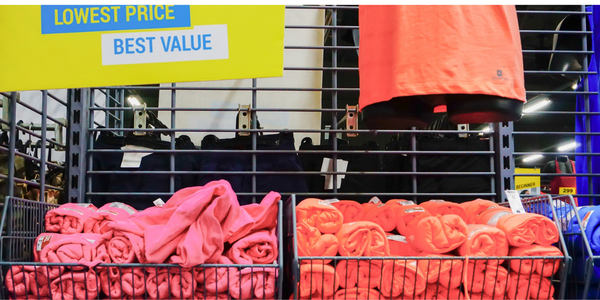
Case Study
High Density Stacking Capability Enhances Productivity in 3D Part Production at Decathlon
Decathlon, the world’s largest sporting goods retailer, was faced with a mold injection problem on a small component for shooting glasses that connects the frame to the lenses. The company was seeking a solution that would avoid the expense of tooling and increase efficiency in production. They decided to test the new 3D stacking solution developed by 3D Systems to evaluate additive manufacturing for production. After conducting a feasibility study on the Figure 4 solution and stacking feature, Decathlon’s teams confirmed the productivity and economics of additive manufacturing and decided that this solution could be considered for batch-run production of the final product.