下载PDF
Fuelling Conversation: How Springworks got cars talking with SPARK and created an app that’s become a standard on Swedish phones
技术
- 平台即服务 (PaaS) - 连接平台
- 分析与建模 - 实时分析
适用行业
- 汽车
- 电信
适用功能
- 物流运输
- 维护
用例
- 车载远程信息处理
- 车队管理
- 预测性维护
服务
- 云规划/设计/实施服务
- 数据科学服务
挑战
Springworks launched SPARK, a platform that lets car owners receive key data about their vehicles at the touch of a button, served straight from the cloud, direct to their smartphones. The platform also connects them with service providers that can sort any issues that might come up – from MOTs to tyre changes. However, each talking car generates about 10,000 data points per day. To handle 20 million cars, Springworks needed a system that could handle several billion data points in one go. They wanted limitless scale. In order to hit the market with a great new product, Springworks needed to be able to focus on innovation. When they started out, the release cycle as about 2 weeks for a new feature – but the team wanted to move faster. Finally, data security was a major concern. For a new market offer that was looking to partner with the big mobile networks, security couldn’t be an afterthought. It had to be built into the SPARK infrastructure from the start.
关于客户
Springworks is a company with a background in gaming. They launched SPARK, a platform that lets car owners receive key data about their vehicles at the touch of a button, served straight from the cloud, direct to their smartphones. The platform also connects them with service providers that can sort any issues that might come up – from MOTs to tyre changes. Springworks also had an ambition – 20 million talking cars in Europe by 2020. They wanted to create a system that could handle several billion data points in one go and wanted limitless scale. They also wanted to focus on innovation and needed to ensure data security.
解决方案
Springworks turned to AWS. They used Elastic Load Balancing and Autoscaling to manage their powerful APIs. This allowed them to scale without limits, regardless of whether they had a hundred or a million cars talking at once. The workload dropped instantly and the entire platform could be operated by a team of 30 instead of 3,000, which eliminated the need for an operations department. They used Lambda and SNS to automate responses to events. This allowed them to focus on innovation and accelerate releases by something like 300%. Instead of one feature every two weeks, they’re now shipping two features weekly. Finally, they used services like CloudTrail and EC2 to build a secure, compliance-friendly infrastructure.
运营影响
数量效益
相关案例.
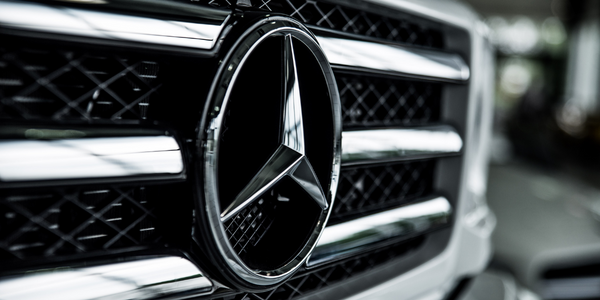
Case Study
Integral Plant Maintenance
Mercedes-Benz and his partner GAZ chose Siemens to be its maintenance partner at a new engine plant in Yaroslavl, Russia. The new plant offers a capacity to manufacture diesel engines for the Russian market, for locally produced Sprinter Classic. In addition to engines for the local market, the Yaroslavl plant will also produce spare parts. Mercedes-Benz Russia and his partner needed a service partner in order to ensure the operation of these lines in a maintenance partnership arrangement. The challenges included coordinating the entire maintenance management operation, in particular inspections, corrective and predictive maintenance activities, and the optimizing spare parts management. Siemens developed a customized maintenance solution that includes all electronic and mechanical maintenance activities (Integral Plant Maintenance).
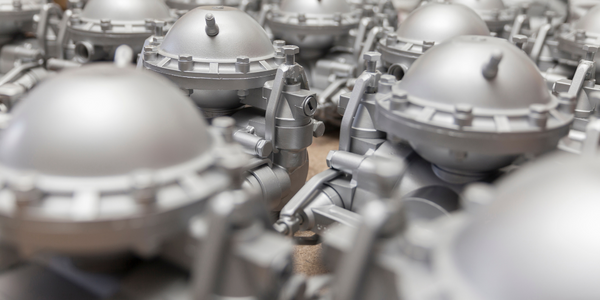
Case Study
Monitoring of Pressure Pumps in Automotive Industry
A large German/American producer of auto parts uses high-pressure pumps to deburr machined parts as a part of its production and quality check process. They decided to monitor these pumps to make sure they work properly and that they can see any indications leading to a potential failure before it affects their process.