下载PDF
Greenfield Speed to MES Delivers First Round Win
技术
- 功能应用 - 制造执行系统 (MES)
适用行业
- 电子产品
适用功能
- 离散制造
用例
- 自动化制造系统
服务
- 系统集成
- 软件设计与工程服务
挑战
HT Micron, a semiconductor facility in São Leopoldo Brazil, needed to implement a manufacturing execution system (MES) within two months to meet the demands of Tier 1 international customers. The company was starting up in a country with no industry experience and no MES consultants with semiconductor experience. The MES was critical for the company to get on the approved vendor list of global Tier 1 customers and to stay efficient and flexible as their volume and product mix grow. The company also faced the challenge of training every employee and getting to market rapidly.
关于客户
HT Micron is a joint venture between PARIT group of Brazil and Hana Micron of South Korea. The company has invested over R$ 165 million to build the largest semiconductor facility in Latin America. The plant, which includes 7,500 m² of cleanroom, has the capacity to create over 800 direct jobs. The company currently occupies over 3,000 m² for IC assembly and component test. This space also includes a Class 100k cleanroom for sister company Teikon’s SMT and module / SSD test lines. With enough people to manage, oversee, and run several dozen wire bonders, plus wafer sawing, die attach, molding, marking, etc. this is not a small or simple new facility.
解决方案
HT Micron selected a modern MES from an experienced company and used core functions out of the box with minor customization. The company licensed a core MES platform to model the plant and store data plus WIP, equipment, durables, consumables, carrier tracking, dispatching, on-line visualization, engineering data analysis, reporting, SPC. The MES supplier installed the software and created specific routing rules, parameter-based automatic actions and specific reports. All production was tracked in the MES from January 1, 2015. The company is planning to expand the team’s knowhow with the MES and add automation, maintenance and other modern MES functions in the future.
运营影响
数量效益
相关案例.
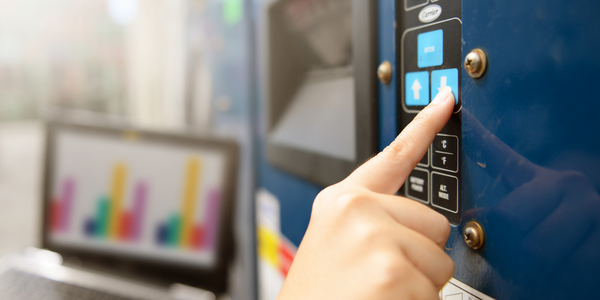
Case Study
Remote Temperature Monitoring of Perishable Goods Saves Money
RMONI was facing temperature monitoring challenges in a cold chain business. A cold chain must be established and maintained to ensure goods have been properly refrigerated during every step of the process, making temperature monitoring a critical business function. Manual registration practice can be very costly, labor intensive and prone to mistakes.
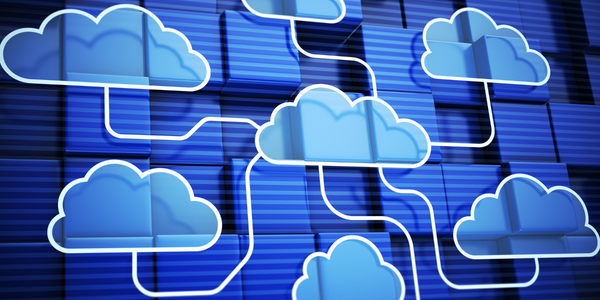
Case Study
Cloud Solution for Energy Management Platform-Schneider Electric
Schneider Electric required a cloud solution for its energy management platform to manage high computational operations, which were essential for catering to client requirements. As the business involves storage and analysis of huge amounts of data, the company also needed a convenient and scalable storage solution to facilitate operations efficiently.
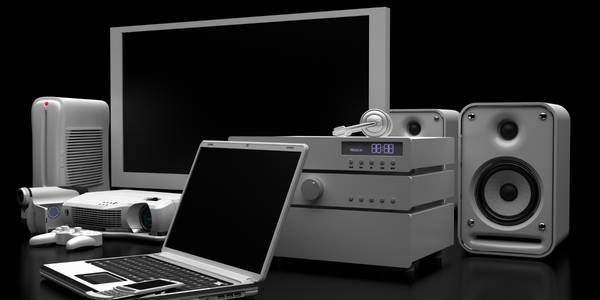
Case Study
Leveraging the IoT to Gain a Competitive Edge in International Competition
Many large manufacturers in and outside Japan are competing for larger market share in the same space, expecting a growing demand for projectors in the areas of entertainment, which requires glamor and strong visual performance as well as digital signage that can attract people’s attention. “It is becoming more and more difficult to differentiate ourselves with stand-alone hardware products,” says Kazuyuki Kitagawa, Director of Service & Support at Panasonic AVC Networks. “In order for Panasonic to grow market share and overall business, it is essential for us to develop solutions that deliver significant added value.” Panasonic believes projection failure and quality deterioration should never happen. This is what and has driven them to make their projectors IoT-enabled. More specifically, Panasonic has developed a system that collects data from projectors, visualizes detailed operational statuses, and predicts issues and address them before failure occurs. Their projectors are embedded with a variety of sensors that measure power supply, voltage, video input/ output signals, intake/exhaust air temperatures, cooling fan operations, and light bulb operating time. These sensors have been used to make the projector more intelligent, automatically suspending operation when the temperature rises excessively, and automatically switching light bulbs. Although this was a great first step, Panasonic projectors were still not equipped with any capability to send the data over a network.