下载PDF
Harnessing Large, Heterogenous Datasets to Improve Manufacturing Process
技术
- 分析与建模 - 机器学习
- 分析与建模 - 预测分析
适用功能
- 维护
- 离散制造
用例
- 预测性维护
- 机器状态监测
服务
- 数据科学服务
挑战
领先的眼科光学公司 Essilor International 面临着改进表面处理机的流程和性能以大幅提高产量的挑战。镜片制造中的表面处理步骤复杂而精细,因为它赋予镜片光学功能。该公司旨在优化此步骤以符合每个人的个人处方和个人参数。然而,他们正在处理来自表面处理机的大量异构数据集,需要一种可扩展的方式来处理这些数据。该公司已经在使用物联网连接设备等持续监控技术,但他们希望更进一步,采用先进的算法和机器学习,根据实时洞察采取行动。
关于客户
依视路国际是世界领先的眼科光学公司。该公司设计、制造和销售各种镜片,以改善和保护视力。依视路在全球拥有 67,000 名员工,拥有 34 家工厂、481 个处方实验室和磨边设施,以及全球 4 个研发中心。该公司的核心业务是生产眼科镜片。依视路致力于确保工厂高效、创新并遵守高质量标准,拥有全球工程 (GE) 服务,负责实施和标准化生产流程。
解决方案
Essilor 选择 Dataiku 数据科学工作室 (DSS) 来帮助他们有效处理来自表面处理机器的大量数据。Dataiku 的设置和实施非常简单,使他们能够快速上手。该工具使他们能够探索、分析和创建预测模型,每个人都可以使用这些模型,从专业专家到机器操作员、数据科学家和 IT。Dataiku 还使他们能够高效、有效地管理来自表面处理机器的数据变化。该团队能够快速测试和迭代用例,以更快地找到解决方案。他们还欣赏使用代码或使用点击式可视化界面的灵活性,无论哪种方式都能让他们更快地工作。
运营影响
数量效益
相关案例.
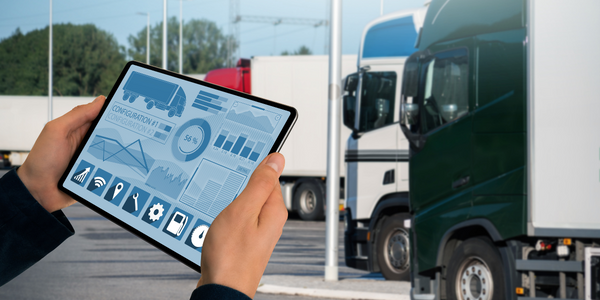
Case Study
IoT enabled Fleet Management with MindSphere
In view of growing competition, Gämmerler had a strong need to remain competitive via process optimization, reliability and gentle handling of printed products, even at highest press speeds. In addition, a digitalization initiative also included developing a key differentiation via data-driven services offers.
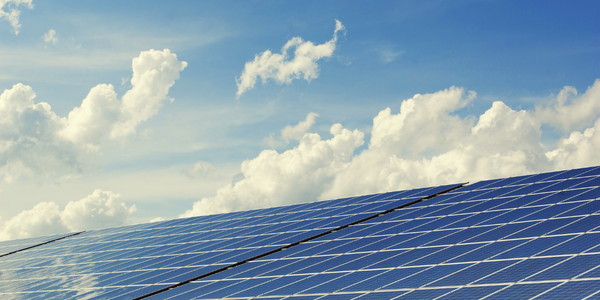
Case Study
Remote Monitoring & Predictive Maintenance App for a Solar Energy System
The maintenance & tracking of various modules was an overhead for the customer due to the huge labor costs involved. Being an advanced solar solutions provider, they wanted to ensure early detection of issues and provide the best-in-class customer experience. Hence they wanted to automate the whole process.
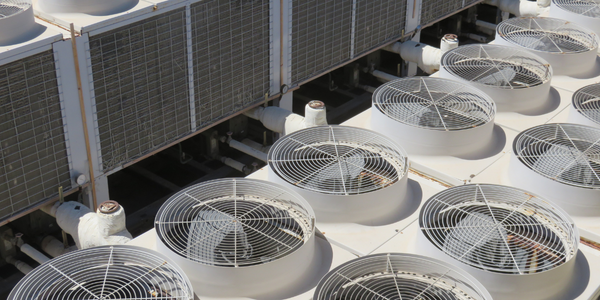
Case Study
Predictive Maintenance for Industrial Chillers
For global leaders in the industrial chiller manufacturing, reliability of the entire production process is of the utmost importance. Chillers are refrigeration systems that produce ice water to provide cooling for a process or industrial application. One of those leaders sought a way to respond to asset performance issues, even before they occur. The intelligence to guarantee maximum reliability of cooling devices is embedded (pre-alarming). A pre-alarming phase means that the cooling device still works, but symptoms may appear, telling manufacturers that a failure is likely to occur in the near future. Chillers who are not internet connected at that moment, provide little insight in this pre-alarming phase.
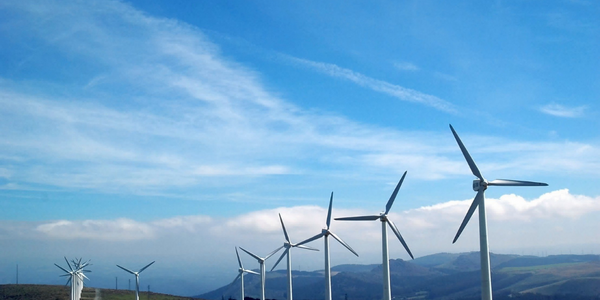
Case Study
Siemens Wind Power
Wind provides clean, renewable energy. The core concept is simple: wind turbines spin blades to generate power. However, today's systems are anything but simple. Modern wind turbines have blades that sweep a 120 meter circle, cost more than 1 million dollars and generate multiple megawatts of power. Each turbine may include up to 1,000 sensors and actuators – integrating strain gages, bearing monitors and power conditioning technology. The turbine can control blade speed and power generation by altering the blade pitch and power extraction. Controlling the turbine is a sophisticated job requiring many cooperating processors closing high-speed loops and implementing intelligent monitoring and optimization algorithms. But the real challenge is integrating these turbines so that they work together. A wind farm may include hundreds of turbines. They are often installed in difficult-to-access locations at sea. The farm must implement a fundamentally and truly distributed control system. Like all power systems, the goal of the farm is to match generation to load. A farm with hundreds of turbines must optimize that load by balancing the loading and generation across a wide geography. Wind, of course, is dynamic. Almost every picture of a wind farm shows a calm sea and a setting sun. But things get challenging when a storm goes through the wind farm. In a storm, the control system must decide how to take energy out of gusts to generate constant power. It must intelligently balance load across many turbines. And a critical consideration is the loading and potential damage to a half-billion-dollar installed asset. This is no environment for a slow or undependable control system. Reliability and performance are crucial.
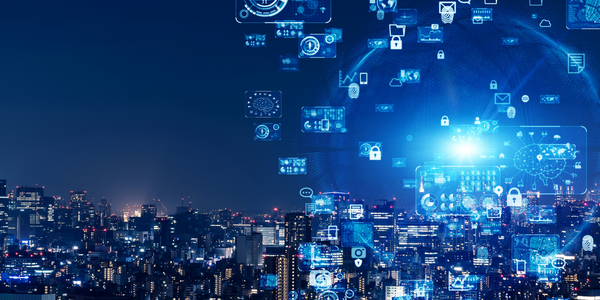
Case Study
Integration of PLC with IoT for Bosch Rexroth
The application arises from the need to monitor and anticipate the problems of one or more machines managed by a PLC. These problems, often resulting from the accumulation over time of small discrepancies, require, when they occur, ex post technical operations maintenance.
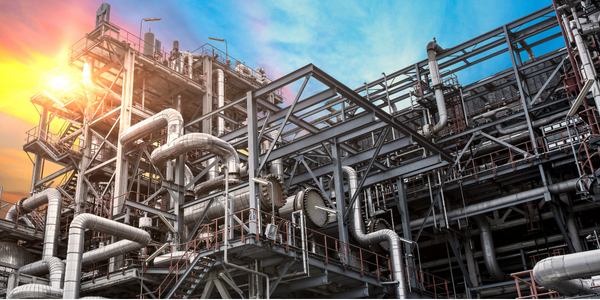
Case Study
Refinery Saves Over $700,000 with Smart Wireless
One of the largest petroleum refineries in the world is equipped to refine various types of crude oil and manufacture various grades of fuel from motor gasoline to Aviation Turbine Fuel. Due to wear and tear, eight hydrogen valves in each refinery were leaking, and each cost $1800 per ton of hydrogen vented. The plant also had leakage on nearly 30 flare control hydrocarbon valves. The refinery wanted a continuous, online monitoring system that could catch leaks early, minimize hydrogen and hydrocarbon production losses, and improve safety for maintenance.