下载PDF
Heico Calls on AI to Predict & Prevent Potentially Serious Injuries and Fatalities (pSIFs)
技术
- 分析与建模 - 机器学习
- 分析与建模 - 大数据分析
适用行业
- 建筑与基础设施
- 金属
适用功能
- 维护
- 质量保证
用例
- 预测性维护
- 机器状态监测
- 根因分析与诊断
服务
- 数据科学服务
- 系统集成
挑战
The Heico Companies, a holding company with a diverse industrial portfolio, was facing challenges in identifying and managing Serious Injuries and Fatalities (SIFs) across its various firms. Traditional approaches to reducing SIF potential, such as Heinrich’s Safety Triangle, were proving inadequate as they often misidentified the fundamental issues causing SIF events. The company needed a more nuanced method to reduce SIF rates, especially given its global presence and mixed portfolio. The challenge was to identify tasks with high potential for SIFs rather than focusing on more common severe or non-injury events. Additionally, the company needed to understand industry or region-specific workplace situations with high SIF potential.
关于客户
The Heico Companies is a holding company with a diverse industrial portfolio. It owns more than 70 firms operating at different risk levels, including metal processing, construction, and industrial technologies. The company operates across mixed verticals in multiple regions, making the management of Serious Injuries and Fatalities (SIFs) particularly challenging. The company needed a comprehensive approach to reducing SIF and potentially Serious Injuries and Fatalities (pSIF) events across varied industries and geographies.
解决方案
To address these challenges, Heico implemented the Benchmark pSIF AI Advisor, a tool developed by Benchmark Digital Partners and Bowers Management Analytics. This tool uses Machine Learning and advanced data analysis to identify potentially Serious Injuries and Fatalities (pSIFs). The AI Advisor was implemented through a one-time data analysis of 20,000 data points between 2018 and 2020, identifying 699 pSIFs with 95% accuracy. These findings were incorporated into Heico's firm-wide plan for continuous improvement in dealing with the root causes of pSIFs. The AI Advisor provides a holistic, firm-wide approach to tracking, identifying, and minimizing pSIFs through standardized data analysis. This allows for more actionable insights compared with traditional methods.
运营影响
数量效益
相关案例.
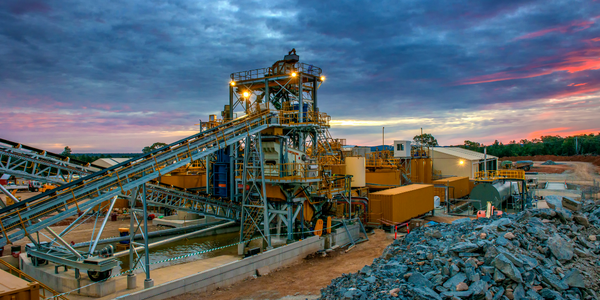
Case Study
Goldcorp: Internet of Things Enables the Mine of the Future
Goldcorp is committed to responsible mining practices and maintaining maximum safety for its workers. At the same time, the firm is constantly exploring ways to improve the efficiency of its operations, extend the life of its assets, and control costs. Goldcorp needed technology that can maximize production efficiency by tracking all mining operations, keep employees safe with remote operations and monitoring of hazardous work areas and control production costs through better asset and site management.
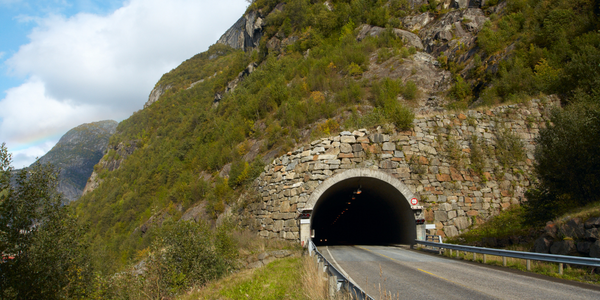
Case Study
IoT System for Tunnel Construction
The Zenitaka Corporation ('Zenitaka') has two major business areas: its architectural business focuses on structures such as government buildings, office buildings, and commercial facilities, while its civil engineering business is targeted at structures such as tunnels, bridges and dams. Within these areas, there presented two issues that have always persisted in regard to the construction of mountain tunnels. These issues are 'improving safety" and "reducing energy consumption". Mountain tunnels construction requires a massive amount of electricity. This is because there are many kinds of electrical equipment being used day and night, including construction machinery, construction lighting, and ventilating fan. Despite this, the amount of power consumption is generally not tightly managed. In many cases, the exact amount of power consumption is only ascertained when the bill from the power company becomes available. Sometimes, corporations install demand-monitoring equipment to help curb the maximum power demanded. However, even in these cases, the devices only allow the total volume of power consumption to be ascertained, or they may issue warnings to prevent the contracted volume of power from being exceeded. In order to tackle the issue of reducing power consumption, it was first necessary to obtain an accurate breakdown of how much power was being used in each particular area. In other words, we needed to be able to visualize the amount of power being consumed. Safety, was also not being managed very rigorously. Even now, tunnel construction sites often use a 'name label' system for managing entry into the work site. Specifically, red labels with white reverse sides that bear the workers' names on both sides are displayed at the tunnel work site entrance. The workers themselves then flip the name label to the appropriate side when entering or exiting from the work site to indicate whether or not they are working inside the tunnel at any given time. If a worker forgets to flip his or her name label when entering or exiting from the tunnel, management cannot be performed effectively. In order to tackle the challenges mentioned above, Zenitaka decided to build a system that could improve the safety of tunnel construction as well as reduce the amount of power consumed. In other words, this new system would facilitate a clear picture of which workers were working in each location at the mountain tunnel construction site, as well as which processes were being carried out at those respective locations at any given time. The system would maintain the safety of all workers while also carefully controlling the electrical equipment to reduce unnecessary power consumption. Having decided on the concept, our next concern was whether there existed any kind of robust hardware that would not break down at the construction work site, that could move freely in response to changes in the working environment, and that could accurately detect workers and vehicles using radio frequency identification (RFID). Given that this system would involve many components that were new to Zenitaka, we decided to enlist the cooperation of E.I.Sol Co., Ltd. ('E.I.Sol') as our joint development partner, as they had provided us with a highly practical proposal.
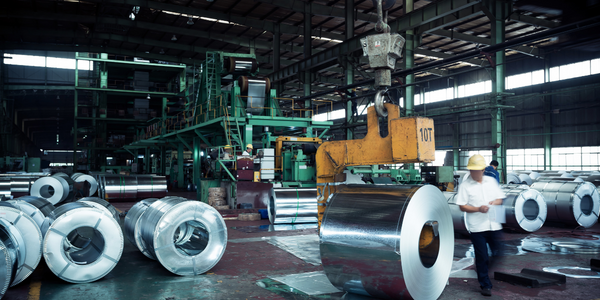
Case Study
KSP Steel Decentralized Control Room
While on-site in Pavlodar, Kazakhstan, the DAQRI team of Business Development and Solutions Architecture personnel worked closely with KSP Steel’s production leadership to understand the steel production process, operational challenges, and worker pain points.
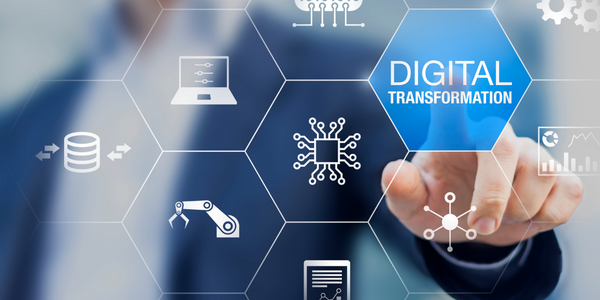
Case Study
Bluescope Steel on Path to Digitally Transform Operations and IT
Increasing competition and fluctuations in the construction market prompted BlueScope Steel to look toward digital transformation of its four businesses, including modern core applications and IT infrastructure. BlueScope needed to modernize its infrastructure and adopt new technologies to improve operations and supply chain efficiency while maintaining and updating an aging application portfolio.
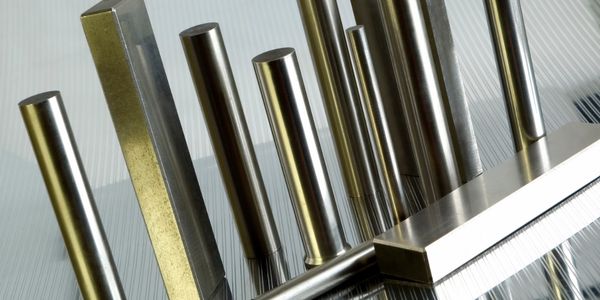
Case Study
RobotStudio Case Study: Benteler Automobiltechnik
Benteler has a small pipe business area for which they produce fuel lines and coolant lines made of aluminum for Porsche and other car manufacturers. One of the problems in production was that when Benteler added new products, production had too much downtime.
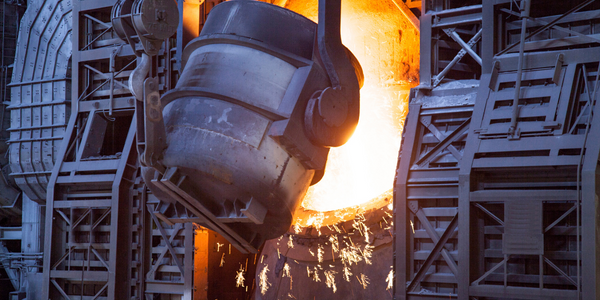
Case Study
Continuous Casting Machines in a Steel Factory
With a very broad range of applications, steel is an important material and has been developed into the most extensive alloy in the engineering world. Since delivering high quality is absolutely crucial for steel plants, ensuring maximum productivity and the best quality production are the keys to competitiveness in the steel industry. Additionally, working conditions in steel factories are not suitable for workers to stay in for long periods of time, so manufactures usually adopt various machines to complete the steel production processes. However, the precision of these machines is often overestimated and the lack of flexibility also makes supervisors unable to adjust operating procedures. A renowned steel factory in Asia planned to improve its Distributed Control System (DCS) of furnaces as well as addressing the problem of insufficient accuracy. However, most well-known international equipment suppliers can not provide a satisfactory solution and local maintenance because the project needed new technologies to more accurately control equipment operations. By implementing Advantech’s automated monitoring and control solution, steel factories can not only improve the manufacturing processes but can also allow users to add additional functions to the existing system so as to make sure the operation runs at high efficiency.