下载PDF
How Advantech’s Solutions for Yeefung’s Automated Guided Vehicles Help Turn Traditional Factories into Smart Factories
技术
- 自动化与控制 - 自动化与过程控制系统
- 机器人 - 自动导引车 (AGV)
适用功能
- 离散制造
- 仓库和库存管理
用例
- 工厂可见化与智能化
- 自动化制造系统
- 仓库自动化
服务
- 系统集成
- 软件设计与工程服务
挑战
怡丰机器人科技是中国领先的综合自动导引车 (AGV) 和革命性停车解决方案提供商,该公司正在寻求全面的硬件和 AGV 控制器解决方案。该公司希望利用工业 4.0 的优势,确保机器人和 AGV 以最高效率工作,几乎没有停机时间,从而降低成本并增加利润。然而,为了确保全面监控和灵活性,智能工厂 AGV 必须以传统可编程逻辑控制器 (PLC) 无法处理的速度执行多项算术运算。
关于客户
深圳怡丰机器人技术有限公司成立于 2014 年,是中国领先的综合自动导引车 (AGV) 和革命性停车解决方案供应商。该公司开发了采用研华无线 AGV 解决方案的尖端 AGV 系统。结合传感器、无线网络和激光导航等不断发展的技术,怡丰扩展了其 AGV 系统的多功能性,可用于智能工厂和智能停车。事实证明,这些解决方案不仅仅是基本的自动化工具,还为智能工厂 AGV 提供了全面的监控和灵活性。
解决方案
研华为怡丰提供了一系列解决方案,包括无线 AGV 解决方案和基于 PC 的 UNO2272G 嵌入式自动化计算机。UNO-2272G 配备 Intel® Atom™ J1900 处理器、无线通信模块 (PCM-24S2WF) 和 CANbus 模块 (PCM26D2CA),可接收来自中央调度系统的命令,并快速处理从 AGV 的防撞传感器、360 度激光发射器和磁钉扫描仪收集的数据,以快速计算 AGV 的停车位置和行驶路径。所使用的其他研华解决方案包括 EKI7710E-2C 管理型以太网交换机、WISE-5121 Wi-Fi AP/客户端和 FPM-7061T VGA 工业显示器。这些解决方案使怡丰能够生产出最先进的 AGV 系统,具有广泛的智能工厂功能,例如指令发布、行进轨迹和位置监控、系统健康诊断和自动调度。
运营影响
数量效益
相关案例.
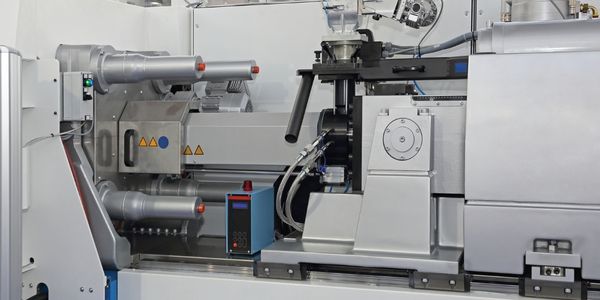
Case Study
Plastic Spoons Case study: Injection Moulding
In order to meet customer expectations by supplying a wide variety of packaging units, from 36 to 1000 spoons per package, a new production and packaging line needed to be built. DeSter wanted to achieve higher production capacity, lower cycle time and a high degree of operator friendliness with this new production line.
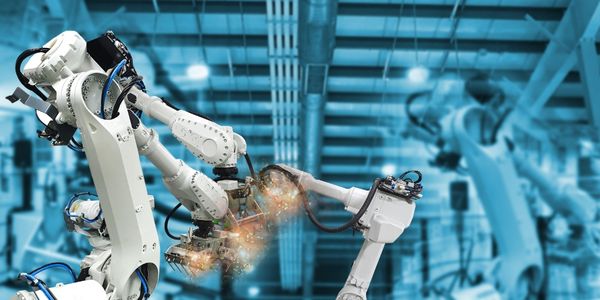
Case Study
Robot Saves Money and Time for US Custom Molding Company
Injection Technology (Itech) is a custom molder for a variety of clients that require precision plastic parts for such products as electric meter covers, dental appliance cases and spools. With 95 employees operating 23 molding machines in a 30,000 square foot plant, Itech wanted to reduce man hours and increase efficiency.
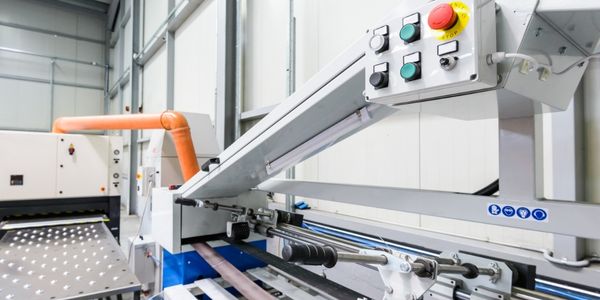
Case Study
Fully Automated Visual Inspection System
Tofflon has developed a fully automatic machine that uses light to inspect vials, medicine bottles, or infusion containers for glass fragments, aluminum particles, rubber grains, hairs, fibers, or other contaminants. It also detects damaged containers with cracks or inclusions (microscopic imperfections), automatically removing faulty or contaminated products. In order to cover all production processes for freeze-dried pharmaceuticals, Tofflon needed to create an open, consistent, and module-based automation concept.

Case Study
IoT Solution for Cold Chain
Most of the customer's warehouses run on utility and generator power. Since these warehouses are in remote locations, power outages are a very common scenario. Diesel fuel, thereby, becomes a significant cost for these warehouses. Energy consumption was also very high due to the lack of a consistent temperature throughout the facility. This lack of a consistent temperature in all areas and no way to control it, resulted in the customer losing a significant amount of their temperature sensitive goods due to spoilage.
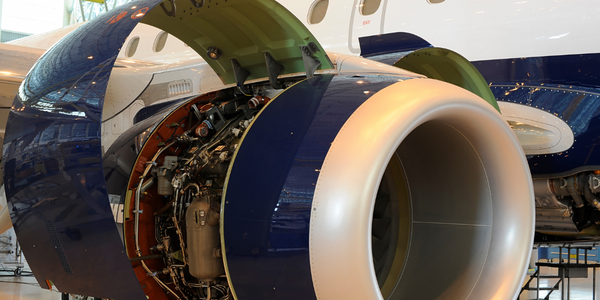
Case Study
Accelerate Production for Spirit AeroSystems
The manufacture and assembly of massive fuselage assemblies and other large structures generates a river of data. In fact, the bill of materials for a single fuselage alone can be millions of rows of data. In-house production processes and testing, as well as other manufacturers and customers created data flows that overwhelmed previous processes and information systems. Spirit’s customer base had grown substantially since their 2005 divestiture from Boeing, resulting in a $41 billion backlog of orders to fill. To address this backlog, meet increased customer demands and minimize additional capital investment, the company needed a way to improve throughput in the existing operational footprint. Spirit had a requirement from customers to increase fuselage production by 30%. To accomplish this goal, Spirit needed real-time information on its value chain and workflow. However, the two terabytes of data being pulled from their SAP ECC was unmanageable and overloaded their business warehouse. It had become time-consuming and difficult to pull aggregate data, disaggregate it for the needed information and then reassemble to create a report. During the 6-8 hours it took to build a report, another work shift (they run three per day) would have already taken place, thus the report content was out-of-date before it was ever delivered. As a result, supervisors often had to rely on manual efforts to provide charts, reports and analysis.
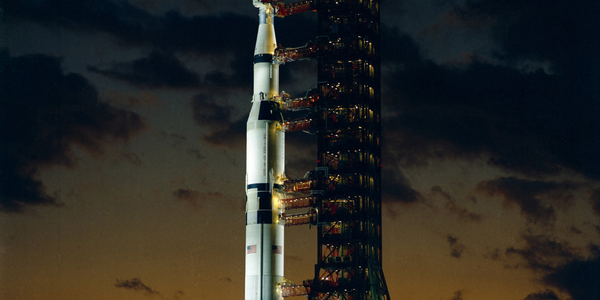
Case Study
SAP Leonardo Enabling Rocket Science
At times, ULA has as many as 15 different operating systems dedicated to overlapping processes, such as rocket design, testing, and launch. Multiple systems created unnecessary costs and unwanted confusion among workers at offices, factories, and launch sites in different location. In order to improve collaboration and transparency during vital activities that directly influence mission success, ULA wanted to improve data sharing and streamline manufacturing processes.