下载PDF
Improving Recycling Collection Performance
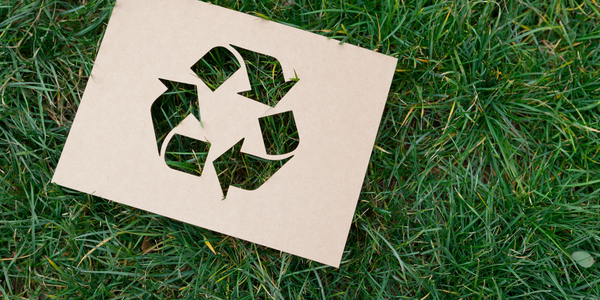
技术
- 功能应用 - 远程监控系统
- 传感器 - 液位传感器
适用功能
- 物流运输
用例
- 过程控制与优化
- 资产跟踪
挑战
2015 年,HFTH、纽约西部捐赠物品联盟 (WNYCDG) 和布法罗市的成员转移了 4,800 吨不需要的衣物和纺织品以供重复使用。在消费主义日益增长的时代,HFTH 的雄心是为无家可归者提供更大的支持。其管理团队的目标是扩大其回收和收集能力,以实现其运营中的垃圾零填埋。 HFTH 成立于 1990 年,最初是在 WNY 地区周围的少量回收收集容器。 HFTH 的首席运营官兼公司秘书 Nick Calandra 在描述这些集装箱的管理时说:“我们亲自检查了每个集装箱,很容易记住位置和估计填充速度,以便组织我们的卡车路线和收集。”然而,随着组织的发展和收集点分布在更广泛的区域,人工物流计划变得更加复杂,效率下降。它达到了容器在只有 30% 满时被清空的地步,仅仅是因为它们位于常规收集路线上。 HFTH 寻求一种解决方案,使他们能够扩大运营规模、优化收集,并尽可能自动调整路线以最大限度地提高收集效率。
客户
无家可归者的心
关于客户
Hearts for the Homeless (HFTH) 是该地区循环经济的主要推动力。 HFTH 开展服装和纺织品回收计划,从纽约西部 (WNY) 地区收集废物。他们通过他们的 th 回收那些用过很少的衣服
解决方案
在对市场进行调查后,Enevo 于 2014 年被选中,并在整个运营过程中在精心挑选的多个集装箱站点上部署了传感器。结果证明了该技术的可靠性和易用性,其中包括每个收集容器中的无线填充水平传感器,将数据传输到办公室的分析和物流规划工具以及卡车和仓库的移动设备上。 Enevo 解决方案随后被部署在 HFTH 的整个 420 收集站点。通过 Enevo 的基于 Web 的应用程序提供的强大数据报告和分析可以实现更好的预测,并且系统的动态功能可以根据实际需要更改集合和路线。
收集的数据
Asset Location, Asset Status Tracking, Fill Levels Of Containers, Operation Performance, Routes
运营影响
数量效益
相关案例.
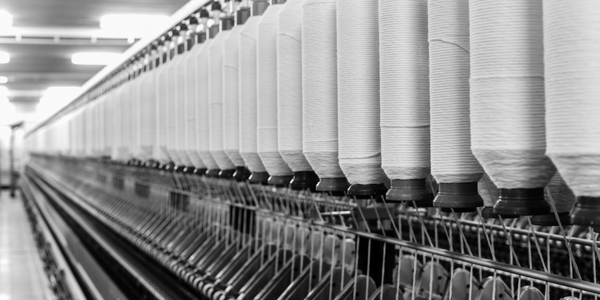
Case Study
IoT Applications and Upgrades in Textile Plant
At any given time, the textile company’s manufacturing facility has up to 2,000 textile carts in use. These carts are pushed from room to room, carrying materials or semi-finished products. Previously, a paper with a hand-written description was attached to each cart. This traditional method of processing made product tracking extremely difficult. Additionally, making sure that every cart of materials or semi-finished products went to its correct processing work station was also a problem. Therefore, the company desired an intelligent solution for tracking assets at their factories. They also wanted a solution that would help them collect process data so they could improve their manufacturing efficiency.
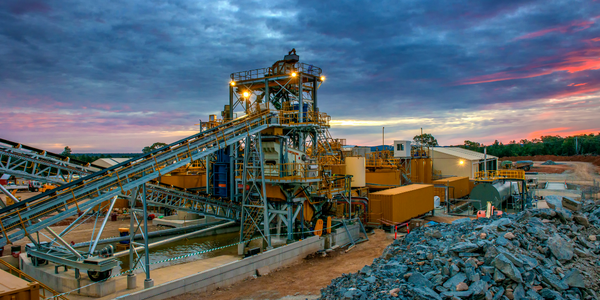
Case Study
Goldcorp: Internet of Things Enables the Mine of the Future
Goldcorp is committed to responsible mining practices and maintaining maximum safety for its workers. At the same time, the firm is constantly exploring ways to improve the efficiency of its operations, extend the life of its assets, and control costs. Goldcorp needed technology that can maximize production efficiency by tracking all mining operations, keep employees safe with remote operations and monitoring of hazardous work areas and control production costs through better asset and site management.
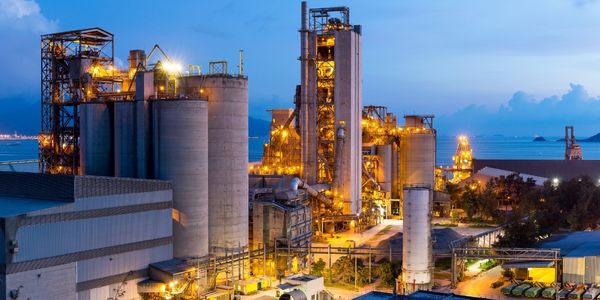
Case Study
System 800xA at Indian Cement Plants
Chettinad Cement recognized that further efficiencies could be achieved in its cement manufacturing process. It looked to investing in comprehensive operational and control technologies to manage and derive productivity and energy efficiency gains from the assets on Line 2, their second plant in India.
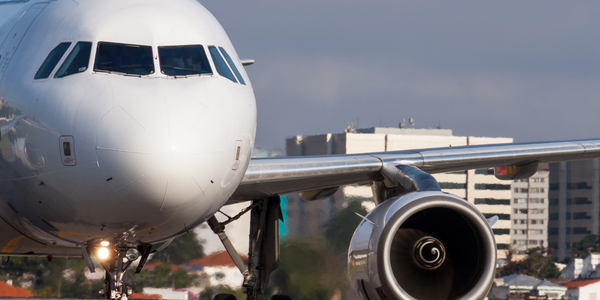
Case Study
Airbus Soars with Wearable Technology
Building an Airbus aircraft involves complex manufacturing processes consisting of thousands of moving parts. Speed and accuracy are critical to business and competitive advantage. Improvements in both would have high impact on Airbus’ bottom line. Airbus wanted to help operators reduce the complexity of assembling cabin seats and decrease the time required to complete this task.