下载PDF
Industry 4.0 and Cognitive Manufacturing
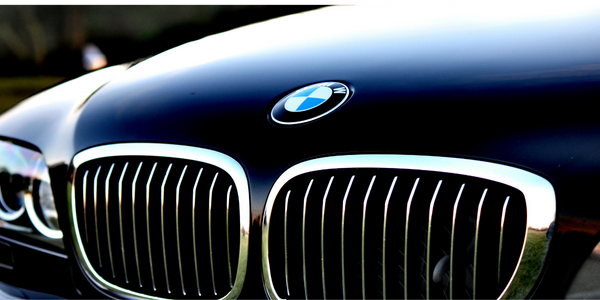
技术
- 分析与建模 - 机器学习
适用行业
- 汽车
适用功能
- 离散制造
- 质量保证
用例
- 计算机视觉
- 机器状态监测
服务
- 系统集成
挑战
制造商正面临与复杂的目视检查活动相关的风险挑战。每个制造商都需要许多人工检查员、操作员和工程师。他们承担着旨在识别数百个缺陷的重复性任务的全部工作量。这导致了主要的工厂劳动力成本、检查准确性和一致性问题、员工培训需求以及危险区域检查的潜在健康问题。
客户
宝马
库卡
关于客户
宝马——总部位于豪华汽车和摩托车的跨国企业制造商。
KUKA - 工业机器人和工厂自动化系统制造商。
解决方案
视觉检测系统基于机器学习算法,并利用多种视觉检测模式,如杂质/高对比度区域、几何检测和验证、异常纹理和区域检测以及颜色/亮度特征提取和验证来确定质量缺陷。 (该系统可以检测的示例包括制动钳缺陷、车身车间和油漆车间缺陷或损坏、零件变形、备件碰撞和汽车仪表板划痕。)
IBM 解决方案套件的视觉检测功能集成在设备线和机器人技术中。在本次展示中,IBM 正在使用 Watson Visual Recognition Service 检查新 BMW 5 系的多个门把手是否存在制造缺陷。
运营影响
相关案例.
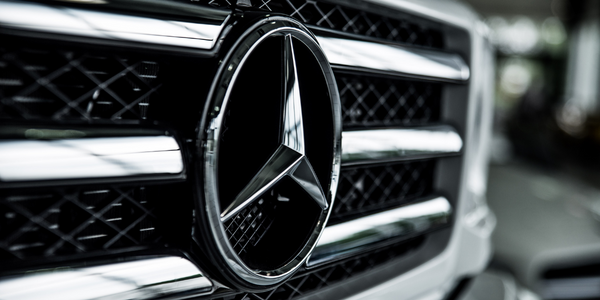
Case Study
Integral Plant Maintenance
Mercedes-Benz and his partner GAZ chose Siemens to be its maintenance partner at a new engine plant in Yaroslavl, Russia. The new plant offers a capacity to manufacture diesel engines for the Russian market, for locally produced Sprinter Classic. In addition to engines for the local market, the Yaroslavl plant will also produce spare parts. Mercedes-Benz Russia and his partner needed a service partner in order to ensure the operation of these lines in a maintenance partnership arrangement. The challenges included coordinating the entire maintenance management operation, in particular inspections, corrective and predictive maintenance activities, and the optimizing spare parts management. Siemens developed a customized maintenance solution that includes all electronic and mechanical maintenance activities (Integral Plant Maintenance).
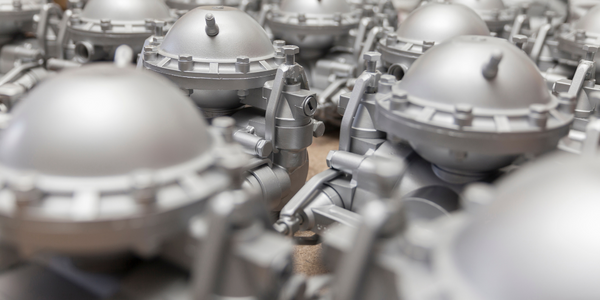
Case Study
Monitoring of Pressure Pumps in Automotive Industry
A large German/American producer of auto parts uses high-pressure pumps to deburr machined parts as a part of its production and quality check process. They decided to monitor these pumps to make sure they work properly and that they can see any indications leading to a potential failure before it affects their process.