下载PDF
Introduction of AI to Quality Inspection of Consumable Raw Material
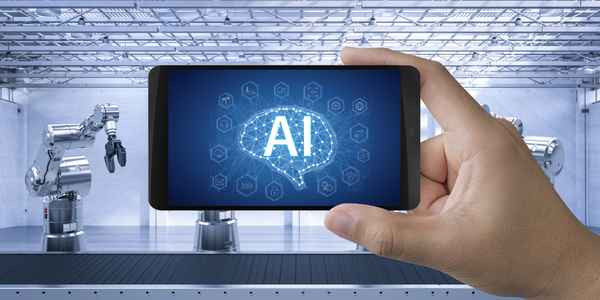
技术
- 分析与建模 - 计算机视觉软件
适用行业
- 汽车
适用功能
- 离散制造
用例
- 物体检测
服务
- 软件设计与工程服务
挑战
过去,检查人员需要目视检测很少混入流下生产线的原材料(植物)中的微小异物。
挑战是:
1. 检测人员肉眼难以检测- 检测人员需要目视检查小至 1mm 的异物,因此很难检测到。
2. 现有的检测设备无法解决问题——除了异物是微观的,原材料和异物都有多种类型和颜色,形状不定,因此基于规则的图像检测系统可以不处理它们。
3. 每家工厂和生产线的不同条件- 客户有多个工厂和生产线,每个工厂和生产线的异物类型不同,输送速度不同,检验员技能不同。
解决方案
为了解决上述问题,公司通过引入安装在生产线上的固定摄像头和AI算法来判断产品的好坏,实现了高质量的无人化检测。
运营影响
相关案例.
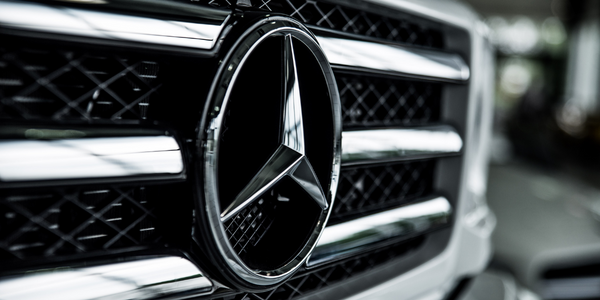
Case Study
Integral Plant Maintenance
Mercedes-Benz and his partner GAZ chose Siemens to be its maintenance partner at a new engine plant in Yaroslavl, Russia. The new plant offers a capacity to manufacture diesel engines for the Russian market, for locally produced Sprinter Classic. In addition to engines for the local market, the Yaroslavl plant will also produce spare parts. Mercedes-Benz Russia and his partner needed a service partner in order to ensure the operation of these lines in a maintenance partnership arrangement. The challenges included coordinating the entire maintenance management operation, in particular inspections, corrective and predictive maintenance activities, and the optimizing spare parts management. Siemens developed a customized maintenance solution that includes all electronic and mechanical maintenance activities (Integral Plant Maintenance).
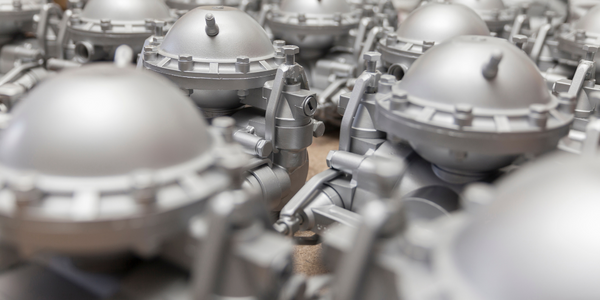
Case Study
Monitoring of Pressure Pumps in Automotive Industry
A large German/American producer of auto parts uses high-pressure pumps to deburr machined parts as a part of its production and quality check process. They decided to monitor these pumps to make sure they work properly and that they can see any indications leading to a potential failure before it affects their process.