下载PDF
OGIHARA Drives Customer Issue Tracking and CAPA Compliance with Enterprise PLM
技术
- 应用基础设施与中间件 - 数据交换与集成
- 应用基础设施与中间件 - 数据可视化
- 功能应用 - 产品生命周期管理系统 (PLM)
适用行业
- 汽车
适用功能
- 商业运营
- 质量保证
用例
- 预测性维护
- 过程控制与优化
- 监管合规监控
- 远程资产管理
服务
- 软件设计与工程服务
- 系统集成
挑战
Management’s goal was to maintain Ogihara’s competitive advantage, and at the same time, enable compliance to the ISO/TS16949 quality systems standard. Quality systems standards compel companies to gain control over strategic corporate quality processes, including Corrective Action / Preventive Action (CAPA), Supplier Corrective Action Requests (SCAR), customer issue management, nonconformance management, defect tracking, document management & control, and product realization or Advanced Product Quality Planning (APQP) during development ─ all core processes that support corporate-wide quality and customer satisfaction. As business grew at Ogihara, management recognized the need to unify the existing combination of systems that support these critical processes. Doing so would ensure streamlined product quality improvement and achieve more effective compliance processes to support future business growth. The Quality group and IT organization at Ogihara worked together to find a solution that would unify the company’s quality management and compliance processes without incurring significant costs. Given the evolving nature of compliance requirements and customer demands, IT also recognized the need for a flexible solution that would easily extend to new processes and scale to support an enterprise wide deployment. Finally, Ogihara employees, supplier partners, and customers needed to be able to participate in an increasing number of automated business processes for better collaboration and faster issue resolution.
关于客户
Ogihara America Corporation is a leading tier 1 supplier of vehicle body parts. With headquarters in Michigan, the company produces high-quality door, fender, hood, and roof panels for Mercedes-Benz, Cadillac, Lincoln, and other major brands. Despite the intense industry competition, Ogihara has thrived and grown the business. The company’s success with global OEM customers is due to its reputation as a recognized leader as a high-quality supplier. As Ogihara continues to grow, it maintains a sharp focus on its commitment to excellence and craftsmanship as well superior customer responsiveness.
解决方案
To meet these challenges, Ogihara turned to the Aras Innovator® solution suite for enterprise quality management and compliance to address: CAPA issue resolution with closed-loop accountability, customer issue collection, tracking, and response, defect tracking & nonconforming material management, failure mode & effects analysis for risk management, APQP with Part Submission Warrants for PPAP, phase-gate product program management with dashboard roll-ups for executive visibility, and ISO Document and file control with online change management workflows. Ogihara is implementing a five phase 8D CAPA process enterprise-wide using the Aras Innovator solution for quality systems. Aras enables Web submission of issues initiating an online workflow with specific actions depending on whether the issue is customer, supplier or internally-oriented. The CAPA process in Aras provides a single view of the process including the team assigned, problem scope & description and any containment actions taken. Then, root cause analysis is performed and recorded with file attachments including Office documents such as Word, Excel, Visio, and Power Point, as well as, data files, drawings, and PDFs. Finally, the corrective action and preventive actions are documented, implemented, and verified for closed loop resolution. The Aras system captures and manages the CAPA process and related information including: Issue Identification & Team, Problem Description, Containment, Root Cause Analysis, Corrective Action, Preventive Action, Verification of Effectiveness, and Team Recognition.
运营影响
数量效益
相关案例.
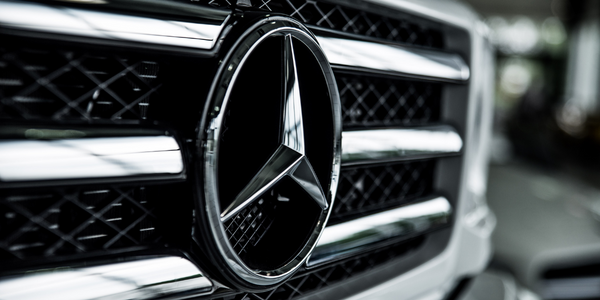
Case Study
Integral Plant Maintenance
Mercedes-Benz and his partner GAZ chose Siemens to be its maintenance partner at a new engine plant in Yaroslavl, Russia. The new plant offers a capacity to manufacture diesel engines for the Russian market, for locally produced Sprinter Classic. In addition to engines for the local market, the Yaroslavl plant will also produce spare parts. Mercedes-Benz Russia and his partner needed a service partner in order to ensure the operation of these lines in a maintenance partnership arrangement. The challenges included coordinating the entire maintenance management operation, in particular inspections, corrective and predictive maintenance activities, and the optimizing spare parts management. Siemens developed a customized maintenance solution that includes all electronic and mechanical maintenance activities (Integral Plant Maintenance).
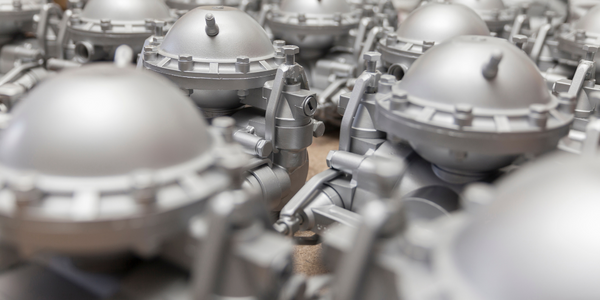
Case Study
Monitoring of Pressure Pumps in Automotive Industry
A large German/American producer of auto parts uses high-pressure pumps to deburr machined parts as a part of its production and quality check process. They decided to monitor these pumps to make sure they work properly and that they can see any indications leading to a potential failure before it affects their process.