下载PDF
Optimization of Plastic Parts for Lighter Vehicles: A Case Study of Kanto Auto Works
技术
- 机器人 - 自动导引车 (AGV)
- 传感器 - 电表
适用行业
- 汽车
- 金属
适用功能
- 产品研发
用例
- 连续排放监测系统
- 车辆性能监测
服务
- 测试与认证
挑战
为了减少二氧化碳排放并为防止全球变暖做出贡献,汽车工业一直致力于改善车身结构和发动机效率。这项努力的一个重要部分是努力减轻车身重量,从而提高燃油效率。虽然钢和铝等金属占汽车重量的大部分,但用更轻的塑料取代其中一些材料的趋势日益明显。然而,目前约占汽车重量 9% 的塑料也面临着自身的挑战。它比金属轻得多,可以模制成复杂的形状,但在外力或高温下也容易变形。丰田集团的核心成员关东汽车工厂面临着如何使塑料部件变得更轻,同时确保其保持足够的刚性和耐热性的挑战。
关于客户
关东汽车制作所(后来的丰田汽车东日本株式会社)是丰田集团的核心成员。该公司负责丰田汽车车身的开发和生产。该公司的有机材料工程部门评估和开发用于车身的塑料部件。在仪表板等大型塑料部件的开发初期,该部门使用计算机辅助工程(CAE)验证刚性和耐热性。该公司对减轻车辆重量和提高燃油效率的承诺是全球减少二氧化碳排放和应对全球变暖努力的一部分。
解决方案
为了应对这一挑战,Kanto Auto Works 开始使用 Altair 的结构优化工具 OptiStruct。该工具使公司能够可视化需要加固的区域。 OptiStruct 结合了多种优化功能的选择,可在设计过程的任何阶段使用仅通过经验无法获得的信息创建创新的新形状。它通过确定最佳材料、确定需要和不需要加固的位置、自动压边或压花、优化有限元建模以及确定最佳板材厚度和横截面形状,能够创建更轻的零件并减少生产过程中的步骤。托梁结构。使用 OptiStruct 进行拓扑优化计算,以可视化需要加固的区域,以防止外力引起的变形。对于耐热性,根据塑料试验板的试验结果进行计算,以确定引起板变形所需的载荷。
运营影响
数量效益
相关案例.
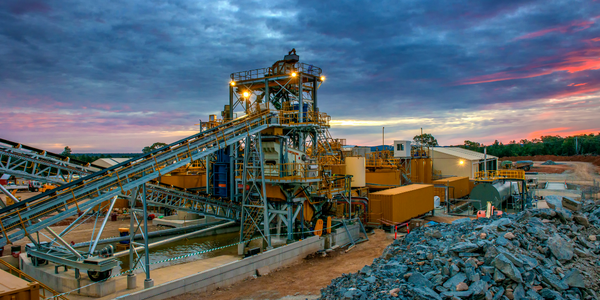
Case Study
Goldcorp: Internet of Things Enables the Mine of the Future
Goldcorp is committed to responsible mining practices and maintaining maximum safety for its workers. At the same time, the firm is constantly exploring ways to improve the efficiency of its operations, extend the life of its assets, and control costs. Goldcorp needed technology that can maximize production efficiency by tracking all mining operations, keep employees safe with remote operations and monitoring of hazardous work areas and control production costs through better asset and site management.
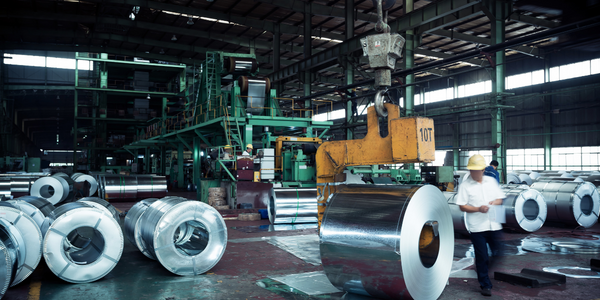
Case Study
KSP Steel Decentralized Control Room
While on-site in Pavlodar, Kazakhstan, the DAQRI team of Business Development and Solutions Architecture personnel worked closely with KSP Steel’s production leadership to understand the steel production process, operational challenges, and worker pain points.
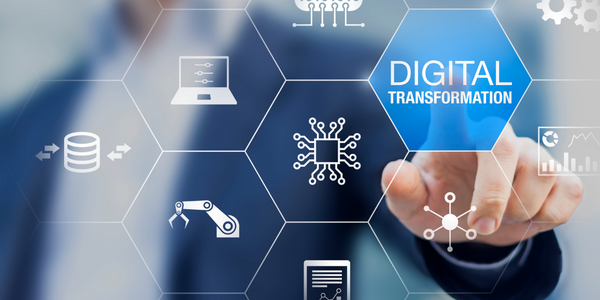
Case Study
Bluescope Steel on Path to Digitally Transform Operations and IT
Increasing competition and fluctuations in the construction market prompted BlueScope Steel to look toward digital transformation of its four businesses, including modern core applications and IT infrastructure. BlueScope needed to modernize its infrastructure and adopt new technologies to improve operations and supply chain efficiency while maintaining and updating an aging application portfolio.
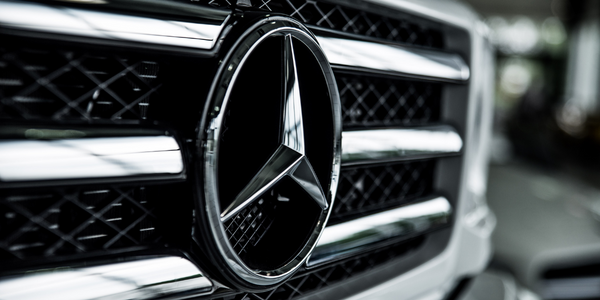
Case Study
Integral Plant Maintenance
Mercedes-Benz and his partner GAZ chose Siemens to be its maintenance partner at a new engine plant in Yaroslavl, Russia. The new plant offers a capacity to manufacture diesel engines for the Russian market, for locally produced Sprinter Classic. In addition to engines for the local market, the Yaroslavl plant will also produce spare parts. Mercedes-Benz Russia and his partner needed a service partner in order to ensure the operation of these lines in a maintenance partnership arrangement. The challenges included coordinating the entire maintenance management operation, in particular inspections, corrective and predictive maintenance activities, and the optimizing spare parts management. Siemens developed a customized maintenance solution that includes all electronic and mechanical maintenance activities (Integral Plant Maintenance).
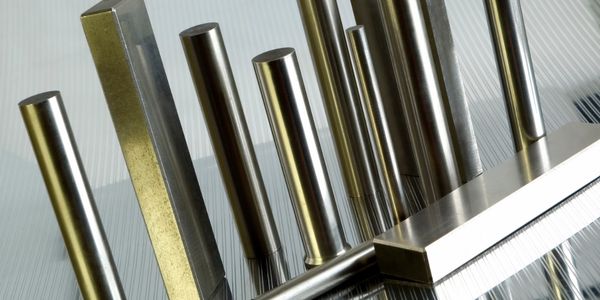
Case Study
RobotStudio Case Study: Benteler Automobiltechnik
Benteler has a small pipe business area for which they produce fuel lines and coolant lines made of aluminum for Porsche and other car manufacturers. One of the problems in production was that when Benteler added new products, production had too much downtime.