下载PDF
Playing it cool
技术
- 平台即服务 (PaaS) - 连接平台
- 应用基础设施与中间件 - API 集成与管理
适用行业
- 食品与饮料
- 医疗保健和医院
- 农业
适用功能
- 维护
- 质量保证
用例
- 预测性维护
- 能源管理系统
- 远程资产管理
服务
- 系统集成
- 软件设计与工程服务
挑战
Oxford Energy Solutions Inc., a Canadian company, has been designing and building refrigeration equipment for various sectors since 2006. The refrigeration sector is relatively conservative, with many facilities still running systems that were installed 50 years ago. Maintenance is usually done reactively by replacing broken parts like valves and compressors without addressing bigger issues. Oxford Energy wanted to change the way refrigeration systems are built and maintained in line with its ethos of energy conservation and sustainability. The company was looking for a flexible, holistic platform that would enable it to bring its vision of control and integration to the market.
关于客户
Oxford Energy Solutions Inc. is a Canadian company that has been designing and building refrigeration equipment for agricultural, food processing, industrial, and healthcare customers in the North American market since 2006. The company is committed to energy conservation and sustainability and aims to revolutionize the way refrigeration systems are built and maintained. Oxford Energy is focused on modernizing 50-year-old refrigeration systems to improve visibility of operating thresholds and increase their flexibility, reliability, and functionality.
解决方案
Oxford Energy decided on a full suite of EcoStruxure Machine solutions to provide its customers with more efficient refrigeration systems. At the heart of Oxford Energy’s platform is the Modicon M172 logic controller which offers a wide choice of connectivity options to support integration with a variety of building management systems. This ready-to-connect controller requires no on-site programming and enables control of every device in the system. Another important element is EcoStruxure Secure Connect Advisor, which adds a security layer and helps protect the system. It also comes with an intuitive e-mail notification system that helps pinpoint where issues have occurred and speeds up maintenance which can be done remotely. An IPC/HMI controller brings all this information into a pre-defined set of screens. Combined with the dashboard and server system where Oxford Energy is applying advanced analytics and machine learning, it results in a fully integrated solution.
运营影响
数量效益
相关案例.
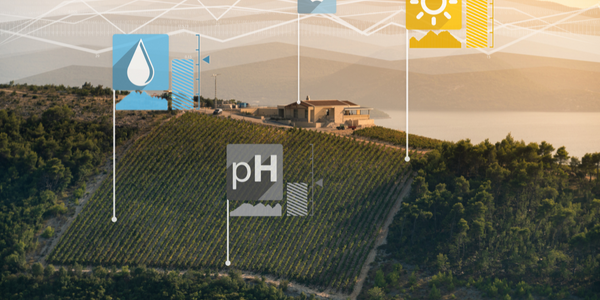
Case Study
Intelligent Farming with ThingWorx Analytics
Z Farms was facing three challenges: costly irrigation systems with water as a limited resource, narrow optimal ranges of soil moisture for growth with difficult maintenance and farm operators could not simply turn on irrigation systems like a faucet.
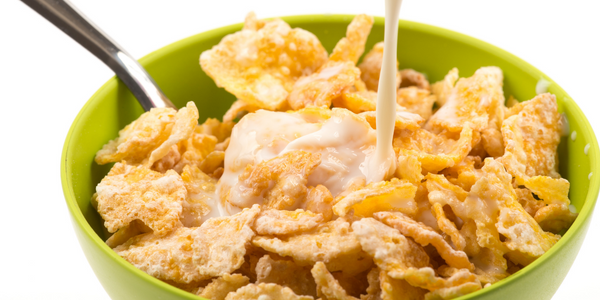
Case Study
The Kellogg Company
Kellogg keeps a close eye on its trade spend, analyzing large volumes of data and running complex simulations to predict which promotional activities will be the most effective. Kellogg needed to decrease the trade spend but its traditional relational database on premises could not keep up with the pace of demand.
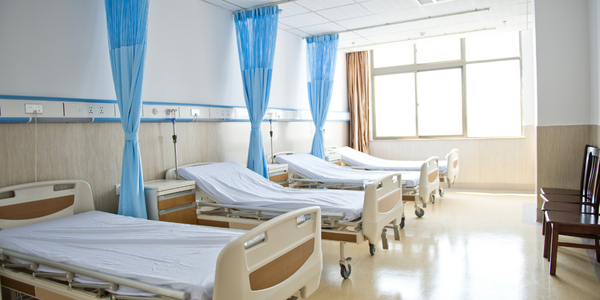
Case Study
Hospital Inventory Management
The hospital supply chain team is responsible for ensuring that the right medical supplies are readily available to clinicians when and where needed, and to do so in the most efficient manner possible. However, many of the systems and processes in use at the cancer center for supply chain management were not best suited to support these goals. Barcoding technology, a commonly used method for inventory management of medical supplies, is labor intensive, time consuming, does not provide real-time visibility into inventory levels and can be prone to error. Consequently, the lack of accurate and real-time visibility into inventory levels across multiple supply rooms in multiple hospital facilities creates additional inefficiency in the system causing over-ordering, hoarding, and wasted supplies. Other sources of waste and cost were also identified as candidates for improvement. Existing systems and processes did not provide adequate security for high-cost inventory within the hospital, which was another driver of cost. A lack of visibility into expiration dates for supplies resulted in supplies being wasted due to past expiry dates. Storage of supplies was also a key consideration given the location of the cancer center’s facilities in a dense urban setting, where space is always at a premium. In order to address the challenges outlined above, the hospital sought a solution that would provide real-time inventory information with high levels of accuracy, reduce the level of manual effort required and enable data driven decision making to ensure that the right supplies were readily available to clinicians in the right location at the right time.
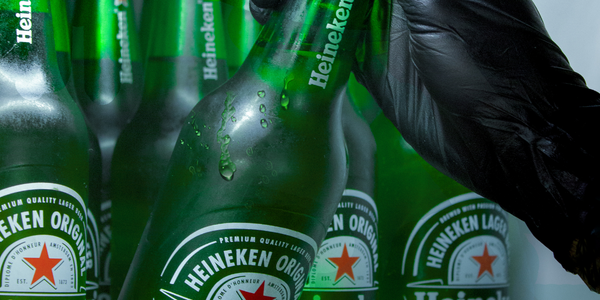
Case Study
HEINEKEN Uses the Cloud to Reach 10.5 Million Consumers
For 2012 campaign, the Bond promotion, it planned to launch the campaign at the same time everywhere on the planet. That created unprecedented challenges for HEINEKEN—nowhere more so than in its technology operation. The primary digital content for the campaign was a 100-megabyte movie that had to play flawlessly for millions of viewers worldwide. After all, Bond never fails. No one was going to tolerate a technology failure that might bruise his brand.Previously, HEINEKEN had supported digital media at its outsourced datacenter. But that datacenter lacked the computing resources HEINEKEN needed, and building them—especially to support peak traffic that would total millions of simultaneous hits—would have been both time-consuming and expensive. Nor would it have provided the geographic reach that HEINEKEN needed to minimize latency worldwide.