下载PDF
Premier Custom-Built Embraces Digital Transformation While Preserving Old-School Craftsmanship
技术
- 平台即服务 (PaaS) - 应用开发平台
- 应用基础设施与中间件 - API 集成与管理
- 分析与建模 - 实时分析
适用功能
- 产品研发
- 质量保证
- 商业运营
用例
- 数字孪生
- 预测性维护
- 远程协作
服务
- 云规划/设计/实施服务
- 软件设计与工程服务
- 系统集成
挑战
Pennsylvania furniture manufacturer Premier Custom-Built makes custom cabinetry for luxury homes and yachts, designing every job from scratch. The engineering team was looking to create a paperless manufacturing floor, aiming to migrate the product specs currently in 3-ring binders to 3D CAD models. Premier was also seeking a way to automate repetitive design tasks to speed up time to market.
关于客户
Premier Custom-Built is a luxury furniture manufacturer based in Lancaster County, Pennsylvania, also known as Pennsylvania Dutch Country or Amish Country. The company specializes in custom cabinetry for luxury homes and yachts, with a strong emphasis on craftsmanship. Founded in 1991 by Marlin Horst, the company is now led by his son, Sheldon Horst. Premier Custom-Built has a rich history of using technology to enhance its operations, as evidenced by their makeshift museum of obsolete technology. The company is deeply rooted in the region's centuries-old tradition of woodworking, originally fostered by Swiss-German immigrants. Premier Custom-Built aims to preserve this craftsmanship while integrating modern technology to operate more effectively.
解决方案
At the center of Premier Custom-Built's digital transformation strategy is cloud-native Onshape, PTC’s product development platform that unites advanced CAD tools with built-in data management, real-time collaboration, and business analytics. Onshape has become a central part of Premier's IT department, bringing engineering and IT together to design and develop products collaboratively. The use of FeatureScript, Onshape’s open-source programming language, has allowed Premier to create more than 50 custom cabinet features, automating repetitive tasks and giving engineers more time to focus on innovation. Onshape Configurations also enable Premier to quickly modify cabinet designs based on customer preferences, making the design process more efficient.
运营影响
数量效益
相关案例.
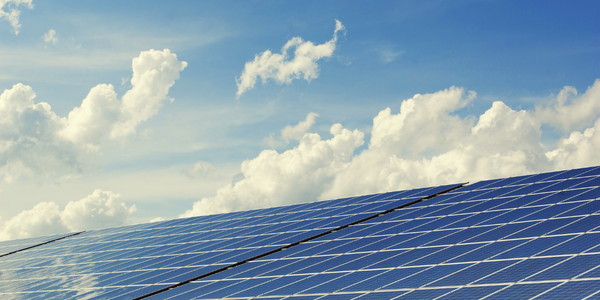
Case Study
Remote Monitoring & Predictive Maintenance App for a Solar Energy System
The maintenance & tracking of various modules was an overhead for the customer due to the huge labor costs involved. Being an advanced solar solutions provider, they wanted to ensure early detection of issues and provide the best-in-class customer experience. Hence they wanted to automate the whole process.
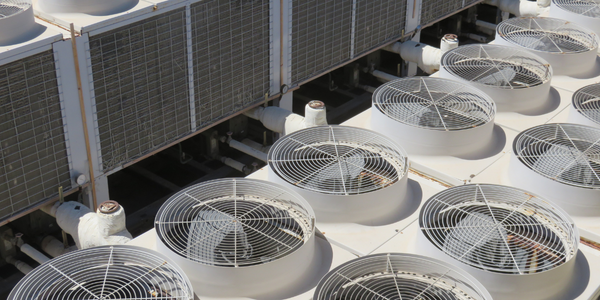
Case Study
Predictive Maintenance for Industrial Chillers
For global leaders in the industrial chiller manufacturing, reliability of the entire production process is of the utmost importance. Chillers are refrigeration systems that produce ice water to provide cooling for a process or industrial application. One of those leaders sought a way to respond to asset performance issues, even before they occur. The intelligence to guarantee maximum reliability of cooling devices is embedded (pre-alarming). A pre-alarming phase means that the cooling device still works, but symptoms may appear, telling manufacturers that a failure is likely to occur in the near future. Chillers who are not internet connected at that moment, provide little insight in this pre-alarming phase.
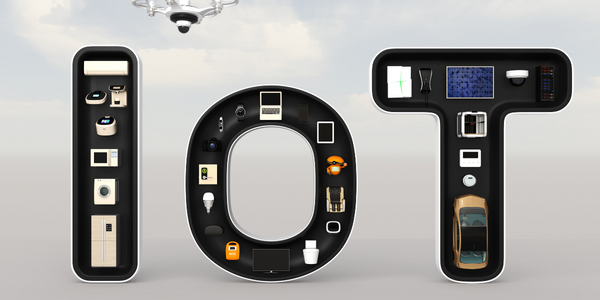
Case Study
Premium Appliance Producer Innovates with Internet of Everything
Sub-Zero faced the largest product launch in the company’s history:It wanted to launch 60 new products as scheduled while simultaneously opening a new “greenfield” production facility, yet still adhering to stringent quality requirements and manage issues from new supply-chain partners. A the same time, it wanted to increase staff productivity time and collaboration while reducing travel and costs.
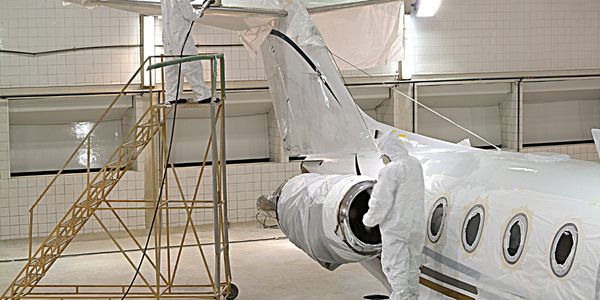
Case Study
Aircraft Predictive Maintenance and Workflow Optimization
First, aircraft manufacturer have trouble monitoring the health of aircraft systems with health prognostics and deliver predictive maintenance insights. Second, aircraft manufacturer wants a solution that can provide an in-context advisory and align job assignments to match technician experience and expertise.
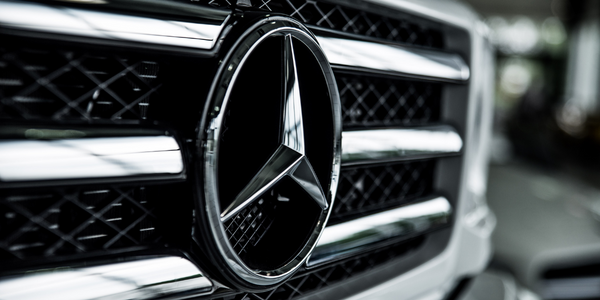
Case Study
Integral Plant Maintenance
Mercedes-Benz and his partner GAZ chose Siemens to be its maintenance partner at a new engine plant in Yaroslavl, Russia. The new plant offers a capacity to manufacture diesel engines for the Russian market, for locally produced Sprinter Classic. In addition to engines for the local market, the Yaroslavl plant will also produce spare parts. Mercedes-Benz Russia and his partner needed a service partner in order to ensure the operation of these lines in a maintenance partnership arrangement. The challenges included coordinating the entire maintenance management operation, in particular inspections, corrective and predictive maintenance activities, and the optimizing spare parts management. Siemens developed a customized maintenance solution that includes all electronic and mechanical maintenance activities (Integral Plant Maintenance).

Case Study
Asset Management and Predictive Maintenance
The customer prides itself on excellent engineering and customer centric philosophy, allowing its customer’s minds to be at ease and not worry about machine failure. They can easily deliver the excellent maintenance services to their customers, but there are some processes that can be automated to deliver less downtime for the customer and more efficient maintenance schedules.