下载PDF
Qlikview Gives Jardine Lloyd Thompson A Global View of Its Risk Business
技术
- 应用基础设施与中间件 - 数据可视化
- 分析与建模 - 大数据分析
用例
- 预测性维护
服务
- 数据科学服务
- 系统集成
挑战
Jardine Lloyd Thompson (JLT) is an international group of risk specialists and employee benefits consultants. The firm wanted to give its global executives access to real-time information on mobile devices to help them deliver great customer service. However, JLT needed to replace its existing business intelligence (BI) infrastructure and move away from its labour-intensive approach to business discovery. The company had a large data warehouse, but all of the analytics were pretty much after the event. Internal analysis at JLT took time and there was uncertainty about the accuracy of the findings. It led people to question what they were seeing. JLT wanted to adopt a more intuitive, real-time, graphical solution that better suited its global dynamic workforce and commitment to business transformation.
关于客户
Jardine Lloyd Thompson (JLT) is an international group of risk specialists and employee benefits consultants, and one of the largest companies of its type worldwide. The group—with 2011 revenues of £818 million (US$1.3 billion)—was formed in 1997 in the United Kingdom (UK) when Jardine Insurance Brokers merged with Lloyd Thompson Group. Listed on the London Stock Exchange, the group employs more than 7,000 people in around 135 countries. JLT prides itself on its client-first, knowledge-led global business strategy. The firm wanted to give its global executives access to real-time information on mobile devices— helping them deliver great customer service.
解决方案
JLT selected the QlikView Business Discovery platform to replace its many legacy reporting models and put self-service business discovery into the hands of its employees. Data visualisation through QlikView led to a major change of business culture at JLT. Users could make selections, click into them, and immediately see relationships within. The biggest single change since deploying QlikView is better decision making through data visualisation. With QlikView accessible via desktops and a variety of mobile devices, users quickly see trends, identify opportunities that will add value, and ask simple actionable questions. JLT is using QlikView across a variety of business lines, including customer analytics and operational performance. It stems from a belief that client knowledge is the key to success in a competitive industry.
运营影响
数量效益
相关案例.
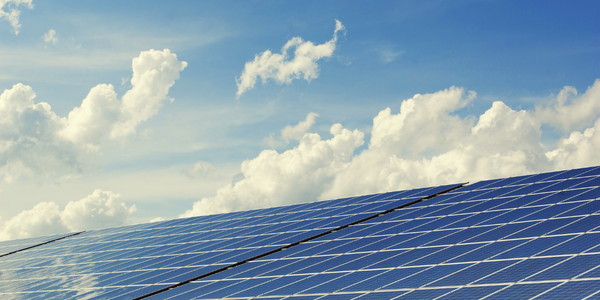
Case Study
Remote Monitoring & Predictive Maintenance App for a Solar Energy System
The maintenance & tracking of various modules was an overhead for the customer due to the huge labor costs involved. Being an advanced solar solutions provider, they wanted to ensure early detection of issues and provide the best-in-class customer experience. Hence they wanted to automate the whole process.
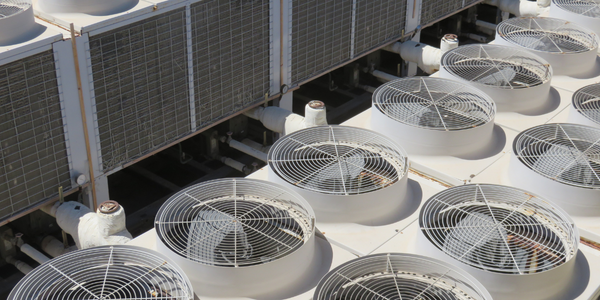
Case Study
Predictive Maintenance for Industrial Chillers
For global leaders in the industrial chiller manufacturing, reliability of the entire production process is of the utmost importance. Chillers are refrigeration systems that produce ice water to provide cooling for a process or industrial application. One of those leaders sought a way to respond to asset performance issues, even before they occur. The intelligence to guarantee maximum reliability of cooling devices is embedded (pre-alarming). A pre-alarming phase means that the cooling device still works, but symptoms may appear, telling manufacturers that a failure is likely to occur in the near future. Chillers who are not internet connected at that moment, provide little insight in this pre-alarming phase.
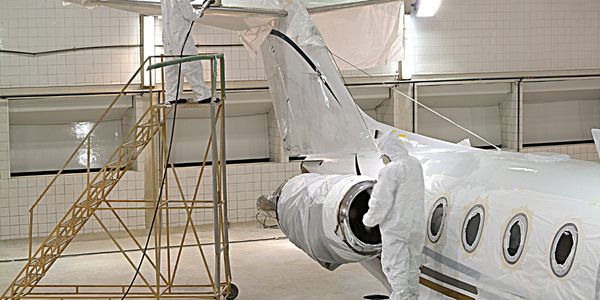
Case Study
Aircraft Predictive Maintenance and Workflow Optimization
First, aircraft manufacturer have trouble monitoring the health of aircraft systems with health prognostics and deliver predictive maintenance insights. Second, aircraft manufacturer wants a solution that can provide an in-context advisory and align job assignments to match technician experience and expertise.
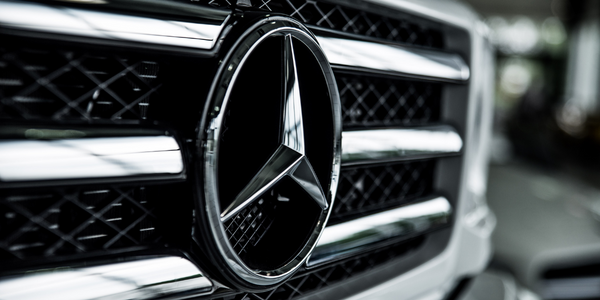
Case Study
Integral Plant Maintenance
Mercedes-Benz and his partner GAZ chose Siemens to be its maintenance partner at a new engine plant in Yaroslavl, Russia. The new plant offers a capacity to manufacture diesel engines for the Russian market, for locally produced Sprinter Classic. In addition to engines for the local market, the Yaroslavl plant will also produce spare parts. Mercedes-Benz Russia and his partner needed a service partner in order to ensure the operation of these lines in a maintenance partnership arrangement. The challenges included coordinating the entire maintenance management operation, in particular inspections, corrective and predictive maintenance activities, and the optimizing spare parts management. Siemens developed a customized maintenance solution that includes all electronic and mechanical maintenance activities (Integral Plant Maintenance).

Case Study
Asset Management and Predictive Maintenance
The customer prides itself on excellent engineering and customer centric philosophy, allowing its customer’s minds to be at ease and not worry about machine failure. They can easily deliver the excellent maintenance services to their customers, but there are some processes that can be automated to deliver less downtime for the customer and more efficient maintenance schedules.