下载PDF
Revving Up The Automotive Aftermarket Through Continuous Process Improvement
技术
- 分析与建模 - 实时分析
- 应用基础设施与中间件 - 数据交换与集成
适用行业
- 汽车
适用功能
- 离散制造
- 销售与市场营销
用例
- 预测性维护
- 供应链可见性(SCV)
服务
- 数据科学服务
- 系统集成
挑战
Bosch, a leading global supplier of technology and services, was facing challenges in managing complex data and legacy process management systems. The company was struggling to meet customer demands for lower prices and more detailed order tracking. Bosch's global scale, with over 450 subsidiaries and local companies operating in over 60 countries, made these demands seem insurmountable. The company was also dealing with data stored on independent systems, complex reporting requirements, increasing competition and thinner margins, and growing process administration delays. Bosch lacked a centralized platform for generating reports or a standard way to manage business processes, which was like operating with blinders on. The company needed more agility, better insights, and greater flexibility.
关于客户
The Bosch Group is a leading global supplier of technology and services. It employs 389,000 associates worldwide who conform to the company’s foundational ideals of innovative strength and social commitment. Bosch operates in four business sectors—Mobility Solutions, Industrial Technology, Consumer Goods, and Energy and Building Technology. In 2016, these sectors reached combined global revenues of over 73 billion euros. Bosch is a global organization with over 450 subsidiaries and local companies operating in over 60 countries. The company's products are “invented for life,” and customer care is its top priority.
解决方案
Bosch implemented Software AG’s Process Performance Manager to address its challenges. The solution automatically extracted relevant daily data and made it visible on a platform, enabling processes to be analyzed from numerous angles, including deep dives into individual process instances. The new system, which went live fully in 2017, cut order inquiry response times by five percent. This resulted in a spike in customer satisfaction, better retention rates, and improved churn in sales KPIs. The solution also automated the order inquiry process, cutting administrative work by three days per month. Bosch was so impressed by these early results that it quickly moved to implement additional Process Performance Manager capabilities. These capabilities, like benchmarking, process mining, and situational analysis dashboards, will greatly impact overall efficiency.
运营影响
数量效益
相关案例.
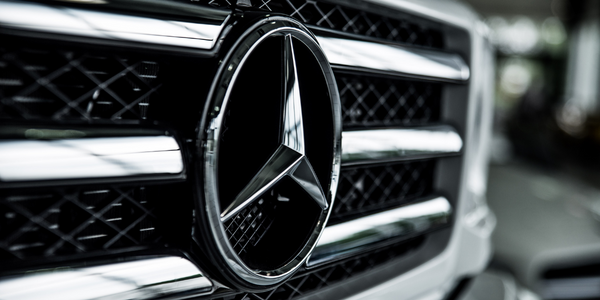
Case Study
Integral Plant Maintenance
Mercedes-Benz and his partner GAZ chose Siemens to be its maintenance partner at a new engine plant in Yaroslavl, Russia. The new plant offers a capacity to manufacture diesel engines for the Russian market, for locally produced Sprinter Classic. In addition to engines for the local market, the Yaroslavl plant will also produce spare parts. Mercedes-Benz Russia and his partner needed a service partner in order to ensure the operation of these lines in a maintenance partnership arrangement. The challenges included coordinating the entire maintenance management operation, in particular inspections, corrective and predictive maintenance activities, and the optimizing spare parts management. Siemens developed a customized maintenance solution that includes all electronic and mechanical maintenance activities (Integral Plant Maintenance).
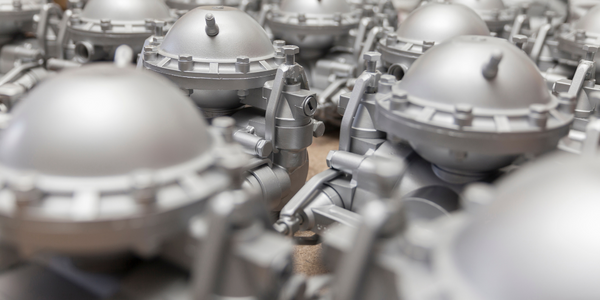
Case Study
Monitoring of Pressure Pumps in Automotive Industry
A large German/American producer of auto parts uses high-pressure pumps to deburr machined parts as a part of its production and quality check process. They decided to monitor these pumps to make sure they work properly and that they can see any indications leading to a potential failure before it affects their process.