下载PDF
Richard Childress Racing: A Drive to Grow and Help Others
技术
- 功能应用 - 远程监控系统
适用行业
- 汽车
适用功能
- 离散制造
- 产品研发
用例
- 自动化制造系统
- 预测性维护
服务
- 系统集成
挑战
Richard Childress Racing (RCR) faced the challenge of managing their manufacturing process efficiently to meet tight deadlines and adapt to product changes. Initially, they used JobBOSS for scheduling their machines to quickly finish parts and prototypes for testing before race day. However, as the complexity of their operations increased, they needed to schedule programming as well. They were also struggling with communication issues, especially regarding materials needed for building a racecar. The team had to complete a working chassis in less than a week, which required efficient and transparent information relay. The short turnaround time and the delay in getting material requirements to the materials planner were other challenges they faced.
关于客户
Richard Childress Racing (RCR) is an iconic organization in NASCAR. After owner Richard Childress retired from driving in 1981 and handed over the seat of the No. 3 Chevrolet to young driver Dale Earnhardt, Sr., Childress and Earnhardt went on to win six NASCAR Sprint Cup championships together. Behind every car and driver is a larger team that works day and night to not only make sure the vehicle is working, but to ensure it goes faster than any other car on the track. Over the past 15 years, numerous great drivers, parts, vehicles, and seasons have come and gone for RCR. But the passion to get out there and build the fastest cars remains. RCR has grown tremendously over the years, supporting 11 shops within the company and supplying parts for its alliance teams.
解决方案
RCR expanded the use of JobBOSS to schedule the programming side of the manufacturing process, automating a process that previously required extensive manual attention. This gave them a better understanding of the workload and allowed them to make better decisions within the required timeframe to get a part done. To address the issue of uncertainty regarding materials on hand, RCR used JobBOSS’ Materials Requirements Planning (MRP) module. They moved all the data regarding what alloys they had available in the shops into one centralized source. This cut down on verbal communication and gave everyone involved a clear view of what was going on with the car. The team also moved all the material and part data into JobBOSS’s MRP rather than on whiteboards or inventory sheets, enabling parts to be made and purchased more quickly and feasibly thanks to end-to-end inventory control.
运营影响
数量效益
相关案例.
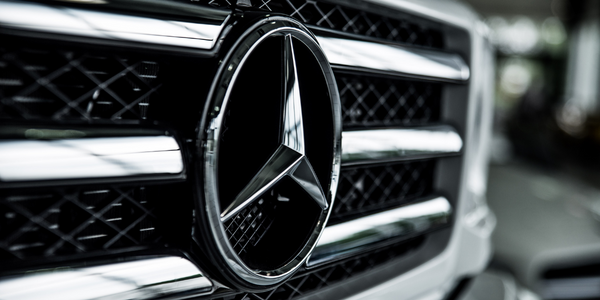
Case Study
Integral Plant Maintenance
Mercedes-Benz and his partner GAZ chose Siemens to be its maintenance partner at a new engine plant in Yaroslavl, Russia. The new plant offers a capacity to manufacture diesel engines for the Russian market, for locally produced Sprinter Classic. In addition to engines for the local market, the Yaroslavl plant will also produce spare parts. Mercedes-Benz Russia and his partner needed a service partner in order to ensure the operation of these lines in a maintenance partnership arrangement. The challenges included coordinating the entire maintenance management operation, in particular inspections, corrective and predictive maintenance activities, and the optimizing spare parts management. Siemens developed a customized maintenance solution that includes all electronic and mechanical maintenance activities (Integral Plant Maintenance).
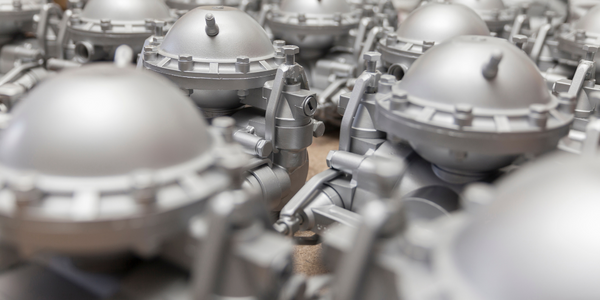
Case Study
Monitoring of Pressure Pumps in Automotive Industry
A large German/American producer of auto parts uses high-pressure pumps to deburr machined parts as a part of its production and quality check process. They decided to monitor these pumps to make sure they work properly and that they can see any indications leading to a potential failure before it affects their process.