下载PDF
Rubicon Project Automates Real Time Business Incident Detection with Anodot
技术
- 分析与建模 - 实时分析
- 分析与建模 - 预测分析
适用功能
- 商业运营
用例
- 实时定位系统 (RTLS)
- 预测性维护
服务
- 数据科学服务
挑战
Rubicon Project, one of the largest ad exchanges in the world, processes trillions of transactions each month in real-time auctions. The company receives more than 13 trillion bid requests per month, handled in its seven global data centers, housing more than 55,000 CPUs. However, the Tech Ops team could not monitor more complex aspects of business and trends, especially not in real time. For instance, Rubicon needed real-time insight if a large institutional buyer deviated from its normal transaction trend by any percentage in one of the global data centers at any hour of the day or night. Such deviations could have a devastating effect on the exchange if there was a delay in addressing it with the customer. Along the bid stream, there were many potential areas for communication or technical breakdown, which would prevent the bid from going into the auction, and negatively affect overall bid health.
关于客户
Rubicon Project is one of the largest ad exchanges in the world, using proprietary computing systems to automate the buying and selling of advertising. The company employs more than 700 people and provides real-time ad auction services for their partners in various industries. More than 90% of people browsing the internet will see an ad that goes through the Rubicon exchange. Each day, Rubicon’s systems process more than twice as many transactions as the Nasdaq stock exchange. The company receives more than 13 trillion bid requests per month, handled in its seven global data centers, housing more than 55,000 CPUs.
解决方案
Rubicon Project implemented Anodot to monitor all of their data in real time. The company was already using Graphite for its monitoring, so it simply pulled Graphite data into Anodot. They immediately benefitted from streamlining and automating the data analytics. Previous monitoring tools that Rubicon used required the company to manually set thresholds to generate alerts. Anodot takes the solution to the next level, by learning the normal behavior of Rubicon's data and determining seasonality for each metric, unlike other solutions which cannot account for seasonal trends. With the new real-time analysis from Anodot, Rubicon will notice if a specific DSP stops responding to bids over 15 minute increments. Rubicon uses the Anodot alerts and correlations to determine if they need to reach out to their partner to fix an issue.
运营影响
数量效益
相关案例.
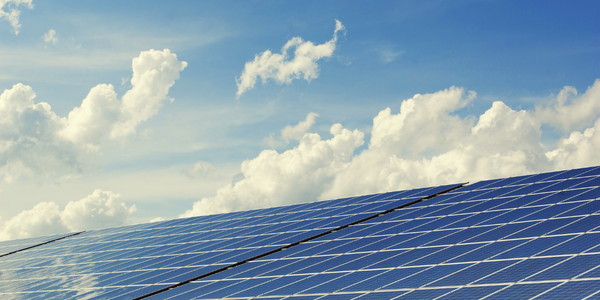
Case Study
Remote Monitoring & Predictive Maintenance App for a Solar Energy System
The maintenance & tracking of various modules was an overhead for the customer due to the huge labor costs involved. Being an advanced solar solutions provider, they wanted to ensure early detection of issues and provide the best-in-class customer experience. Hence they wanted to automate the whole process.
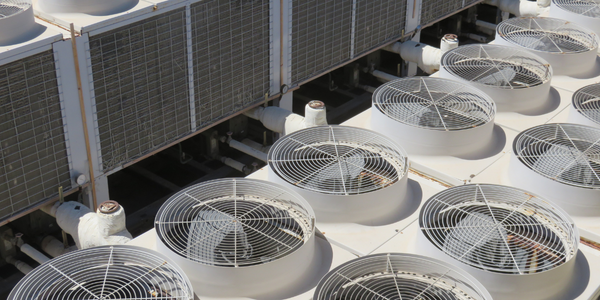
Case Study
Predictive Maintenance for Industrial Chillers
For global leaders in the industrial chiller manufacturing, reliability of the entire production process is of the utmost importance. Chillers are refrigeration systems that produce ice water to provide cooling for a process or industrial application. One of those leaders sought a way to respond to asset performance issues, even before they occur. The intelligence to guarantee maximum reliability of cooling devices is embedded (pre-alarming). A pre-alarming phase means that the cooling device still works, but symptoms may appear, telling manufacturers that a failure is likely to occur in the near future. Chillers who are not internet connected at that moment, provide little insight in this pre-alarming phase.
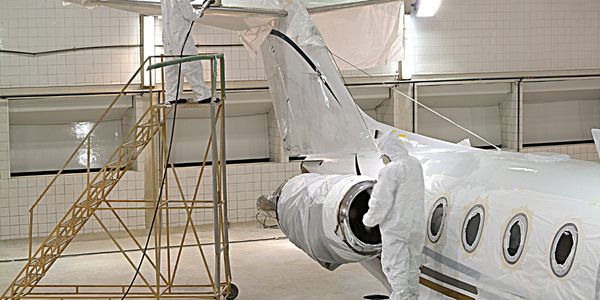
Case Study
Aircraft Predictive Maintenance and Workflow Optimization
First, aircraft manufacturer have trouble monitoring the health of aircraft systems with health prognostics and deliver predictive maintenance insights. Second, aircraft manufacturer wants a solution that can provide an in-context advisory and align job assignments to match technician experience and expertise.
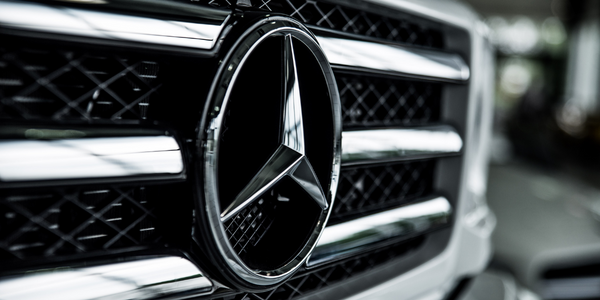
Case Study
Integral Plant Maintenance
Mercedes-Benz and his partner GAZ chose Siemens to be its maintenance partner at a new engine plant in Yaroslavl, Russia. The new plant offers a capacity to manufacture diesel engines for the Russian market, for locally produced Sprinter Classic. In addition to engines for the local market, the Yaroslavl plant will also produce spare parts. Mercedes-Benz Russia and his partner needed a service partner in order to ensure the operation of these lines in a maintenance partnership arrangement. The challenges included coordinating the entire maintenance management operation, in particular inspections, corrective and predictive maintenance activities, and the optimizing spare parts management. Siemens developed a customized maintenance solution that includes all electronic and mechanical maintenance activities (Integral Plant Maintenance).
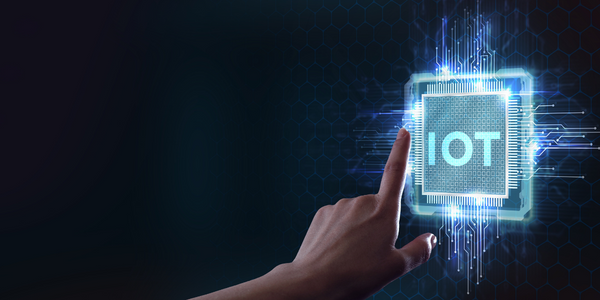
Case Study
Leading Tools Manufacturer Transforms Operations with IoT
Stanley Black & Decker required transparency of real-time overall equipment effectiveness and line productivity to reduce production line change over time.The goal was to to improve production to schedule, reduce actual labor costs and understanding the effects of shift changes and resource shifts from line to line.

Case Study
Asset Management and Predictive Maintenance
The customer prides itself on excellent engineering and customer centric philosophy, allowing its customer’s minds to be at ease and not worry about machine failure. They can easily deliver the excellent maintenance services to their customers, but there are some processes that can be automated to deliver less downtime for the customer and more efficient maintenance schedules.