下载PDF
Sandvik's Transition to Zero Trust Network with Zscaler Private Access
技术
- 基础设施即服务 (IaaS) - 公共云
- 网络与连接 - 网关
适用行业
- 矿业
- 国家安全与国防
用例
- 网络安全
- 篡改检测
服务
- 云规划/设计/实施服务
挑战
山特维克集团是一家全球高科技工程公司,其传统的虚拟专用网络 (VPN) 方法在连接和保护远程工作人员方面面临重大挑战。VPN 技术自推出以来一直没有太大发展,导致生产力和用户体验受到阻碍。该公司正在寻找一种能够消除连接障碍并减少攻击面的技术,以改善其安全状况。COVID-19 疫情进一步加剧了这一挑战,迫使公司迅速过渡到随时随地工作 (WFA) 模式。该公司需要快速、平稳地建立零信任网络访问,以实现这一转变。
关于客户
山特维克集团是一家全球高科技和工程公司,坚定致力于提高客户的生产力、盈利能力和可持续性。山特维克成立于 1862 年,在工业工具和模具、采矿和建筑设备以及先进不锈钢和特种合金领域拥有约 6,000 项有效专利。该公司在制造和机械加工、采矿和岩石、岩石加工以及材料技术领域处于世界领先地位。山特维克在 140 个国家的近 600 个工厂拥有 37,000 名员工,是工业工程行业的重要参与者。
解决方案
山特维克集团求助于他们之前合作过的 Zscaler 公司来实施零信任战略。他们使用 Zscaler Private Access (ZPA) 进行了价值证明,这是一种云驱动的解决方案,可以解决他们的 VPN 问题。 ZPA 已在 30 名用户中进行了测试,并于五天后在全球推出,使所有员工能够在疫情期间安全工作。 ZPA 解决方案为公共云和山特维克数据中心内运行的私有应用程序提供无缝、安全、无 VPN 的访问。通过将 ZPA 添加到其现有的 Zscaler Internet Access (ZIA) 部署中,山特维克建立了一个名为 Zscaler 零信任交换平台的整体 WFA 零信任安全环境。 ZPA 解决方案还确保网络和应用程序都不会暴露在互联网上,从而使未经授权的用户完全看不到山特维克的所有基础设施,同时仍向授权用户授予最低权限的访问权限。
运营影响
数量效益
相关案例.
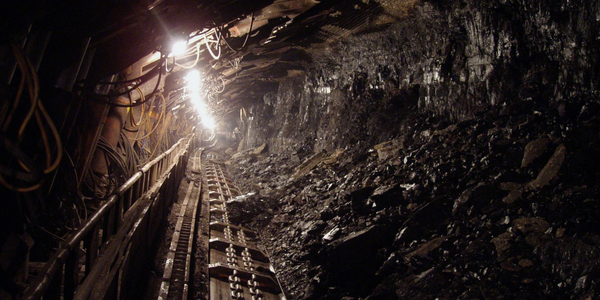
Case Study
Underground Mining Safety
The goal was to produce a safety system to monitor and support underground mining operations; existing systems were either too simple (i.e. phone line) or overly complex and expensive, inhibiting deployment, and providing little-to-no support in event of an accident. Given the dangerous nature of the mining work environment and the strict regulations placed on the industry, the solution would have to comply with Mine Safety and Health Administration (MSHA) regulations. Yet the product needed to allow for simple deployment to truly be a groundbreaking solution - increasing miner safety and changing daily operations for the better.
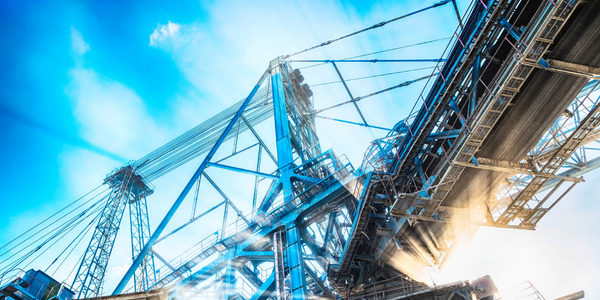
Case Study
Mining Firm Quadruples Production, with Internet of Everything
Dundee Precious Metal’s flagship mine, in Chelopech, Bulgaria, produces a gold, copper, and silver concentrate set a goal to increase production by 30%. Dundee wanted to increase production quality and output without increasing headcount and resources, improve miner safety, and minimize cost.
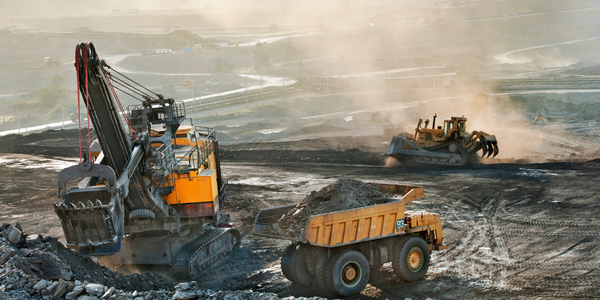
Case Study
Fastenal Builds the Future of Manufacturing with MachineMetrics
Fastenal's objective was to better understand their machine downtime, utilization, quality issues, and to embrace cutting-edge manufacturing technology/process improvement capabilities to bring their team to the next level. However, there was a lack of real-time data, visualization, and actionable insights made this transition impossible.
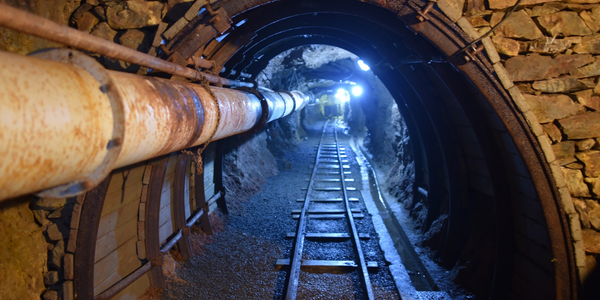
Case Study
Joy Mining Systems
Joy equipment faces many challenges. The first is machine integration and control. The business end of the machine has a rapidly-spinning cylinder with 6-inch diamond-studded cutting teeth. It chews through rock at rates measured in tens of tons per minute. The system grinds through the rock in front, creating a rectangular mine tunnel. Hydraulic lifters support the ceiling as the machine moves forward. Automated drills and screws drive 3-ft long screws into the ceiling to stabilize it. The rock and coal fall into a set of gathering "fingers" below the cutting cylinder. These fingers scoop up the rock and coal and deposit it onto a conveyor belt. The conveyor passes under the machine and out the back. A train of conveyor belt cars, up to a mile long, follows the cutter into the mine. The rock shoots along this train at over 400 feet per minute until it empties into rail cars at the end. Current systems place an operator cage next to the cutter. Choking dust (potentially explosive), the risk of collapse and the proximity of metal and rock mayhem make the operator cage a hazardous location.
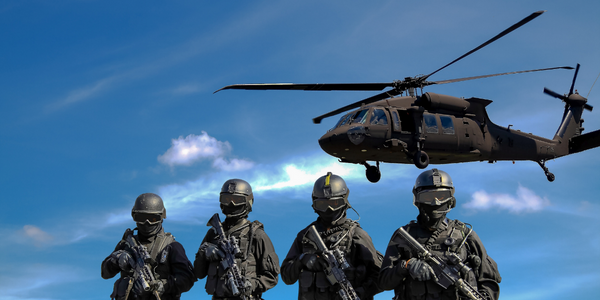
Case Study
Data Capture for Afghanistan Forces
Electronic equipments on the field of Afghanistan provided information on the status of the vehicle and to identify potential threats surrounding it to the British Force. The monitoring and interpretation of this data requires robust and sophisticated digitization for data capture and communication.