下载PDF
Securing High Availability and Service at Michelin Nordic
技术
- 功能应用 - 仓库管理系统 (WMS)
- 自动化与控制 - 自动化与过程控制系统
适用行业
- 汽车
- 运输
适用功能
- 仓库和库存管理
- 物流运输
用例
- 仓库自动化
- 库存管理
- 供应链可见性(SCV)
服务
- 系统集成
- 培训
挑战
The Michelin Nordic distribution center in Kungälv, Sweden, faced significant challenges due to outdated equipment that could not handle the increased volume and rapid goods-flows during peak seasons. The existing AGVs and cranes became bottlenecks, and obtaining spare parts for these aging systems was increasingly difficult. The need for modernization was clear to maintain high levels of customer service and efficient supply chain operations. The project aimed to replace the old equipment with modern, high-efficiency systems while minimizing disruption to daily operations.
关于客户
Michelin, founded in 1889 by André and Edouard Michelin, is the world’s leading tire manufacturer. The company employs over 110,000 people and generates sales exceeding 20 billion Euros. Michelin operates in 170 countries, producing and selling a wide range of tires for various vehicles, including passenger cars, trucks, buses, tractors, motorcycles, and aircraft. The company has 72 production facilities across 19 countries. Michelin Nordic AB, a regional branch, serves Sweden, Denmark, Norway, and Finland, focusing on high customer service levels and an efficient supply chain.
解决方案
Michelin Nordic partnered with Swisslog to modernize their distribution center in Kungälv. The project, known as The Retrofit Project, involved replacing the existing eight stacker cranes with new, high-efficiency cranes and installing a fixed conveyor system to replace the outdated AGVs. The modernization aimed to improve capacity and efficiency, particularly during peak seasons. The project was executed with minimal disruption to daily operations, including the use of an external warehouse during the installation of the new conveyor system. Swisslog's understanding of Michelin's challenges and their professional execution ensured the project was completed on time and as planned.
运营影响
数量效益
相关案例.
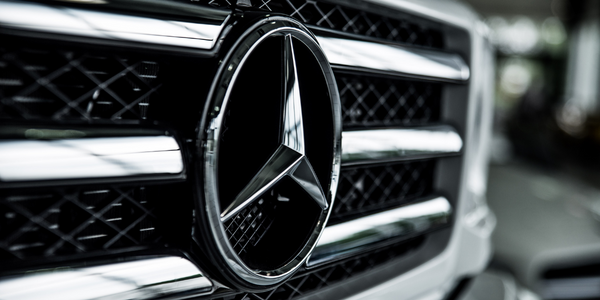
Case Study
Integral Plant Maintenance
Mercedes-Benz and his partner GAZ chose Siemens to be its maintenance partner at a new engine plant in Yaroslavl, Russia. The new plant offers a capacity to manufacture diesel engines for the Russian market, for locally produced Sprinter Classic. In addition to engines for the local market, the Yaroslavl plant will also produce spare parts. Mercedes-Benz Russia and his partner needed a service partner in order to ensure the operation of these lines in a maintenance partnership arrangement. The challenges included coordinating the entire maintenance management operation, in particular inspections, corrective and predictive maintenance activities, and the optimizing spare parts management. Siemens developed a customized maintenance solution that includes all electronic and mechanical maintenance activities (Integral Plant Maintenance).
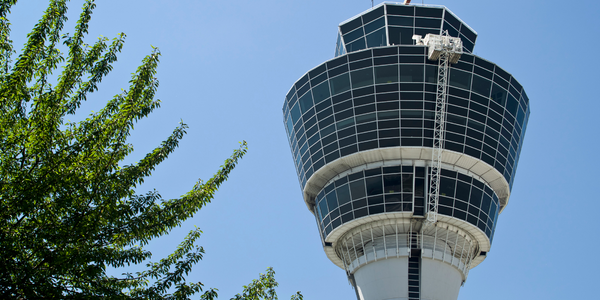
Case Study
Airport SCADA Systems Improve Service Levels
Modern airports are one of the busiest environments on Earth and rely on process automation equipment to ensure service operators achieve their KPIs. Increasingly airport SCADA systems are being used to control all aspects of the operation and associated facilities. This is because unplanned system downtime can cost dearly, both in terms of reduced revenues and the associated loss of customer satisfaction due to inevitable travel inconvenience and disruption.
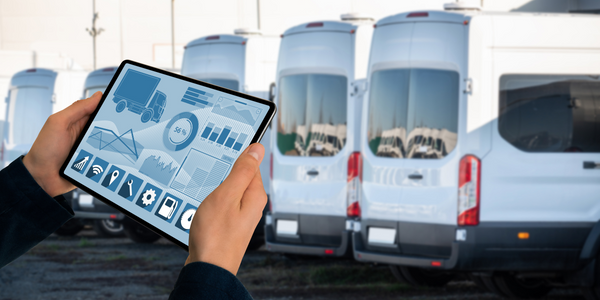
Case Study
IoT-based Fleet Intelligence Innovation
Speed to market is precious for DRVR, a rapidly growing start-up company. With a business model dependent on reliable mobile data, managers were spending their lives trying to negotiate data roaming deals with mobile network operators in different countries. And, even then, service quality was a constant concern.
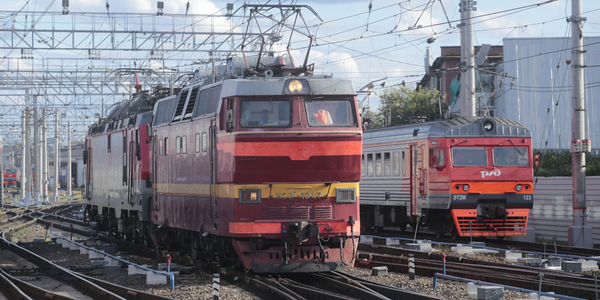
Case Study
Digitize Railway with Deutsche Bahn
To reduce maintenance costs and delay-causing failures for Deutsche Bahn. They need manual measurements by a position measurement system based on custom-made MEMS sensor clusters, which allow autonomous and continuous monitoring with wireless data transmission and long battery. They were looking for data pre-processing solution in the sensor and machine learning algorithms in the cloud so as to detect critical wear.