下载PDF
Siempelkamp Uses QlikView to Calculate and Manage Projects
技术
- 分析与建模 - 实时分析
- 应用基础设施与中间件 - 数据交换与集成
用例
- 实时定位系统 (RTLS)
- 预测性维护
服务
- 系统集成
- 数据科学服务
挑战
Siempelkamp Maschinen-und Anlagenbau, a machine and plant construction company, was facing challenges in maintaining transparency in their figures, project calculations, and deadlines. The construction of a plant can take 12-15 months from the planning stage to sign off, and throughout this period, all the managers involved must constantly make target/actual comparisons to ascertain progress status. The key questions were whether they were still within deadlines, whether all materials could be delivered and used on schedule, and whether all budgetary costs were being met. The company needed a tool that would allow them and indeed the users themselves, anytime and anywhere, to make the analyses and evaluations they needed for project control without having to rely on IT.
关于客户
Siempelkamp Maschinen-und Anlagenbau, based in Krefeld, Germany operates worldwide. It is a machine and plant construction company for the timber, rubber, and metal casting industry. The company manufactures 50–70 metres long steel assembly lines for the wood-processing industry. Once felled the trees are stripped of their bark and then chopped up. After processing them into wood fibre, these are variously glued and compressed to produce the chip, medium density fibreboard, or oriented strand board which comes off the assembly line. These go to the furniture and building division where they are further processed into countertops, laminates, or shelving. All units, which sell in the double digit million bracket, are unique. Technicians adjust the machines depending on the moisture content of the raw material for processing, whether poplar, oak, or other wood. The company also manufactures machines for the steel processing industry—examples include internal components for Airbus aero engine turbines, pipes for the Baltic pipeline, or wheels for railway rolling stock. A workforce of 1,700 is employed in the engineering and plant construction division of this medium-sized family business which has grown organically over the years. The group also has nuclear and metal casting divisions with an overall workforce of 2,600. Siempelkamp has its own production sites in Krefeld, China, and the Czech Republic and through its distribution network is represented worldwide with a world market share of around 70 per cent.
解决方案
Siempelkamp deployed QlikView in its organization to empower its managers and overall staff with transparent information on figures, project calculation, and deadlines. QlikView is installed in Internet Explorer and not on individual workstation computers, which helps to keep costs down. The software is simple to operate and so intuitive that extensive training and briefing sessions aren’t necessary. The in-memory technology means enormous efficiency gains. The system also lets users process information independently without IT support.
运营影响
数量效益
相关案例.
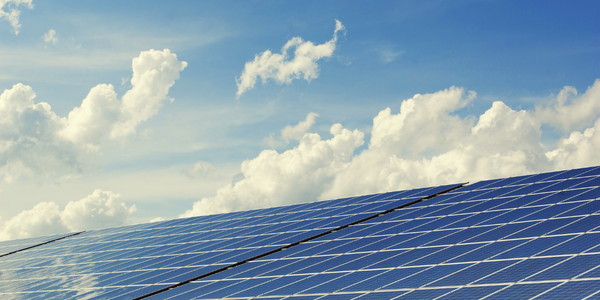
Case Study
Remote Monitoring & Predictive Maintenance App for a Solar Energy System
The maintenance & tracking of various modules was an overhead for the customer due to the huge labor costs involved. Being an advanced solar solutions provider, they wanted to ensure early detection of issues and provide the best-in-class customer experience. Hence they wanted to automate the whole process.
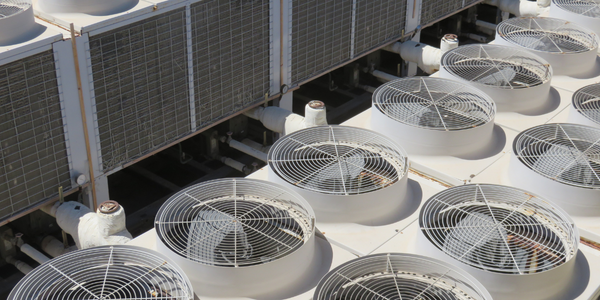
Case Study
Predictive Maintenance for Industrial Chillers
For global leaders in the industrial chiller manufacturing, reliability of the entire production process is of the utmost importance. Chillers are refrigeration systems that produce ice water to provide cooling for a process or industrial application. One of those leaders sought a way to respond to asset performance issues, even before they occur. The intelligence to guarantee maximum reliability of cooling devices is embedded (pre-alarming). A pre-alarming phase means that the cooling device still works, but symptoms may appear, telling manufacturers that a failure is likely to occur in the near future. Chillers who are not internet connected at that moment, provide little insight in this pre-alarming phase.
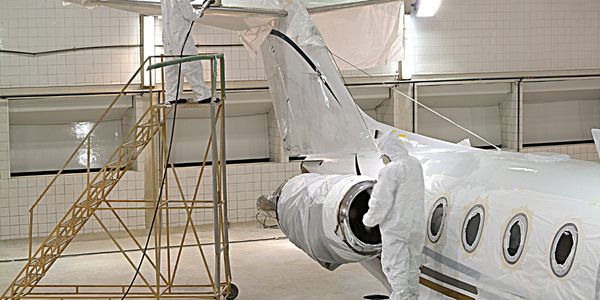
Case Study
Aircraft Predictive Maintenance and Workflow Optimization
First, aircraft manufacturer have trouble monitoring the health of aircraft systems with health prognostics and deliver predictive maintenance insights. Second, aircraft manufacturer wants a solution that can provide an in-context advisory and align job assignments to match technician experience and expertise.
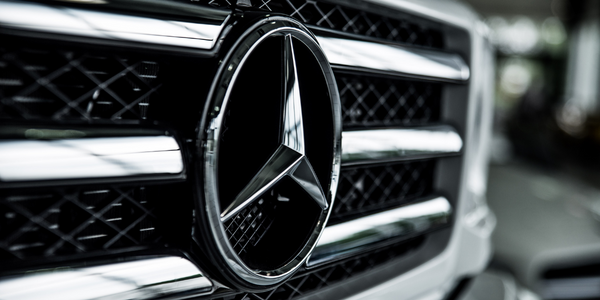
Case Study
Integral Plant Maintenance
Mercedes-Benz and his partner GAZ chose Siemens to be its maintenance partner at a new engine plant in Yaroslavl, Russia. The new plant offers a capacity to manufacture diesel engines for the Russian market, for locally produced Sprinter Classic. In addition to engines for the local market, the Yaroslavl plant will also produce spare parts. Mercedes-Benz Russia and his partner needed a service partner in order to ensure the operation of these lines in a maintenance partnership arrangement. The challenges included coordinating the entire maintenance management operation, in particular inspections, corrective and predictive maintenance activities, and the optimizing spare parts management. Siemens developed a customized maintenance solution that includes all electronic and mechanical maintenance activities (Integral Plant Maintenance).
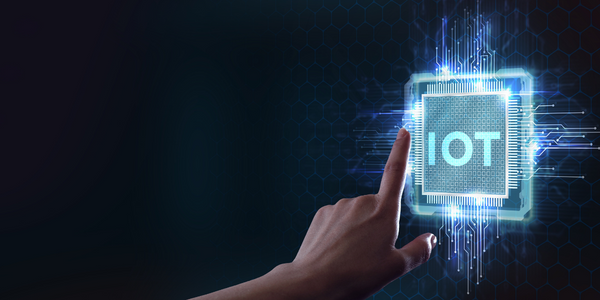
Case Study
Leading Tools Manufacturer Transforms Operations with IoT
Stanley Black & Decker required transparency of real-time overall equipment effectiveness and line productivity to reduce production line change over time.The goal was to to improve production to schedule, reduce actual labor costs and understanding the effects of shift changes and resource shifts from line to line.

Case Study
Asset Management and Predictive Maintenance
The customer prides itself on excellent engineering and customer centric philosophy, allowing its customer’s minds to be at ease and not worry about machine failure. They can easily deliver the excellent maintenance services to their customers, but there are some processes that can be automated to deliver less downtime for the customer and more efficient maintenance schedules.