下载PDF
Skaigh Engineering's Journey to Improved Casting with IoT
技术
- 分析与建模 - 数字孪生/模拟
- 功能应用 - 制造执行系统 (MES)
适用功能
- 产品研发
- 质量保证
用例
- 制造过程模拟
- 虚拟培训
服务
- 测试与认证
- 培训
挑战
Skaigh Engineering 是一家专门从事高质量铝重力压铸件的英国公司,在制造过程中面临着多项挑战。由于客户需求的增加和零件复杂性的增加,铸造行业正在经历重大变革。为了保持竞争力并在全球市场中发展,Skaigh 等铸件制造商需要解决降低开发和制造成本等问题。该公司正在处理浪费时间来改进客户较差的制造技术以及由于涉及继承模具的试错开发方法而导致的交货时间过长的问题。为了改进开发流程并应对这些挑战,Skaigh 开始探索模拟的使用。
关于客户
Skaigh Engineering 是一家位于英国德文郡的公司,专门生产高品质铝重力压铸件。该公司为各行业的客户提供服务,并提供涵盖铸造设计、模拟和制造的交钥匙交付方法。 Skaigh Engineering 提供一系列现场服务,包括砂型铸造原型、模具和工具制造、砂芯、热处理、各种表面光洁度处理以及完全机器定制的铸件。该组织致力于通过第一时间提供卓越的产品和服务,为客户在竞争激烈的市场中提供优势。
解决方案
Skaigh 与 Altair 合作伙伴 Origin Engineering Solutions 合作,提供设计和仿真解决方案。他们实施了 Altair® Inspire™ Cast,该工具使他们能够降低成本并缩短交货时间。他们解决的一个具体问题是重新设计一种工具,以替换使用了 15 年、磨损的致动器模具,该模具会产生过多的废料。 Skaigh 团队使用 Inspire Cast 模拟了旧方法,使零件填充可视化,并纠正了空气滞留等铸造缺陷。他们重新设计了浇注和浇道系统,以改进制造方法并减少废品产量。在另一个案例中,Skaigh 使用 Inspire Cast 来解决导致铸造轮圈表面缺陷的铸造问题。该软件显示出必须去除的空气滞留,从而导致了零件的重新设计并消除了空气滞留。
运营影响
数量效益
相关案例.
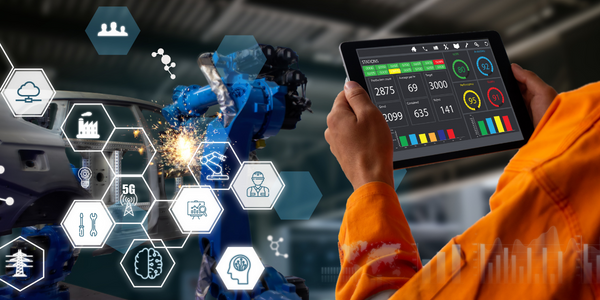
Case Study
Battery manufacturer Industrial Digital Twin
For optimum control of product quality, Banner relies on a high production depth. Its 560 production employees produce nearly all the components in¬-house that they need to make finished batteries on Banner’s six assembly lines. This includes the plastic parts for the battery cases as well as the paste-filled lead oxide grids. Their production involves two to five¬ days rest in maturing chambers to create optimum current absorption and storage capacity. Banner’s ongoing success was accompanied by a continuous, organic growth of the production facilities, adding or extending hall after hall until the complex filled the site that had seemed ever so spacious when the company moved here from a smaller place in 1959. These developments led to a heterogeneous production environment. “This confronts us with significant challenges, particularly concerning intra¬logistics issues, such as scheduling for the maturing chambers,” says Franz Dorninger, technical director at Banner. “We contemplated various ways to overcome this problem, including relocating to new premises.”
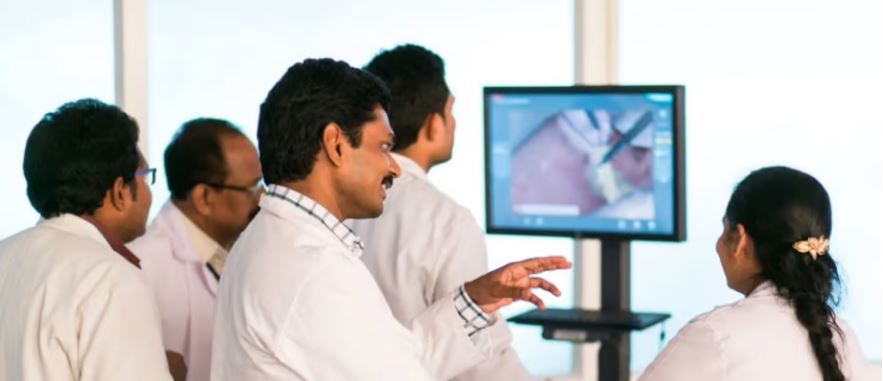
Case Study
Revolutionizing Medical Training in India: GSL Smart Lab and the LAP Mentor
The GSL SMART Lab, a collective effort of the GSL College of Medicine and the GSL College of Nursing and Health Science, was facing a challenge in providing superior training to healthcare professionals. As clinical medicine was becoming more focused on patient safety and quality of care, the need for medical simulation to bridge the educational gap between the classroom and the clinical environment was becoming increasingly apparent. Dr. Sandeep Ganni, the director of the GSL SMART Lab, envisioned a world-class surgical and medical training center where physicians and healthcare professionals could learn skills through simulation training. He was looking for different simulators for different specialties to provide both basic and advanced simulation training. For laparoscopic surgery, he was interested in a high fidelity simulator that could provide basic surgical and suturing skills training for international accreditation as well as specific hands-on training in complex laparoscopic procedures for practicing physicians in India.
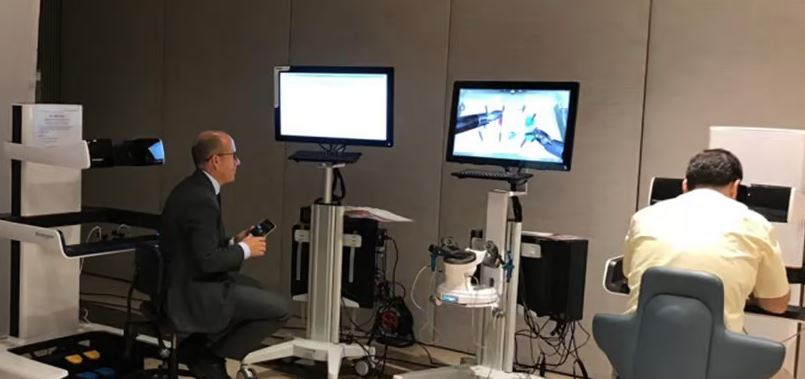
Case Study
Implementing Robotic Surgery Training Simulator for Enhanced Surgical Proficiency
Fundacio Puigvert, a leading European medical center specializing in Urology, Nephrology, and Andrology, faced a significant challenge in training its surgical residents. The institution recognized the need for a more standardized and comprehensive training curriculum, particularly in the area of robotic surgery. The challenge was underscored by two independent studies showing that less than 5% of residents in Italian and German residency programs could perform major or complex procedures by the end of their residency. The institution sought to establish a virtual reality simulation lab that would include endourological, laparoscopic, and robotic platforms. However, they needed a simulator that could replicate both the hardware and software of the robotic Da Vinci console used in the operating room, without being connected to the actual physical console. They also required a system that could provide both basic and advanced simulation training, and a metrics system to assess the proficiency of the trainees before they performed surgical procedures in the operating theater.

Case Study
Augmented Reality Medical Diagnostics by NHS
The UK’s National Health Service, the UK’s national public health care provider, trains thousands of healthcare assistants, nurses, and doctors every year and employs some 1.5 million people, making it a top five employer globally. As a result, the NHS is constantly searching for better ways to train their employees and achieve better learning results.One problem they identified was that certain subject areas were challenging for learners using conventional training methods, which are both costly and time consuming. They needed a solution that would accelerate knowledge transfer of key subject areas, reduce costs, and improve the number of people who can be exposed to training.
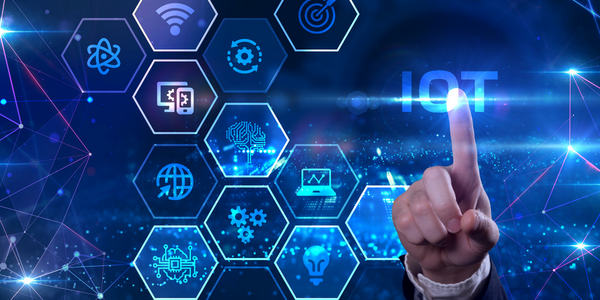
Case Study
Scalable IoT Empowering GreenFlex's Sustainable Growth
GreenFlex, a company that supports sustainable development, decarbonization, and energy efficiency, faced several challenges in its quest to expand its business. The company needed to deploy a robust and sustainable IoT technology to support its growth. It was crucial for them to monitor and control devices at customer sites in a safe and reliable manner. They also needed to integrate devices across a range of communication protocols and gather and act on data to meet efficiency targets. GreenFlex had previously built IoT capabilities into its digital platform, GreenFlexIQ, to monitor and manage customer sites remotely. However, they soon realized that they needed a new platform to support their ambitions. They needed a platform that could scale to connect more devices for production management and make it easier for the operations team to manage devices in the field.
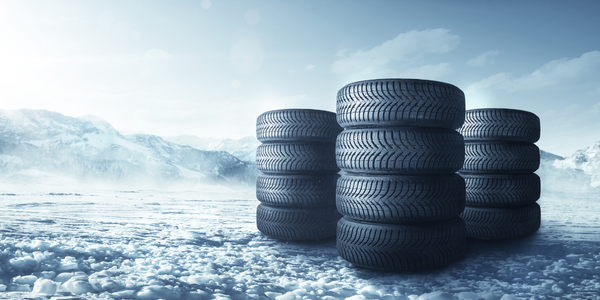
Case Study
Toyo Tire's Digital Transformation: Enhancing Product Development with IoT
Toyo Tire, a Japanese-based tire manufacturer, was facing the challenge of keeping up with the rapid changes in the automotive industry. With the advent of electric vehicles and connected cars, the company recognized the need to innovate and develop new types of tires to meet these specific needs. However, their existing product development processes were not sufficient to keep pace with the industry's transformation. The company's data was held in siloes, preventing users from easily accessing all the information they needed. This lack of integration was hindering their ability to innovate and develop new products efficiently. Toyo Tire needed a solution that would accelerate its product development processes and put innovation at the core of its activities.