下载PDF
Software AG and Wipro Ltd. Cater to Connected Customers in Real Time
技术
- 分析与建模 - 实时分析
- 网络安全和隐私 - 云安全
- 平台即服务 (PaaS) - 数据管理平台
适用行业
- 航天
- 汽车
- 医疗保健和医院
适用功能
- 离散制造
- 产品研发
- 质量保证
用例
- 边缘计算与边缘智能
- 机器状态监测
- 预测性维护
- 实时定位系统 (RTLS)
- 视觉质量检测
服务
- 云规划/设计/实施服务
- 数据科学服务
- 系统集成
挑战
With the Internet of Things (IoT) expected to connect 50 billion devices by 2020, the way products are used and interacted with is changing. More products are being embedded with sensors that provide real-time data on how customers are using them. This presents a challenge for businesses to adapt dynamically and understand their connected customers better. One of the most overlooked topics in IoT is security. The platform allows you to give access to your distributors and customers using an advanced mapping authorization engine. The endpoint security technologies are customized specifically to the machine world of the IoT, offering tighter security control than networked VPN solutions.
关于客户
Wipro Limited is a leading global information technology, consulting and business process services company. They harness the power of cognitive computing, hyper-automation, robotics, cloud, analytics and emerging technologies to help their clients adapt to the digital world and make them successful. Recognized globally for its comprehensive portfolio of services, strong commitment to sustainability and good corporate citizenship, Wipro has a dedicated workforce of over 170,000, serving clients across six continents. They discover ideas and connect the dots to build a better and a bold new future.
解决方案
Wipro Looking Glass, the IoT solution from Software AG and Wipro Ltd., leverages the proven big data streaming technology of Software AG and the expertise of Wipro Ltd., a leader in building the IoT for business outcomes. The solution platform enables a fast and easy entry into the real-time insights and business opportunities offered by the IoT. Wipro Looking Glass combines a real-time analytics engine, in-memory database technology, a real-time user interface and data mashup technologies. These components are proven to scale in high speed and big data environments in industries such as financial services, manufacturing and supply chain, and telecommunications. Software AG’s streaming analytics technology integrates, captures, analyzes and responds to data captured by products that are connected to the IoT. The solution can run both on-premises and in a single or multiple clouds simultaneously. Through leading-edge data management technologies, the platform offers unlimited scalability.
运营影响
数量效益
相关案例.
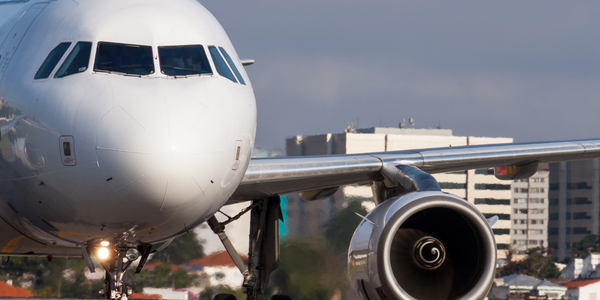
Case Study
Airbus Soars with Wearable Technology
Building an Airbus aircraft involves complex manufacturing processes consisting of thousands of moving parts. Speed and accuracy are critical to business and competitive advantage. Improvements in both would have high impact on Airbus’ bottom line. Airbus wanted to help operators reduce the complexity of assembling cabin seats and decrease the time required to complete this task.
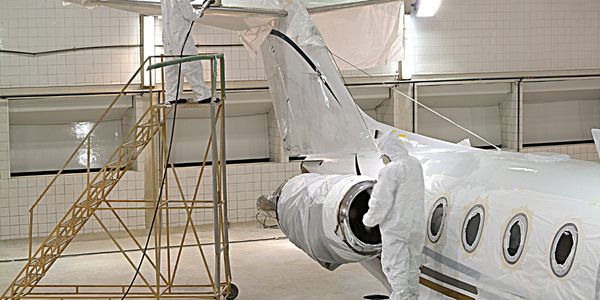
Case Study
Aircraft Predictive Maintenance and Workflow Optimization
First, aircraft manufacturer have trouble monitoring the health of aircraft systems with health prognostics and deliver predictive maintenance insights. Second, aircraft manufacturer wants a solution that can provide an in-context advisory and align job assignments to match technician experience and expertise.
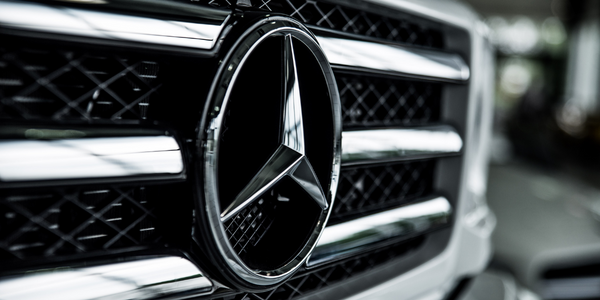
Case Study
Integral Plant Maintenance
Mercedes-Benz and his partner GAZ chose Siemens to be its maintenance partner at a new engine plant in Yaroslavl, Russia. The new plant offers a capacity to manufacture diesel engines for the Russian market, for locally produced Sprinter Classic. In addition to engines for the local market, the Yaroslavl plant will also produce spare parts. Mercedes-Benz Russia and his partner needed a service partner in order to ensure the operation of these lines in a maintenance partnership arrangement. The challenges included coordinating the entire maintenance management operation, in particular inspections, corrective and predictive maintenance activities, and the optimizing spare parts management. Siemens developed a customized maintenance solution that includes all electronic and mechanical maintenance activities (Integral Plant Maintenance).
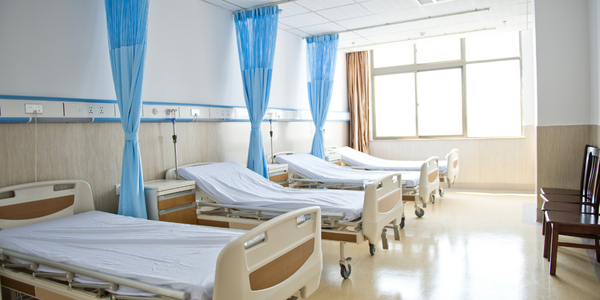
Case Study
Hospital Inventory Management
The hospital supply chain team is responsible for ensuring that the right medical supplies are readily available to clinicians when and where needed, and to do so in the most efficient manner possible. However, many of the systems and processes in use at the cancer center for supply chain management were not best suited to support these goals. Barcoding technology, a commonly used method for inventory management of medical supplies, is labor intensive, time consuming, does not provide real-time visibility into inventory levels and can be prone to error. Consequently, the lack of accurate and real-time visibility into inventory levels across multiple supply rooms in multiple hospital facilities creates additional inefficiency in the system causing over-ordering, hoarding, and wasted supplies. Other sources of waste and cost were also identified as candidates for improvement. Existing systems and processes did not provide adequate security for high-cost inventory within the hospital, which was another driver of cost. A lack of visibility into expiration dates for supplies resulted in supplies being wasted due to past expiry dates. Storage of supplies was also a key consideration given the location of the cancer center’s facilities in a dense urban setting, where space is always at a premium. In order to address the challenges outlined above, the hospital sought a solution that would provide real-time inventory information with high levels of accuracy, reduce the level of manual effort required and enable data driven decision making to ensure that the right supplies were readily available to clinicians in the right location at the right time.