下载PDF
ST Powder Coatings Uses Wonderware Software Solution to Connect ERP and Plant Systems and Fill Thousands of Customized Orders Every Day
技术
- 平台即服务 (PaaS) - 连接平台
- 平台即服务 (PaaS) - 数据管理平台
适用行业
- 化学品
适用功能
- 离散制造
- 质量保证
用例
- 自动化制造系统
- 供应链可见性(SCV)
服务
- 软件设计与工程服务
- 系统集成
挑战
ST Powder Coatings, a producer of high-end, intricately customized thermosetting powder coatings, needed a software solution that could integrate information between the plant and business systems, and enable them to keep production efficiency and product quality consistently high. The company had a requirement to get the plant up and running as quickly as possible. They needed a very short development time to start shipping product within 4 months. The integration of information between the business system and the plant was key to ST Powder Coatings' ability to accurately fill its customers unique and variant orders. The software also needed to assist ST Powder Coatings quickly identify the source of product variations when a color does not turn out precisely how the customer expected.
关于客户
ST Powder Coatings is a producer of high-end, intricately customized thermosetting powder coatings. The company's products are based completely on ecological components and can be found on motorcycles, car accessories, outdoor fixtures, agricultural machinery and household appliances. Providing colors that meet its customers' specific requirements -- and using the best and most effective technology to do so -- is key to the company's business model. The company has used Wonderware software since before its first day in operation. In fact, the Wonderware Production and Performance Management system was up and running before construction of its headquarters and plant was complete.
解决方案
ST Powder Coatings opted for a Wonderware Software Solution because it would enable the company to ramp up and begin fulfilling orders within 4 months. The company's system includes the Wonderware Industrial Application Server, IndustrialSQL Server historian, ActiveFactory trending and analysis software, InTouch View clients, and SCADAlarm alert management software. The Industrial Application Server's object-based approach to software development was integral to building the system at such an accelerated rate. The development approach enabled by the Industrial Application Server's underlying ArchestrA industrial automation and information software architecture saved AUTOWARE's and ST Powder Coatings' software engineers an incredible amount of time. The software's integration attributes enable ST Powder Coatings to focus on getting the most out of the factory.
运营影响
数量效益
相关案例.
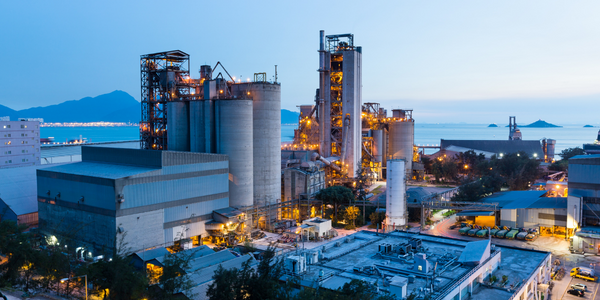
Case Study
Honeywell - Tata Chemicals Improves Data Accessibility with OneWireless
Tata was facing data accessibility challenges in the cement plant control room tapping signals from remote process control areas and other distant locations, including the gas scrubber. Tata needed a wireless solution to extend its control network securely to remote locations that would also provide seamless communication with existing control applications.
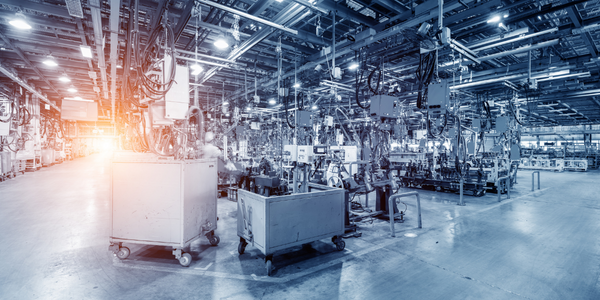
Case Study
Advanced Elastomer Systems Upgrades Production
In order to maintain its share of the international market for thermoplastic elastomers AES recently expanded its Florida plant by adding a new production line. While the existing lines were operating satisfactorily using a PROVOX distributed control system with traditional analog I/O, AES wanted advanced technology on the new line for greater economy, efficiency, and reliability. AES officials were anxious to get this line into production to meet incoming orders, but two hurricanes slowed construction.

Case Study
Wireless GPS Tracking & Security Monitoring
Enhancing the security of hazardous freight and ensuring compliance with Homeland Security’s Transportation Security Administration mandate that all trains carrying chemicals capable of creating a toxic inhalation condition are equipped with on-board safety monitoring systems.
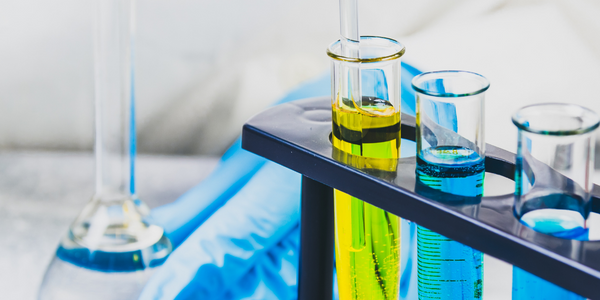
Case Study
Field Device Asset Management For Chemical Company in China
Chinese chemical subsidiary of multinational corporation serves customers throughout the world. Sales offices and research and technology centers are strategically located to provide rapid response to customer requests. Just two workers were assigned to maintain thousands of intelligent instruments in three production units, so they could do little more than react to device issues as they appeared. This costly maintenance method inevitably led to unexpected downtime when a critical instrument failed. Plant management recognized the need to change from reactive to predictive maintenance for all assets, including instruments and control valves, but help was needed in implementing such a technology-based initiative.
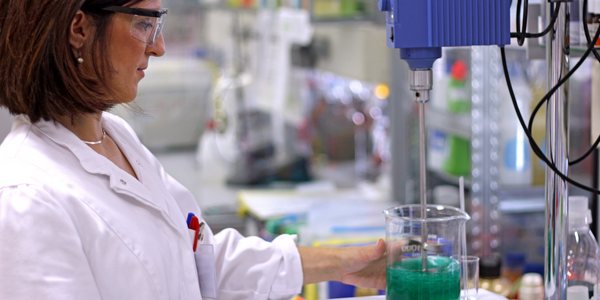
Case Study
Industrial Workforce Mobility for Improved Safety & Operations
Huntsman Corporation, a global manufacturer and marketer of differentiated chemicals, undertook an aggressive program to eliminate injuries, product defects, and environmental releases at their Port Neches facility. Termed “Project Zero”, this program required a completely mobile solution to empower operations and maintenance personnel to capture defects, track work progress and make process and safety related decisions in real-time.