下载PDF
Success Factors for Machine Connection
技术
- 平台即服务 (PaaS) - 连接平台
适用行业
- 汽车
适用功能
- 离散制造
- 质量保证
用例
- 机器状态监测
- 预测性维护
- 工厂可见化与智能化
服务
- 系统集成
- 数据科学服务
挑战
In today’s manufacturing facilities, there is a large mix of heterogeneous machines and control types, where signals must be collected, aggregated and evaluated. The solution to this common problem is a centralized system, which can seamlessly “plug and play” with any type of machine CNC controller or PLC. However, machine connection and integration capabilities are key differentiators when selecting the right MES technology provider. The experience level and readiness of the technology provider determines the time and costs required to successfully connect any machine. Standardized interfaces to all common machine controls, via direct plug-ins, must be created, otherwise the time required for connecting the machines, is unmanageable. In a pilot project initiated by an MES provider, a major German tool manufacturer determined that connections to some of their machines were very time-consuming, costly and in some cases not possible. Even after months of work, some challenging machine controls types remained unconnected. The MES provider lacked expertise and the necessary plug-ins.
关于客户
The customer in this case study is a major German tool manufacturer. The company operates a modern shop floor and aims to measure and visualize the performance of machines and systems in real time. The company's goal is to create a transparent factory, where production is virtually mirrored and inaccuracies and wastes can be immediately identified and eliminated. The company aims to create a “Cyber-Physical System” that can analyze and optimize the performance, availability and quality of the production processes, leading to productivity increases of 20% or more within 12 months or less. However, the company faced challenges in connecting to some of their machines, which was very time-consuming, costly and in some cases not possible.
解决方案
FORCAM offers sophisticated and powerful plug-ins for a variety of machine types and control systems. The integration of machines and production data is made possible in 3 steps: Capture Data, Import Data, Interpret and Analyze Data. To connect with heterogeneous controls, FORCAM uses three methods for machine data acquisition. The selected method for connection depends on the machinery and the desired amount of information to be captured. The machine data connection (MDC) can be fully adopted as there is little room for error; the more data collected automatically, the better the data integrity and the less resources wasted for manual reporting. After all process and measurement data is collected, it is uploaded in the so-called DCU (Data Collection Unit). Various software plug-ins ensure that the above-mentioned and other protocols can be processed. The original machine signals are not the only information needed for production control. A logic device is needed, that calculates the desired operating conditions from a plurality of signals and additional information.
运营影响
数量效益
相关案例.
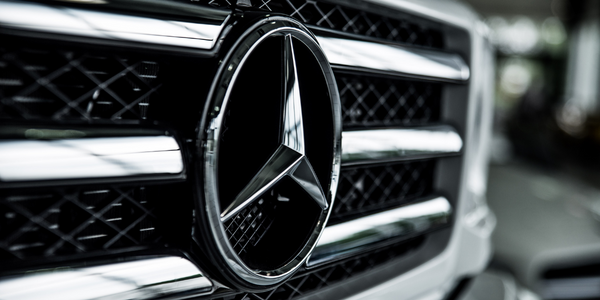
Case Study
Integral Plant Maintenance
Mercedes-Benz and his partner GAZ chose Siemens to be its maintenance partner at a new engine plant in Yaroslavl, Russia. The new plant offers a capacity to manufacture diesel engines for the Russian market, for locally produced Sprinter Classic. In addition to engines for the local market, the Yaroslavl plant will also produce spare parts. Mercedes-Benz Russia and his partner needed a service partner in order to ensure the operation of these lines in a maintenance partnership arrangement. The challenges included coordinating the entire maintenance management operation, in particular inspections, corrective and predictive maintenance activities, and the optimizing spare parts management. Siemens developed a customized maintenance solution that includes all electronic and mechanical maintenance activities (Integral Plant Maintenance).
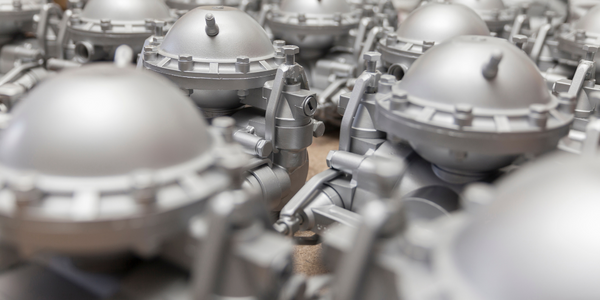
Case Study
Monitoring of Pressure Pumps in Automotive Industry
A large German/American producer of auto parts uses high-pressure pumps to deburr machined parts as a part of its production and quality check process. They decided to monitor these pumps to make sure they work properly and that they can see any indications leading to a potential failure before it affects their process.