下载PDF
Sutphen: Firing Up Purchasing and Manufacturing with Microsoft Dynamics AX
技术
- 功能应用 - 企业资源规划系统 (ERP)
适用行业
- 特种车辆
用例
- 自动化制造系统
- 供应链可见性(SCV)
服务
- 系统集成
- 培训
挑战
With an increase in customer demand, inefficient and disparate systems threatened to undermine the company’s growth. An 8-12 week time gap existed between when an order was taken, and engineering actually began, resulting in extra effort and costs incurred to make sure trucks were delivered on time. The team at Sutphen was utilizing a mix of legacy systems including a custom-developed AS 400 system and Macola. The team at Sutphen sought a unified ERP solution to address workflow, integration, inventory, and productivity issues.
关于客户
Sutphen, a fire apparatus manufacturer, was founded in 1890 by C.H. Sutphen, and now has four manufacturing facilities. Sutphen produces all types of fire-related vehicles on their own chassis including the usual engines, ladders, and rescues but also provides bodies for commercial chassis applications. The company still produces midmount aerials as either a tower ladder platform (with a bucket/basket) or in a ladder tower form (no bucket) plus industrial application aerials today.
解决方案
Sutphen, with the help of Velosio, rolled out Microsoft Dynamics AX to over 50 users across multiple departments. Sutphen implemented functionality to automate production, sales configuration, project management, supply chain management, and financials. Velosio helped Sutphen with data conversion, setup and configuration, user training, user acceptance testing, and cutover support.
运营影响
数量效益
相关案例.
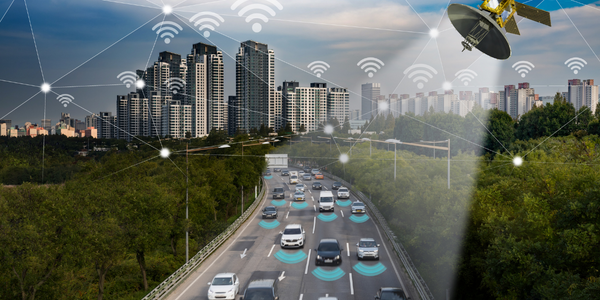
Case Study
Transformation for IoT Business Model in Connected Industrial Vehicles
CNH Industrial wanted to put IoT-enabled viechles onto the market. Whether monitoring a single machine or integrating an entire fleet, operators are able to track the status, speed, and movement of machines and their performance and also receive alerts on issues that may require service by a qualified technician to improve uptime and overall effectiveness of the vehicle.
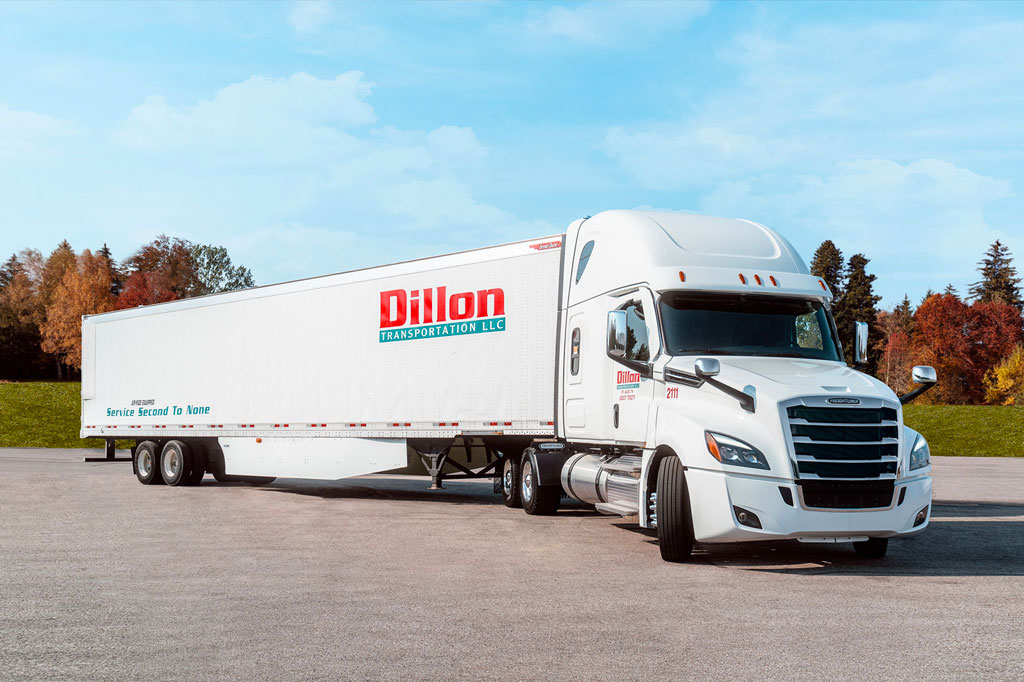
Case Study
Scalability Through IoT: Dillon Transportation's Growth with Innovative Access
Dillon Transportation, a dry van transportation company, experienced significant growth since its inception in 1996. From a humble beginning with one truck and two drivers, the company expanded to a fleet of 125 trucks and 170 drivers and crew members. However, this rapid growth brought about a challenge. The owner, Donnie Dillon, found it increasingly difficult to keep track of every driver and truck in his fleet. He could no longer remember the specifics of each trip, which he previously kept in his head. The company needed a more sophisticated way of storing information about drivers and loads. They required a system that would allow employees to access the specifics of each trip easily. The challenge was to find a solution that could manage the growing complexity of their operations.
Case Study
InterChange Group Enhances Cold Storage Efficiency with IoT Integration
InterChange Group, a cold-storage warehousing and distribution company, was faced with the challenge of increasing the efficiency of its cold storage facility to better service a local customer. The company needed to prove its capability to handle growing volumes in the future. The specific challenge was to integrate their new fleet of semi-automated forklifts with the Camelot Excalibur Warehouse Management System (WMS). The deployment of this technology investment, especially with temperature and date-sensitive food products, within a tight timeline, posed significant challenges.
Case Study
Successful 5G and Wi-Fi Network Convergence Solution for a Power Plant in China
To thrive in the industry 4.0 era, many factories are always looking for ways to improve efficiency and enhance reliability, and power plants are no exception. Any idle time resulting from an operational glitch directly impacts both the top and bottom lines of the business. Thus, the network is central to everything the plant generates. To improve the network infrastructure, the Milesight CPE units, which are 5G-ready and Wi-Fi integrated, are implemented in a power plant to provide a wireless solution for high-speed, reliable connections with low latency.The Beihai Power Plant Phase II is an expansion project, which is a major project promoted by GFIG to build a stable and reliable “energy network” for Guangxi province, China.A 24-by-7 operation spread across 136,500 square meters (0.05 square miles). They were actively seeking a solution with the latest wireless network technology so that they could successfully interlink all mobile devices and office equipment without any downtime, meanwhile, exchange the data securely on the private network.Frustrated with network downtime, unstable connectivity, and spotty coverage, this coal-fired Beihai power plant was desperate.Wireless DeploymentTime equals money. Wired deployment is not an option due to the tricky and time-consuming process, and if a buried cable is broken, it is expensive to repair, while industrial wireless deployment saves significant costs compared to an equivalent wired installation.Extensive ConnectionsMany smartphones and tablets in areas of the plant must be connected to wireless networks to enhance workers’ capabilities, saving time and money in the long run.Dedicated NetworkA dedicated or private network is preferred as it is self-contained that can be deployed almost anywhere and managed centrally, providing a higher level of security.Harsh Work EnvironmentMetal buildings, machinery, massive magnets, extremely hot temperatures, and high humidity made it difficult to gain dependable signals or stable connections.Having tried some of the most well-known Wi-Fi and cellular solutions on the market, the IT network staff at the power plant turned to Milesight 5G CPE units with minimal investment in the new infrastructure.
Case Study
Forklift Manufacturer Streamlines Design Process with Altair’s HyperWorks Suite
NACCO Materials Handling Group (NMHG), a leading producer of lift trucks, was facing a significant challenge in their product development process. The company had been using finite-element analysis (FEA) for 25 years, but this required the construction of several iterations of physical prototypes to test their designs. This process was not only costly but also time-consuming, leading to delays in bringing products to market. The company was in dire need of a solution that could reduce the time to market without compromising on the quality of their products. The ultimate goal was to virtually design, test, and evaluate each product before any physical prototypes were made, thereby saving costs and gaining a competitive advantage.