下载PDF
Tekfen Reduces Project Execution Times and Cost with AVEVA E3D
技术
- 应用基础设施与中间件 - 数据交换与集成
- 功能应用 - 产品数据管理系统
适用功能
- 离散制造
- 产品研发
用例
- 数字孪生
- 自动化制造系统
服务
- 软件设计与工程服务
- 系统集成
挑战
Tekfen Engineering, an international Turkish company, was facing challenges due to its global operations across different countries, time zones, and languages. The company was unable to visualize 3D designs, and the verification of design and data iterations required time-consuming face-to-face meetings. The document control procedures were complicated and required much verification. The work was often done across time zones and in multiple languages, which increased the risk of misinterpretation of data, drawings, changes, and specifications. The company was looking to improve the speed, quality, and profitability of its projects by taking intelligent design to the next level. The geographic spread of its projects and multiple requirements for inter-company collaboration dictated a re-evaluation of technologies used in the company’s design process.
关于客户
Tekfen Engineering is an international Turkish company with a client base across Turkey, the Middle East, Africa, and Azerbaijan. The company has projects planned in Ghana, Morocco, Kuwait, Qatar, Bulgaria, and South East Asia. Tekfen Engineering is familiar with geographic and cultural complications due to its global operations. The company was accustomed to using AVEVA PDMS™ for its 3D plant designs and was looking to improve the speed, quality, and profitability of its projects by taking intelligent design to the next level. The geographic spread of its projects and multiple requirements for inter-company collaboration dictated a re-evaluation of technologies used in the company’s design process.
解决方案
In late 2014, Tekfen Engineering chose AVEVA Everything3D (AVEVA E3D), a solution that enables clash-free, multi-discipline 3D design. The complete migration of Tekfen's PDMS projects to AVEVA E3D took less than ten weeks. AVEVA was able to alleviate Tekfen’s concerns regarding the transition, as AVEVA E3D is built on existing, trusted AVEVA technology. This makes incremental deployment possible by project, department, and team. AVEVA E3D can easily be deployed on the same projects as PDMS and the transition is smooth, easy to upgrade and, above all, risk-free. A key improvement that will increase productivity for all clients is the new graphical interaction with the canvas. This means it is much more natural to learn and quick to adopt.
运营影响
数量效益
相关案例.
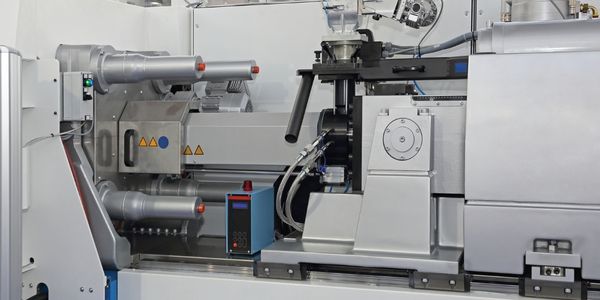
Case Study
Plastic Spoons Case study: Injection Moulding
In order to meet customer expectations by supplying a wide variety of packaging units, from 36 to 1000 spoons per package, a new production and packaging line needed to be built. DeSter wanted to achieve higher production capacity, lower cycle time and a high degree of operator friendliness with this new production line.
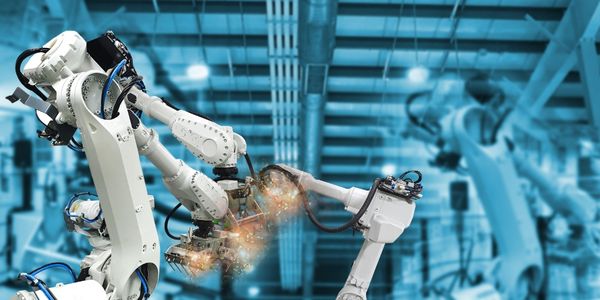
Case Study
Robot Saves Money and Time for US Custom Molding Company
Injection Technology (Itech) is a custom molder for a variety of clients that require precision plastic parts for such products as electric meter covers, dental appliance cases and spools. With 95 employees operating 23 molding machines in a 30,000 square foot plant, Itech wanted to reduce man hours and increase efficiency.
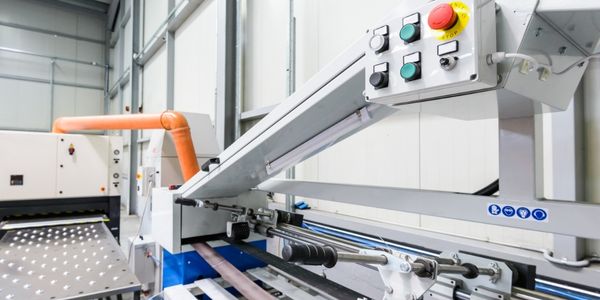
Case Study
Fully Automated Visual Inspection System
Tofflon has developed a fully automatic machine that uses light to inspect vials, medicine bottles, or infusion containers for glass fragments, aluminum particles, rubber grains, hairs, fibers, or other contaminants. It also detects damaged containers with cracks or inclusions (microscopic imperfections), automatically removing faulty or contaminated products. In order to cover all production processes for freeze-dried pharmaceuticals, Tofflon needed to create an open, consistent, and module-based automation concept.
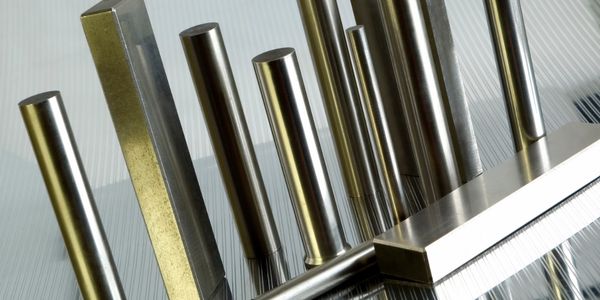
Case Study
RobotStudio Case Study: Benteler Automobiltechnik
Benteler has a small pipe business area for which they produce fuel lines and coolant lines made of aluminum for Porsche and other car manufacturers. One of the problems in production was that when Benteler added new products, production had too much downtime.
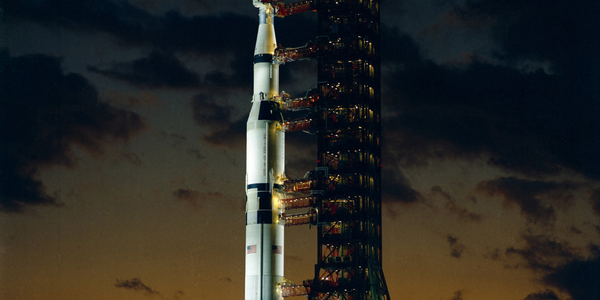
Case Study
SAP Leonardo Enabling Rocket Science
At times, ULA has as many as 15 different operating systems dedicated to overlapping processes, such as rocket design, testing, and launch. Multiple systems created unnecessary costs and unwanted confusion among workers at offices, factories, and launch sites in different location. In order to improve collaboration and transparency during vital activities that directly influence mission success, ULA wanted to improve data sharing and streamline manufacturing processes.