下载PDF
Toray Plastics (America), Inc. Optimizes Manufacturing Operational Performance with Big Data Analytics
技术
- 分析与建模 - 大数据分析
- 分析与建模 - 预测分析
- 分析与建模 - 实时分析
适用行业
- 化学品
- 消费品
- 食品与饮料
适用功能
- 离散制造
- 质量保证
用例
- 库存管理
- 预测性维护
服务
- 软件设计与工程服务
- 系统集成
挑战
The diversification of today’s “food-on-demand” culture has led to an increasing need for keeping food products safe and fresh for extended periods of time—all while preserving its original flavor. Consumers expect their food products to maintain a relatively long shelf life without compromising quality. And as a result of this growing demand, Toray Plastics was faced with producing better food packaging film than ever before. Food packaging film is composed of very unique components for protecting against oxygen and water, and producing these films is no easy task. It requires very tight production processes that are examined with the utmost scrutiny to ensure the highest quality. So, in order for Toray Plastics to meet its vision to remove waste across the organization and remain competitive, the company implemented a new integrated system that allowed it to monitor its film manufacturing much more closely to ensure exact quality standards in every unit.
关于客户
Toray Industries, Inc. is behind the manufacturing of many of the shiny metallized packages that protect a variety of food products, from snack food to cookies, prepared meals, candy, crackers, and granola bars. Toray Industries—headquartered in Tokyo, Japan—is the world leader in high-performance films, synthetic fibers and textiles, carbon fibers, plastics, chemicals, and pharmaceuticals. Today, the organization operates 254 facilities in 26 countries with more than 45,000 employees—with annual sales exceeding $19 billion. Toray Plastics (America), Inc., an American based subsidiary of Toray Industries, is responsible for manufacturing the Torayfan Polypropylene Film, Lumirror Polyester Film, and Toraypef Olefin Foams across its Rhode Island and Virginia facilities. Within its facilities, Toray Plastics operates through a bi-modal approach—a combination of standard operations mixed with agile and cutting-edge techniques—that is fueled by technology. With a keen focus on lean activities, the company’s strategy goes beyond the standard “mode one” of keeping a business up and running. Instead, Toray Plastics consistently strives to integrate innovation, creativity, and experimentation into all of its processes.
解决方案
Toray Plastics started leveraging Plant Applications from GE Digital, part of the Brilliant Manufacturing suite. As an on-premises solution, Plan Applications allowed Toray Plastics to collect real-time data directly from edge devices and assets for critical key performance indicators, as well as perform batch analyses to optimize operations. Plant Applications enabled operators to oversee manufacturing on a more granular level and reduce the production of defective film (first pass quality), which improved overall equipment effectiveness, quality, and reduced material waste, thus helping to increase efficiencies and decrease costs. Toray Plastics also tightly integrated Plant Applications with its SAP software, which made it extremely cost effective and scalable globally. The two systems continuously pass about 30,000 pieces of information a day between one another— covering everything from inventory status to bill of materials, customer specifications, and production order status. This alignment between GE Digital and SAP allowed both systems to utilize the same number of assets and labor while significantly increasing productivity.
运营影响
数量效益
相关案例.
.png)
Case Study
Improving Vending Machine Profitability with the Internet of Things (IoT)
The vending industry is undergoing a sea change, taking advantage of new technologies to go beyond just delivering snacks to creating a new retail location. Intelligent vending machines can be found in many public locations as well as company facilities, selling different types of goods and services, including even computer accessories, gold bars, tickets, and office supplies. With increasing sophistication, they may also provide time- and location-based data pertaining to sales, inventory, and customer preferences. But at the end of the day, vending machine operators know greater profitability is driven by higher sales and lower operating costs.
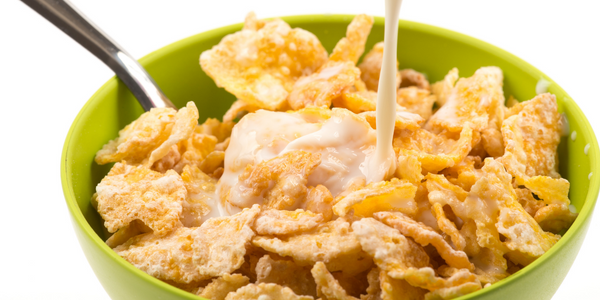
Case Study
The Kellogg Company
Kellogg keeps a close eye on its trade spend, analyzing large volumes of data and running complex simulations to predict which promotional activities will be the most effective. Kellogg needed to decrease the trade spend but its traditional relational database on premises could not keep up with the pace of demand.
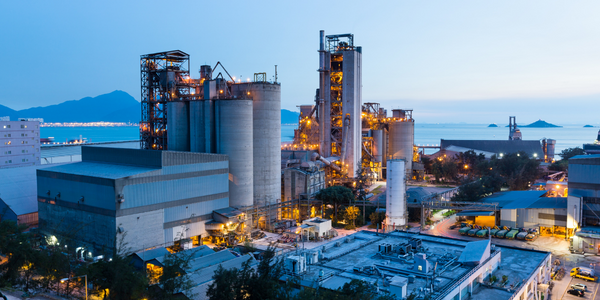
Case Study
Honeywell - Tata Chemicals Improves Data Accessibility with OneWireless
Tata was facing data accessibility challenges in the cement plant control room tapping signals from remote process control areas and other distant locations, including the gas scrubber. Tata needed a wireless solution to extend its control network securely to remote locations that would also provide seamless communication with existing control applications.
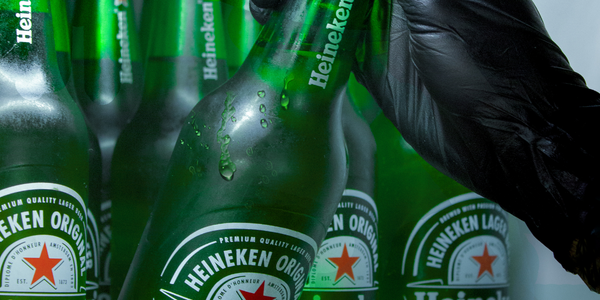
Case Study
HEINEKEN Uses the Cloud to Reach 10.5 Million Consumers
For 2012 campaign, the Bond promotion, it planned to launch the campaign at the same time everywhere on the planet. That created unprecedented challenges for HEINEKEN—nowhere more so than in its technology operation. The primary digital content for the campaign was a 100-megabyte movie that had to play flawlessly for millions of viewers worldwide. After all, Bond never fails. No one was going to tolerate a technology failure that might bruise his brand.Previously, HEINEKEN had supported digital media at its outsourced datacenter. But that datacenter lacked the computing resources HEINEKEN needed, and building them—especially to support peak traffic that would total millions of simultaneous hits—would have been both time-consuming and expensive. Nor would it have provided the geographic reach that HEINEKEN needed to minimize latency worldwide.
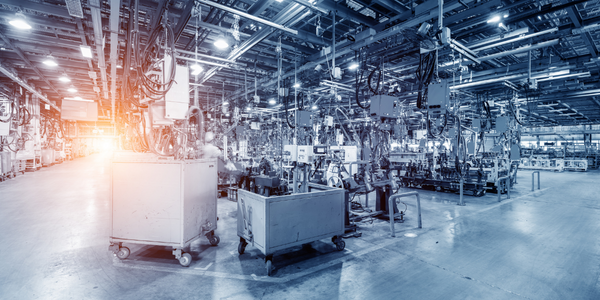
Case Study
Advanced Elastomer Systems Upgrades Production
In order to maintain its share of the international market for thermoplastic elastomers AES recently expanded its Florida plant by adding a new production line. While the existing lines were operating satisfactorily using a PROVOX distributed control system with traditional analog I/O, AES wanted advanced technology on the new line for greater economy, efficiency, and reliability. AES officials were anxious to get this line into production to meet incoming orders, but two hurricanes slowed construction.