下载PDF
Volvo Group’s Journey to Data Adoption and Collaboration with Qlik
技术
- 分析与建模 - 实时分析
适用行业
- 汽车
适用功能
- 商业运营
- 物流运输
用例
- 供应链可见性(SCV)
- 预测性维护
服务
- 数据科学服务
挑战
Volvo Group, a global manufacturer of trucks, buses, construction equipment, and marine applications, faced a significant challenge in managing its complex material flow. The company had to connect with the right suppliers for the right spare parts and find the most efficient way of getting the right parts to the right trucks at the right time. The company's existing tools, such as MS Excel, were inefficient and left a lot of room for error. The team spent an excessive amount of time gathering data and making it understandable and presentable. This inefficiency led to a culture where teams and individuals quickly became siloed, missing out on opportunities to improve workflows or identify suppliers whose products weren't up to standards.
关于客户
Volvo Group is a global manufacturer with a broad portfolio of products. The company is a household name with many different truck brands, such as Volvo Trucks, Renault Trucks, Mack Trucks, and UD Trucks. In addition to trucks, Volvo Group also manufactures buses, construction equipment, and laser machine engines for marine applications. The company has a couple of thousand suppliers and a couple of million trucks per week that need to be up and running. When their products experience breakdowns, Volvo Group has to get service parts out to them. The company's challenge lies in how to connect with the right suppliers for the right spare parts, and find the most efficient way of getting the right parts to the right trucks at the right time.
解决方案
Volvo Group started its data journey about four years ago when senior managers began using Qlik, a data analytics and visualization tool. They ran their own applications and experimented with the platform, leading by example and challenging others within the organization to upgrade their thinking and mindset around data gathering and transparency. QlikView and Qlik Sense, the two solutions most broadly used today, are flexible enough that each user can select the appropriate solution to solve their unique business challenges. Qlik makes it easier for users to obtain data, which gives the team the time and opportunity to engage with their colleagues about the data itself, increasing opportunities for collaboration. When users have a better understanding of what the data shows, they can communicate and exchange ideas with others, and as a result, they can make better business decisions.
运营影响
相关案例.
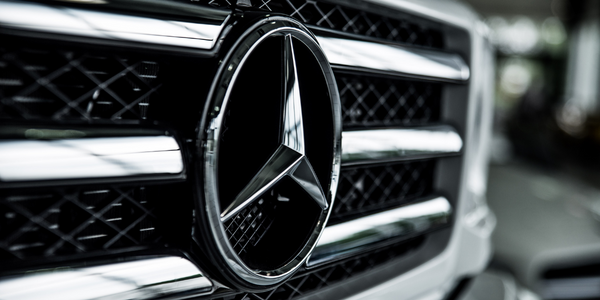
Case Study
Integral Plant Maintenance
Mercedes-Benz and his partner GAZ chose Siemens to be its maintenance partner at a new engine plant in Yaroslavl, Russia. The new plant offers a capacity to manufacture diesel engines for the Russian market, for locally produced Sprinter Classic. In addition to engines for the local market, the Yaroslavl plant will also produce spare parts. Mercedes-Benz Russia and his partner needed a service partner in order to ensure the operation of these lines in a maintenance partnership arrangement. The challenges included coordinating the entire maintenance management operation, in particular inspections, corrective and predictive maintenance activities, and the optimizing spare parts management. Siemens developed a customized maintenance solution that includes all electronic and mechanical maintenance activities (Integral Plant Maintenance).
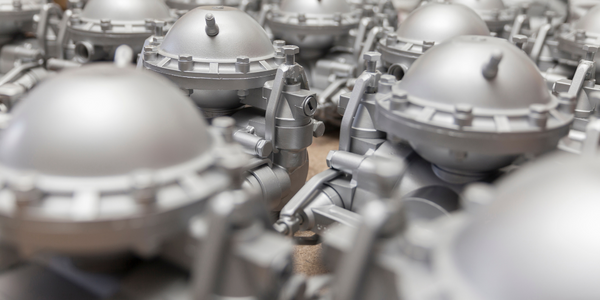
Case Study
Monitoring of Pressure Pumps in Automotive Industry
A large German/American producer of auto parts uses high-pressure pumps to deburr machined parts as a part of its production and quality check process. They decided to monitor these pumps to make sure they work properly and that they can see any indications leading to a potential failure before it affects their process.