Download PDF
Achieving Superior Crash Performance for the Soueast DX7 with IoT
Technology Category
- Analytics & Modeling - Digital Twin / Simulation
- Cybersecurity & Privacy - Intrusion Detection
Applicable Industries
- Automotive
- Packaging
Applicable Functions
- Product Research & Development
Use Cases
- Intrusion Detection Systems
- Virtual Prototyping & Product Testing
Services
- System Integration
- Testing & Certification
The Challenge
Soueast, a China-based automobile manufacturer, was faced with the challenge of optimizing the crash performance of its DX7 vehicle while reducing reliance on physical tests. Crash safety is a crucial part of the development process, and designing a car body that has good collision energy absorption performance is one of the main goals of automotive design. However, due to the high cost of prototype crash tests, it is not practical to validate a design’s feasibility through trial and error alone. The key to the success of virtual simulation is dependent on whether the simulation results are an accurate representation of the physical test results. The target for the DX7 project was to achieve the best possible crashworthiness while under tight time and budget constraints. The two main challenges were ensuring the CAE simulation results accurately reflect the physical crash test and analyzing and optimizing the restraint system.
About The Customer
Soueast is a China-based automobile manufacturer with a mission of “providing an exciting mobile lifestyle and cultivating a cultured automotive community.” After more than twenty years in business, Soueast has successfully integrated advanced technologies from internationally renowned companies - Chrysler and Mitsubishi, and established two of its brands, Soueast and Mitsubishi in China. Looking to the future, while continuing to partner with international companies, Soueast is dedicated to strengthening its own R&D capabilities and its product brand. The DX7 is Soueast’s drive into the competitive SUV market based on its 3.0 new product strategy. The DX7 features an exterior and interior designed by top Italian design company, Pininfarina, who have over 100 years of leading European concept automobile design, along with world quality and safety standards systems using Mitsubishi technology.
The Solution
To overcome these challenges, Soueast partnered with Altair’s engineering services division, Altair ProductDesign. The team utilized the HyperWorks suite and its RADIOSS solver to simulate and optimize the crash performance of the DX7 vehicle. This process involved analyzing the current structure and restraint system and suggesting potential enhancements to the design that could improve performance. A critical loadcase in the development of the body structure of the DX7 was the C-NCAP high speed 40% offset deformable barrier. Extensive optimization using HyperStudy was then performed for bumper beam, longitudinal rail, shotgun, kick-down, and sill design. Finally, the targets of acceleration and intrusion results could be achieved, and furthermore, the weight of the front body was reduced. Regarding development of the restraint systems, optimization was performed on the steering column crush, footrest design, seat design, seat belt force limiters, airbag size and the venting opening.
Operational Impact
Quantitative Benefit
Related Case Studies.
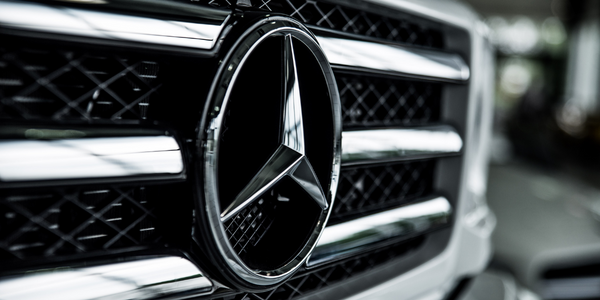
Case Study
Integral Plant Maintenance
Mercedes-Benz and his partner GAZ chose Siemens to be its maintenance partner at a new engine plant in Yaroslavl, Russia. The new plant offers a capacity to manufacture diesel engines for the Russian market, for locally produced Sprinter Classic. In addition to engines for the local market, the Yaroslavl plant will also produce spare parts. Mercedes-Benz Russia and his partner needed a service partner in order to ensure the operation of these lines in a maintenance partnership arrangement. The challenges included coordinating the entire maintenance management operation, in particular inspections, corrective and predictive maintenance activities, and the optimizing spare parts management. Siemens developed a customized maintenance solution that includes all electronic and mechanical maintenance activities (Integral Plant Maintenance).
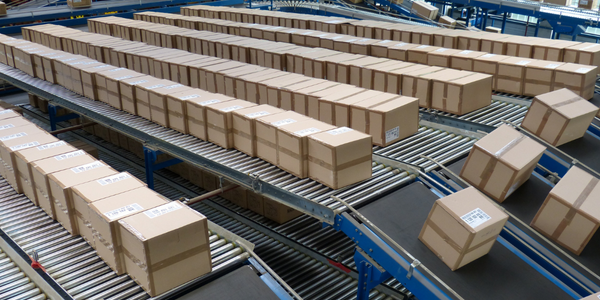
Case Study
IoT Data Analytics Case Study - Packaging Films Manufacturer
The company manufactures packaging films on made to order or configure to order basis. Every order has a different set of requirements from the product characteristics perspective and hence requires machine’s settings to be adjusted accordingly. If the film quality does not meet the required standards, the degraded quality impacts customer delivery causes customer dissatisfaction and results in lower margins. The biggest challenge was to identify the real root cause and devise a remedy for that.
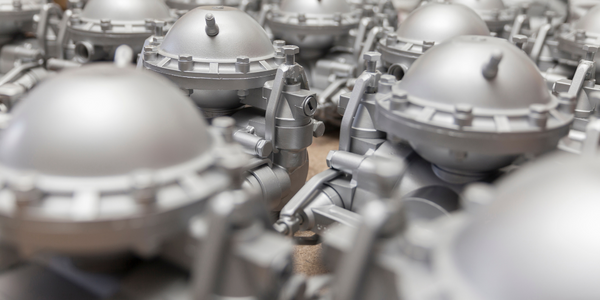
Case Study
Monitoring of Pressure Pumps in Automotive Industry
A large German/American producer of auto parts uses high-pressure pumps to deburr machined parts as a part of its production and quality check process. They decided to monitor these pumps to make sure they work properly and that they can see any indications leading to a potential failure before it affects their process.