Download PDF
Aerojet Rocketdyne’s 3D Printed Quad Thruster Enables Low-Cost Space Exploration
Technology Category
- Other - Additive Manufacturing
- Analytics & Modeling - Generative AI
Applicable Industries
- Aerospace
- Automotive
Applicable Functions
- Product Research & Development
Use Cases
- Rapid Prototyping
- Manufacturing Process Simulation
Services
- Software Design & Engineering Services
- System Integration
The Challenge
The engineering team at Aerojet Rocketdyne faced the challenge of redesigning legacy systems from the Apollo-era using modern propulsion, design, and manufacturing technologies. The goal was to drive down costs, speed up development time, improve performance, and make the production of over 600 thrusters economically sustainable for NASA’s Artemis program. The legacy Reaction Control System (RCS) consisted of four quad-thruster modules that controlled the spacecraft’s yaw, pitch, and roll. The initial design, 'Mark I,' was not optimized for weight, manufacturability, and cost, necessitating a more efficient solution.
About The Customer
Aerojet Rocketdyne is a world-class manufacturer of advanced energetic systems, playing a crucial role in the development of propulsion systems for NASA’s Artemis mission. The company is renowned for its expertise in creating high-performance propulsion systems for spacecraft and launch vehicles. With a history of involvement in significant space missions, Aerojet Rocketdyne is committed to leveraging modern technologies to enhance the performance and cost-effectiveness of its products. The company’s engineering team is focused on redesigning legacy systems to meet the demands of contemporary space exploration, particularly for the ambitious Artemis program, which aims to establish a permanent base camp on the moon and a station in lunar orbit.
The Solution
To address the challenges, Aerojet Rocketdyne engineers utilized additive manufacturing to optimize the RCS quad thruster. They consolidated the injector block into a single part, significantly reducing weight and production costs. For the second iteration, 'Mark II,' the team employed nTopology’s software to apply a lightweighting concept. They created a shell to remove unnecessary material and filled it with a lattice to ensure manufacturability and increase stiffness. This process, which was impossible with traditional CAD tools, took only a few hours in nTopology. The 'Mark II' injector block was manufactured in Titanium 6Al-4V, a material with half the density of Inconel 718 used in 'Mark I,' but more challenging to print. Velo3D’s system successfully produced the intricate geometry of the lattice and nozzle without failures, demonstrating the effectiveness of modern design and manufacturing technologies.
Operational Impact
Quantitative Benefit
Related Case Studies.
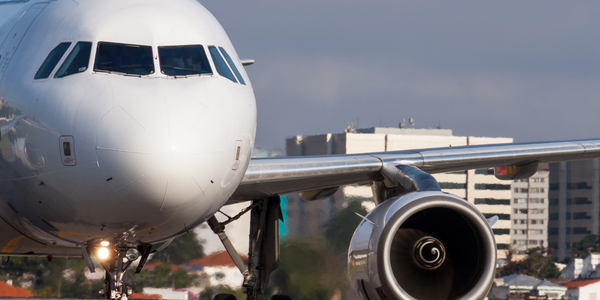
Case Study
Airbus Soars with Wearable Technology
Building an Airbus aircraft involves complex manufacturing processes consisting of thousands of moving parts. Speed and accuracy are critical to business and competitive advantage. Improvements in both would have high impact on Airbus’ bottom line. Airbus wanted to help operators reduce the complexity of assembling cabin seats and decrease the time required to complete this task.
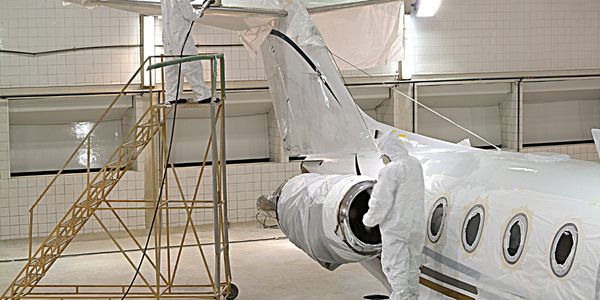
Case Study
Aircraft Predictive Maintenance and Workflow Optimization
First, aircraft manufacturer have trouble monitoring the health of aircraft systems with health prognostics and deliver predictive maintenance insights. Second, aircraft manufacturer wants a solution that can provide an in-context advisory and align job assignments to match technician experience and expertise.
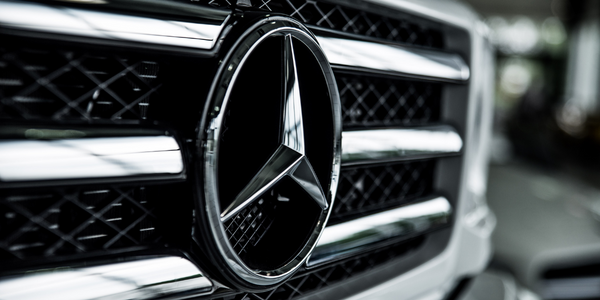
Case Study
Integral Plant Maintenance
Mercedes-Benz and his partner GAZ chose Siemens to be its maintenance partner at a new engine plant in Yaroslavl, Russia. The new plant offers a capacity to manufacture diesel engines for the Russian market, for locally produced Sprinter Classic. In addition to engines for the local market, the Yaroslavl plant will also produce spare parts. Mercedes-Benz Russia and his partner needed a service partner in order to ensure the operation of these lines in a maintenance partnership arrangement. The challenges included coordinating the entire maintenance management operation, in particular inspections, corrective and predictive maintenance activities, and the optimizing spare parts management. Siemens developed a customized maintenance solution that includes all electronic and mechanical maintenance activities (Integral Plant Maintenance).
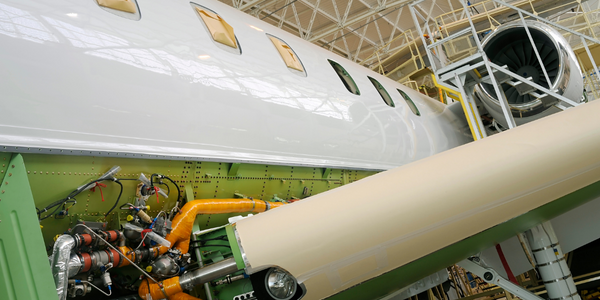
Case Study
Aerospace & Defense Case Study Airbus
For the development of its new wide-body aircraft, Airbus needed to ensure quality and consistency across all internal and external stakeholders. Airbus had many challenges including a very aggressive development schedule and the need to ramp up production quickly to satisfy their delivery commitments. The lack of communication extended design time and introduced errors that drove up costs.