Download PDF
AMETEK's IoT Solution for Cooling Joint Strike Fighter Pilots
Technology Category
- Other - Battery
- Processors & Edge Intelligence - Embedded & Edge Computers
Applicable Industries
- Aerospace
- Metals
Applicable Functions
- Product Research & Development
- Quality Assurance
Use Cases
- Real-Time Location System (RTLS)
- Track & Trace of Assets
Services
- Hardware Design & Engineering Services
- System Integration
The Challenge
AMETEK, a leading global manufacturer of electronic instruments and electromechanical devices, was contracted by Lockheed Martin to design a portable flight suit chiller unit for the Joint Strike Fighter (JSF) program. The chiller unit works with a pilot cooling vest to maintain a pilot’s deep body core temperature at ≤ 100.4° F (38° C). The JSF program aims to deliver affordable, next-generation striker aircraft weapon systems for the U.S. Navy, Air Force, Marines, and allies. Pilots flying these aircrafts are subject to high levels of acceleration – up to 9g – and must wear G-suits to prevent blackouts. To prevent pilots suffering from heat stress in the cockpit and on the ground, portable flight suit chiller units are needed. The design challenge was to monitor multiple variables and develop the code that goes to the controlling device to make those adjustments automatically. The chiller unit must also run within its power limits to prevent damage.
About The Customer
AMETEK, INC. is a leading global manufacturer of electronic instruments and electromechanical devices. With over 15,000 employees at more than 150 manufacturing locations around the world, AMETEK serves a variety of markets including Aerospace and Defense, Connectors, Metals and Engineered System & Materials, Electronic Instruments, Motors and Blowers, and Power. The company was contracted by Lockheed Martin to design a portable flight suit chiller unit for the Joint Strike Fighter (JSF) program, which aims to deliver affordable, next-generation striker aircraft weapon systems for the U.S. Navy, Air Force, Marines, and allies.
The Solution
AMETEK's team decided to follow a model-based development (MBD) approach, leveraging solidThinking Embed. Using solidThinking Embed, the team created a working model of the combined chiller unit and control system via a block diagram approach. They refined the plant model using measurements of plant responses in the lab. Then a multi-loop PID controller was built with interlock safety stages that stepped through the start-up and shutdown actions necessary to avoid damage to sensitive device components. After debugging and tuning the controller in offline Embed simulations, an ANSI C code from the controller model was created automatically. Then the code was compiled and downloaded directly to the Texas Instruments (TI) C2000 target chip, using a bi-directional Joint Test Action Group (JTAG) link. Engineers tested the control algorithm firmware running on the C2000. It resides in the Embed plant model running in real time on a PC, using JTAG technology to easily provide an interface between virtual plant outputs supplied to the firmware and firmware control outputs supplied back to the virtual plant model in Embed.
Operational Impact
Related Case Studies.
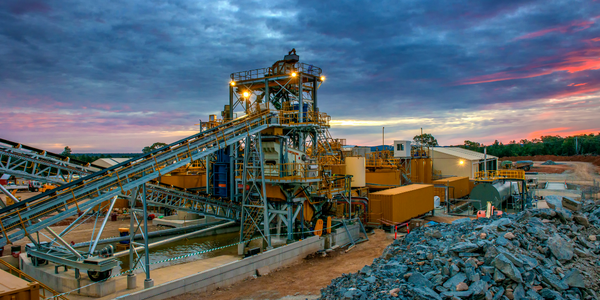
Case Study
Goldcorp: Internet of Things Enables the Mine of the Future
Goldcorp is committed to responsible mining practices and maintaining maximum safety for its workers. At the same time, the firm is constantly exploring ways to improve the efficiency of its operations, extend the life of its assets, and control costs. Goldcorp needed technology that can maximize production efficiency by tracking all mining operations, keep employees safe with remote operations and monitoring of hazardous work areas and control production costs through better asset and site management.
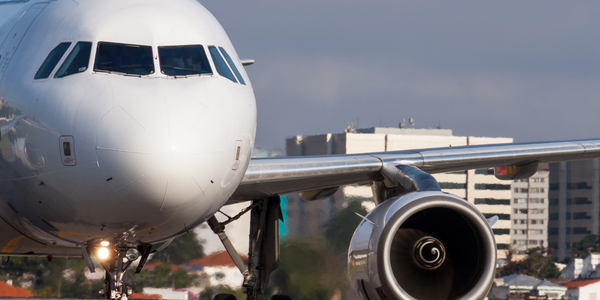
Case Study
Airbus Soars with Wearable Technology
Building an Airbus aircraft involves complex manufacturing processes consisting of thousands of moving parts. Speed and accuracy are critical to business and competitive advantage. Improvements in both would have high impact on Airbus’ bottom line. Airbus wanted to help operators reduce the complexity of assembling cabin seats and decrease the time required to complete this task.
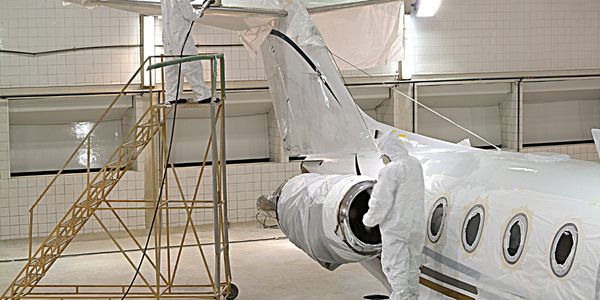
Case Study
Aircraft Predictive Maintenance and Workflow Optimization
First, aircraft manufacturer have trouble monitoring the health of aircraft systems with health prognostics and deliver predictive maintenance insights. Second, aircraft manufacturer wants a solution that can provide an in-context advisory and align job assignments to match technician experience and expertise.
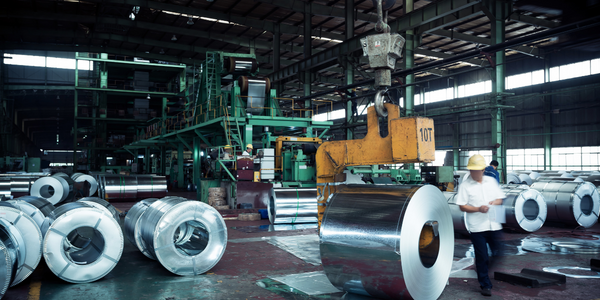
Case Study
KSP Steel Decentralized Control Room
While on-site in Pavlodar, Kazakhstan, the DAQRI team of Business Development and Solutions Architecture personnel worked closely with KSP Steel’s production leadership to understand the steel production process, operational challenges, and worker pain points.
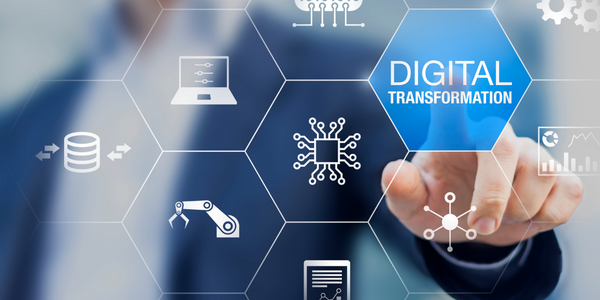
Case Study
Bluescope Steel on Path to Digitally Transform Operations and IT
Increasing competition and fluctuations in the construction market prompted BlueScope Steel to look toward digital transformation of its four businesses, including modern core applications and IT infrastructure. BlueScope needed to modernize its infrastructure and adopt new technologies to improve operations and supply chain efficiency while maintaining and updating an aging application portfolio.
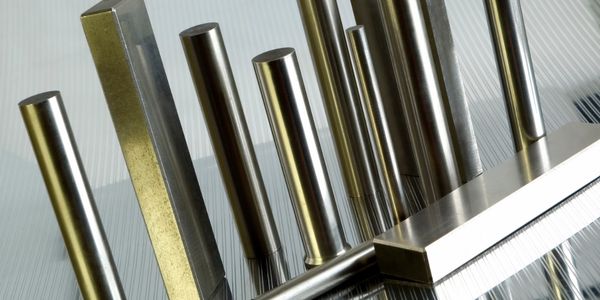
Case Study
RobotStudio Case Study: Benteler Automobiltechnik
Benteler has a small pipe business area for which they produce fuel lines and coolant lines made of aluminum for Porsche and other car manufacturers. One of the problems in production was that when Benteler added new products, production had too much downtime.