Download PDF
Apple Rubber Products, Inc. Case Study
Technology Category
- Functional Applications - Enterprise Resource Planning Systems (ERP)
- Platform as a Service (PaaS) - Data Management Platforms
Applicable Industries
- Aerospace
- Healthcare & Hospitals
Applicable Functions
- Quality Assurance
Services
- System Integration
The Challenge
Apple Rubber Products, Inc. is a manufacturer of rubber components for the medical device and aerospace industries. The company was facing challenges with its paper-based quality control program which involved multiple filing systems. Information was stored in various locations, leading to wasted hours keying duplicate data into different places, searching through file cabinets, and sending paper documents around to different buildings for approval. The company needed a centralized quality system to streamline its operations.
About The Customer
Apple Rubber Products, Inc. is a manufacturer of rubber components, such as o-rings and seals. The company serves the medical device and aerospace industries. As an AS9100C, ISO 9001 and RoHS compliant manufacturer with a Class 7 (10000) cleanroom, Apple Rubber understands the importance of quality control, full lot traceability, safety, and part reliability. The company's manufacturing facilities run on the ERP solution, DELMIAworks, a comprehensive software program that integrates every aspect of the business.
The Solution
Apple Rubber implemented DELMIAworks, a comprehensive ERP solution that integrates every aspect of the business, from ERP to MES, MRP, financials, order management, quality, WMS, CRM, and more, in one single database. With DELMIAworks, Apple Rubber was able to migrate all of its quality processes under one centralized system. The range of quality offerings is robust, allowing Apple Rubber to manage CARs, MRBs, document control, control plans, PPQ submissions, FMEA, gauge calibrations, and SPC analysis all in one place.
Operational Impact
Quantitative Benefit
Related Case Studies.
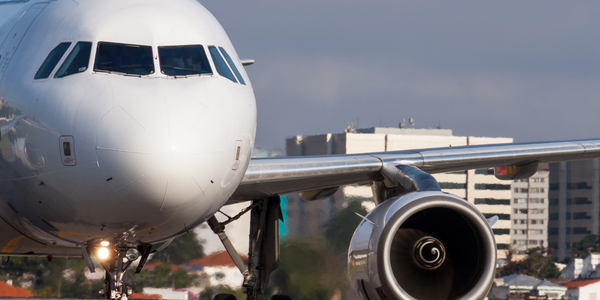
Case Study
Airbus Soars with Wearable Technology
Building an Airbus aircraft involves complex manufacturing processes consisting of thousands of moving parts. Speed and accuracy are critical to business and competitive advantage. Improvements in both would have high impact on Airbus’ bottom line. Airbus wanted to help operators reduce the complexity of assembling cabin seats and decrease the time required to complete this task.
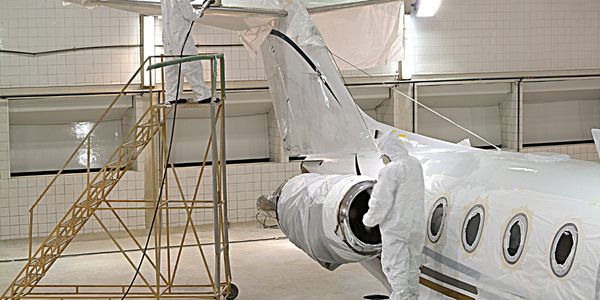
Case Study
Aircraft Predictive Maintenance and Workflow Optimization
First, aircraft manufacturer have trouble monitoring the health of aircraft systems with health prognostics and deliver predictive maintenance insights. Second, aircraft manufacturer wants a solution that can provide an in-context advisory and align job assignments to match technician experience and expertise.
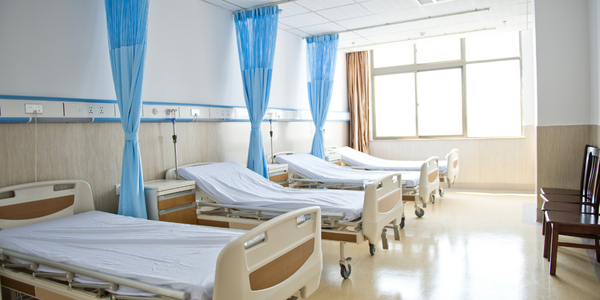
Case Study
Hospital Inventory Management
The hospital supply chain team is responsible for ensuring that the right medical supplies are readily available to clinicians when and where needed, and to do so in the most efficient manner possible. However, many of the systems and processes in use at the cancer center for supply chain management were not best suited to support these goals. Barcoding technology, a commonly used method for inventory management of medical supplies, is labor intensive, time consuming, does not provide real-time visibility into inventory levels and can be prone to error. Consequently, the lack of accurate and real-time visibility into inventory levels across multiple supply rooms in multiple hospital facilities creates additional inefficiency in the system causing over-ordering, hoarding, and wasted supplies. Other sources of waste and cost were also identified as candidates for improvement. Existing systems and processes did not provide adequate security for high-cost inventory within the hospital, which was another driver of cost. A lack of visibility into expiration dates for supplies resulted in supplies being wasted due to past expiry dates. Storage of supplies was also a key consideration given the location of the cancer center’s facilities in a dense urban setting, where space is always at a premium. In order to address the challenges outlined above, the hospital sought a solution that would provide real-time inventory information with high levels of accuracy, reduce the level of manual effort required and enable data driven decision making to ensure that the right supplies were readily available to clinicians in the right location at the right time.
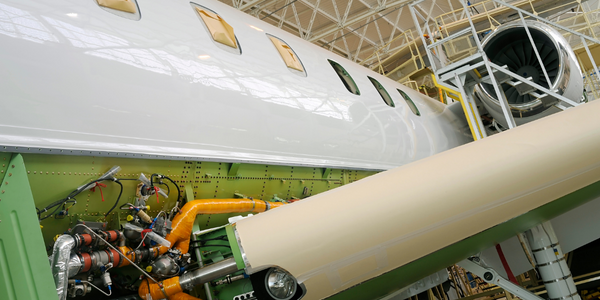
Case Study
Aerospace & Defense Case Study Airbus
For the development of its new wide-body aircraft, Airbus needed to ensure quality and consistency across all internal and external stakeholders. Airbus had many challenges including a very aggressive development schedule and the need to ramp up production quickly to satisfy their delivery commitments. The lack of communication extended design time and introduced errors that drove up costs.
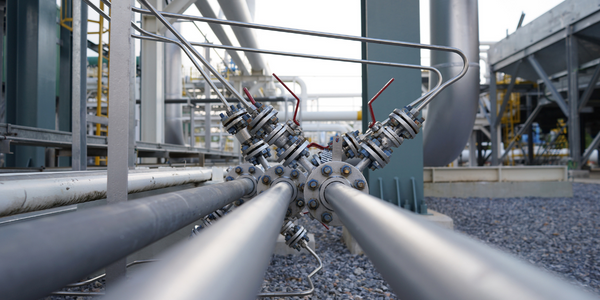
Case Study
Gas Pipeline Monitoring System for Hospitals
This system integrator focuses on providing centralized gas pipeline monitoring systems for hospitals. The service they provide makes it possible for hospitals to reduce both maintenance and labor costs. Since hospitals may not have an existing network suitable for this type of system, GPRS communication provides an easy and ready-to-use solution for remote, distributed monitoring systems System Requirements - GPRS communication - Seamless connection with SCADA software - Simple, front-end control capability - Expandable I/O channels - Combine AI, DI, and DO channels