Download PDF
Apply Sørco Achieves 30% Efficiency Gain Thanks to Enhanced Technology Adoption
Technology Category
- Platform as a Service (PaaS) - Application Development Platforms
Applicable Industries
- Oil & Gas
Applicable Functions
- Discrete Manufacturing
- Product Research & Development
Use Cases
- Manufacturing System Automation
- Digital Twin
Services
- Software Design & Engineering Services
The Challenge
Apply Sørco, a Norwegian engineering company, faced challenges in winning new contracts due to the existing time-consuming training process and the excessive amount of administrative work. Major clients demanded substantially lower costs, putting pressure on the company to reduce their prices and spend fewer man-hours per task. The company's major clients on the Norwegian continental shelf mandate their subcontractors to deliver data and information using AVEVA software, and the deliverables vary from client to client. The integration of these was not optimal, as it required numerous mouse-clicks, and the engineers had to switch between different software packages.
About The Customer
Apply Sørco is a leading international multi-discipline engineering company delivering services to the oil & gas industry, mainly on the Norwegian continental shelf. Headquartered in Stavanger, with offices in Bergen, Krakow and Hammerfest, Apply Sørco covers all project phases from concept development and studies to completion and commissioning, as well as operations, maintenance and modifications. In the last few years Apply Sørco has secured large maintenance, modification and operations contracts with the oil & gas companies Statoil, Eni and Lundin. The company was established in 1979.
The Solution
Apply Sørco decided to test AVEVA Everything3D on a small project to identify efficiency savings. The results provided the basis for Apply Sørco to start the migration process to AVEVA E3D, and implement new technology. The AVEVA E3D solution implemented at Apply Sørco consists of four modules: Design, Draw, Laser Scanning, and Supports. The efficiency savings were a driver for Apply Sørco to upgrade from PDMS to AVEVA E3D. The transition was also cost-efficient, since the total licensing for the AVEVA E3D package is slightly lower than the sum of licences in the PDMS system. The company started implementing it in early 2015. Apply Sørco was the first company in Norway to run AVEVA E3D.
Operational Impact
Quantitative Benefit
Related Case Studies.
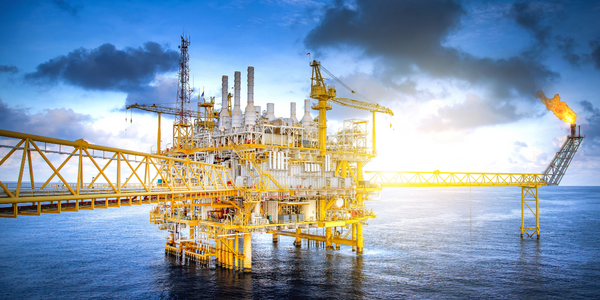
Case Study
Taking Oil and Gas Exploration to the Next Level
DownUnder GeoSolutions (DUG) wanted to increase computing performance by 5 to 10 times to improve seismic processing. The solution must build on current architecture software investments without sacrificing existing software and scale computing without scaling IT infrastructure costs.
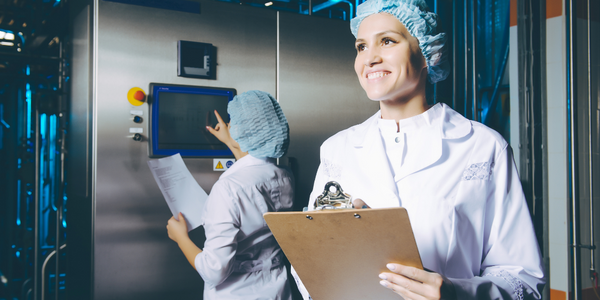
Case Study
Remote Wellhead Monitoring
Each wellhead was equipped with various sensors and meters that needed to be monitored and controlled from a central HMI, often miles away from the assets in the field. Redundant solar and wind generators were installed at each wellhead to support the electrical needs of the pumpstations, temperature meters, cameras, and cellular modules. In addition to asset management and remote control capabilities, data logging for remote surveillance and alarm notifications was a key demand from the customer. Terra Ferma’s solution needed to be power efficient, reliable, and capable of supporting high-bandwidth data-feeds. They needed a multi-link cellular connection to a central server that sustained reliable and redundant monitoring and control of flow meters, temperature sensors, power supply, and event-logging; including video and image files. This open-standard network needed to interface with the existing SCADA and proprietary network management software.
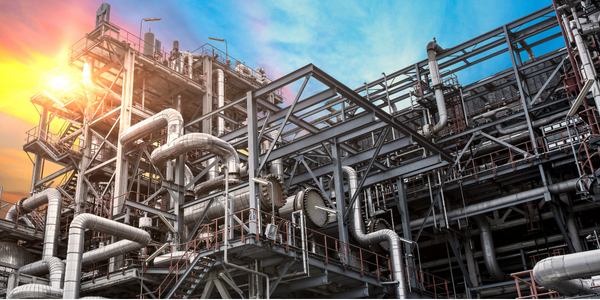
Case Study
Refinery Saves Over $700,000 with Smart Wireless
One of the largest petroleum refineries in the world is equipped to refine various types of crude oil and manufacture various grades of fuel from motor gasoline to Aviation Turbine Fuel. Due to wear and tear, eight hydrogen valves in each refinery were leaking, and each cost $1800 per ton of hydrogen vented. The plant also had leakage on nearly 30 flare control hydrocarbon valves. The refinery wanted a continuous, online monitoring system that could catch leaks early, minimize hydrogen and hydrocarbon production losses, and improve safety for maintenance.