Download PDF
Automating software delivery lifecycle with IBM Rational software cuts development costs 40 percent
Technology Category
- Application Infrastructure & Middleware - API Integration & Management
- Application Infrastructure & Middleware - Data Exchange & Integration
Applicable Industries
- Electronics
- Retail
Applicable Functions
- Product Research & Development
- Quality Assurance
Use Cases
- Process Control & Optimization
- Predictive Quality Analytics
Services
- Software Design & Engineering Services
- System Integration
The Challenge
The data capture device manufacturer was struggling with managing and automating the software development lifecycle for its mission-critical product portfolio. The development team was using email to manage change requests, which often led to lost requests and delays in addressing them. The lack of a collaborative design solution made it difficult for engineers to collaborate on design changes.
About The Customer
The company in focus is a manufacturer of advanced data capture devices, including bar code scanners and radio frequency identification (RFID) products. They also produce professional and commercial two-way radios and deliver unlicensed wireless broadband capabilities and wireless LANs (WLANs) to retail enterprises. The company's mission-critical product portfolio required a more efficient and automated software development lifecycle.
The Solution
The company adopted a suite of IBM Rational software to address its development challenges. This suite included IBM Rational ClearCase, IBM Rational ClearQuest, IBM Rational Rose RealTime, and IBM Rational Test RealTime software. The software helped the company's engineers better manage the software development lifecycle. For example, when an application needed updating or changing, engineers received a change request through Rational ClearQuest software. They used that change record to modify a Unified Modeling Language (UML) model with Rational Rose RealTime software. After completing the modifications, they used Rational Test RealTime software to validate that the changes met the quality requirements. Finally, engineers saved the changes in Rational ClearCase software, where they could distribute them for others to use.
Operational Impact
Quantitative Benefit
Related Case Studies.
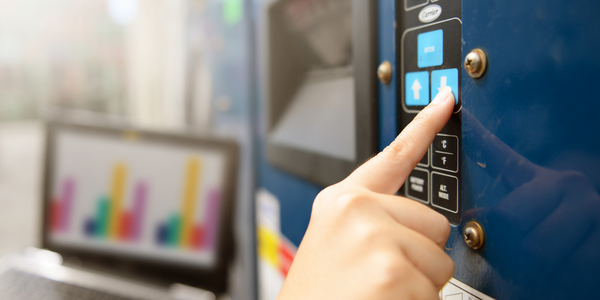
Case Study
Remote Temperature Monitoring of Perishable Goods Saves Money
RMONI was facing temperature monitoring challenges in a cold chain business. A cold chain must be established and maintained to ensure goods have been properly refrigerated during every step of the process, making temperature monitoring a critical business function. Manual registration practice can be very costly, labor intensive and prone to mistakes.
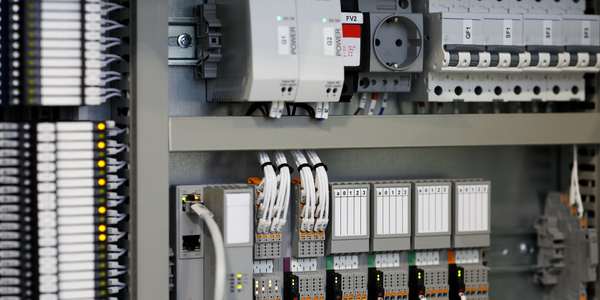
Case Study
Improving Production Line Efficiency with Ethernet Micro RTU Controller
Moxa was asked to provide a connectivity solution for one of the world's leading cosmetics companies. This multinational corporation, with retail presence in 130 countries, 23 global braches, and over 66,000 employees, sought to improve the efficiency of their production process by migrating from manual monitoring to an automatic productivity monitoring system. The production line was being monitored by ABB Real-TPI, a factory information system that offers data collection and analysis to improve plant efficiency. Due to software limitations, the customer needed an OPC server and a corresponding I/O solution to collect data from additional sensor devices for the Real-TPI system. The goal is to enable the factory information system to more thoroughly collect data from every corner of the production line. This will improve its ability to measure Overall Equipment Effectiveness (OEE) and translate into increased production efficiencies. System Requirements • Instant status updates while still consuming minimal bandwidth to relieve strain on limited factory networks • Interoperable with ABB Real-TPI • Small form factor appropriate for deployment where space is scarce • Remote software management and configuration to simplify operations
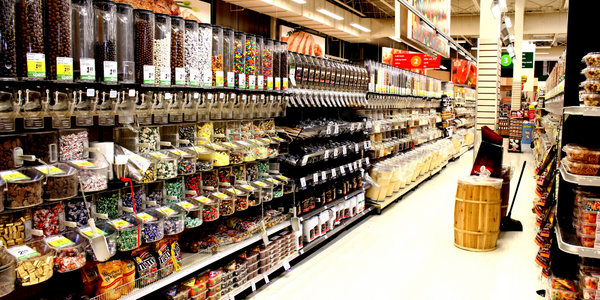
Case Study
How Sirqul’s IoT Platform is Crafting Carrefour’s New In-Store Experiences
Carrefour Taiwan’s goal is to be completely digital by end of 2018. Out-dated manual methods for analysis and assumptions limited Carrefour’s ability to change the customer experience and were void of real-time decision-making capabilities. Rather than relying solely on sales data, assumptions, and disparate systems, Carrefour Taiwan’s CEO led an initiative to find a connected IoT solution that could give the team the ability to make real-time changes and more informed decisions. Prior to implementing, Carrefour struggled to address their conversion rates and did not have the proper insights into the customer decision-making process nor how to make an immediate impact without losing customer confidence.
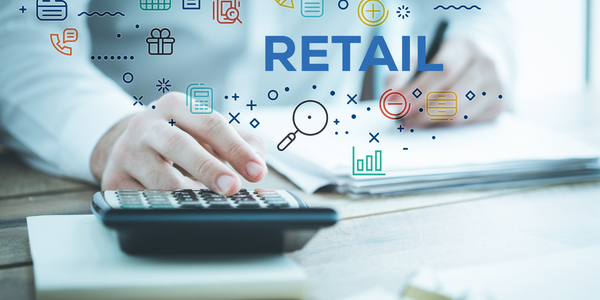
Case Study
Digital Retail Security Solutions
Sennco wanted to help its retail customers increase sales and profits by developing an innovative alarm system as opposed to conventional connected alarms that are permanently tethered to display products. These traditional security systems were cumbersome and intrusive to the customer shopping experience. Additionally, they provided no useful data or analytics.