Download PDF
Automating Vehicle Component Models for Enhanced Accuracy and Efficiency
Technology Category
- Robots - Autonomous Guided Vehicles (AGV)
Applicable Industries
- Automotive
- Buildings
Applicable Functions
- Product Research & Development
Use Cases
- Leasing Finance Automation
- Time Sensitive Networking
The Challenge
Changan Automobile, a leading Chinese automotive brand, was grappling with the time-consuming and error-prone process of pre-processing and setting up their vehicle components, specifically the twist beam. The need for the model to be as close to reality as possible for accurate results made the process extremely labor-intensive. This created a significant bottleneck in the development process, making it increasingly difficult for Changan to keep projects within the designated timeline. The challenge was to find a solution that could streamline this process, reduce errors, and improve efficiency.
About The Customer
Changan Automobile is a leading automotive brand in China with over 30 years of experience in building and selling passenger vehicles. The company's industrial leadership was established more than 150 years ago as China’s first western-style engineering firm. Today, Changan is among China’s top four automobile groups and maintains the title of the top-selling domestic Chinese automotive brand. The company, whose name means 'lasting safety' in Chinese, is committed to developing the safest vehicles possible. To this end, it employs CAE software to continually improve upon this mission.
The Solution
Changan turned to Altair, a provider of CAE software solutions, to address this challenge. Altair's Enterprise Solutions Group customized an existing packaged solution to suit Changan's specific needs, resulting in the Changan Chassis Structure Automation Tool. This tool guides users through the necessary process flow of pre-processing the model of the twist beam, automating repetitive tasks to save time. Users can now mesh the twist beam to achieve nearly the same level of detail seen in the actual component using HyperMesh, create welds based on analysis data, assign appropriate materials, and identify their contacts. The solution allows for accelerated model organization and rapid mesh generation. Once the model is set up, it can be imported into OptiStruct or any other solver to generate the desired results.
Operational Impact
Quantitative Benefit
Related Case Studies.
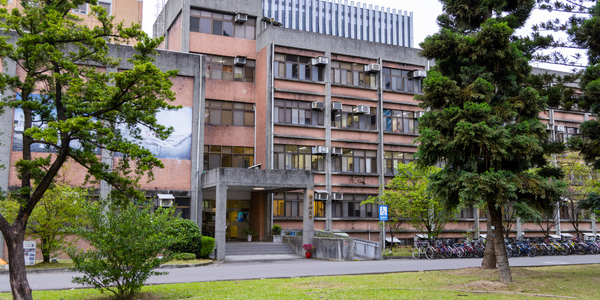
Case Study
Energy Saving & Power Monitoring System
Recently a university in Taiwan was experiencing dramatic power usage increases due to its growing number of campus buildings and students. Aiming to analyze their power consumption and increase their power efficiency across 52 buildings, the university wanted to build a power management system utilizing web-based hardware and software. With these goals in mind, they contacted Advantech to help them develop their system and provide them with the means to save energy in the years to come.
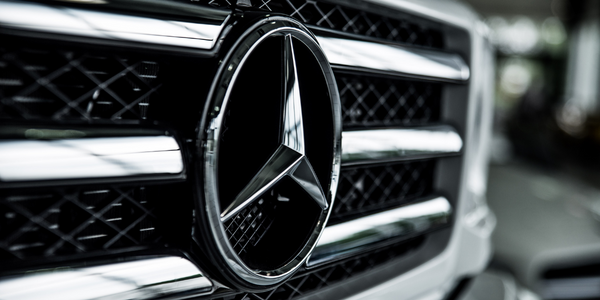
Case Study
Integral Plant Maintenance
Mercedes-Benz and his partner GAZ chose Siemens to be its maintenance partner at a new engine plant in Yaroslavl, Russia. The new plant offers a capacity to manufacture diesel engines for the Russian market, for locally produced Sprinter Classic. In addition to engines for the local market, the Yaroslavl plant will also produce spare parts. Mercedes-Benz Russia and his partner needed a service partner in order to ensure the operation of these lines in a maintenance partnership arrangement. The challenges included coordinating the entire maintenance management operation, in particular inspections, corrective and predictive maintenance activities, and the optimizing spare parts management. Siemens developed a customized maintenance solution that includes all electronic and mechanical maintenance activities (Integral Plant Maintenance).
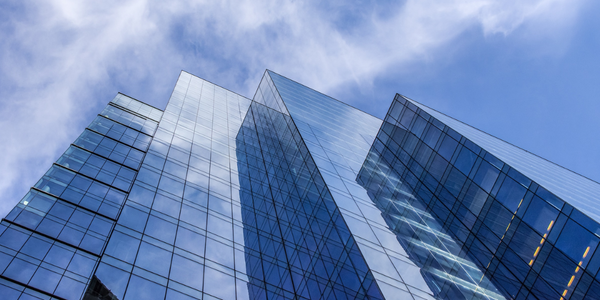
Case Study
Intelligent Building Automation System and Energy Saving Solution
One of the most difficult problems facing the world is conserving energy in buildings. However, it is not easy to have a cost-effective solution to reduce energy usage in a building. One solution for saving energy is to implement an intelligent building automation system (BAS) which can be controlled according to its schedule. In Indonesia a large university with a five floor building and 22 classrooms wanted to save the amount of energy being used.
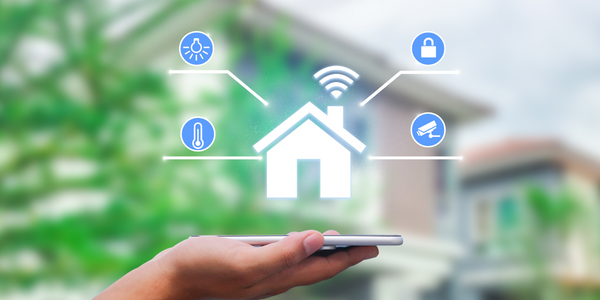
Case Study
Powering Smart Home Automation solutions with IoT for Energy conservation
Many industry leaders that offer Smart Energy Management products & solutions face challenges including:How to build a scalable platform that can automatically scale-up to on-board ‘n’ number of Smart home devicesData security, solution availability, and reliability are the other critical factors to deal withHow to create a robust common IoT platform that handles any kind of smart devicesHow to enable data management capabilities that would help in intelligent decision-making