Download PDF
Building Resiliency Into Disaster Recovery
Technology Category
- Infrastructure as a Service (IaaS) - Cloud Computing
Applicable Industries
- Aerospace
- Automotive
Applicable Functions
- Business Operation
- Discrete Manufacturing
Services
- Cloud Planning, Design & Implementation Services
The Challenge
Textron, a multi-industry company, needed to plan for disaster recovery and business continuity. The company needed to understand how much resiliency it needed for any business continuity or crisis scenario. This required engaging business leaders and asking tough questions about worst-case scenarios. The company needed to consider all aspects of recovery, beginning with a roadmap of critical assets and obscure dependencies. The company also needed to assess the hardware and software required to restore those applications and test recovery plans to validate that recovery goals could be met.
About The Customer
Textron is a multi-industry company headquartered in Providence, Rhode Island. The company is known for brands such as Beechcraft, Bell Helicopter, Cessna, E-Z-GO, and Jacobsen. The company operates in various industries, including aerospace and automotive. Textron is a large enterprise with a significant number of employees and a wide range of operations. The company has a diversified manufacturing enterprise with autonomous operating divisions.
The Solution
Textron partnered with IBM for resiliency planning to provide contingencies for a multitude of interruptions in business operations. The partnership with IBM gave Textron the flexibility to adjust resiliency strategies as business needs changed. Architectural alternatives included cloud, shared floor space, dedicated recovery techniques, and hybrid availability solutions. IBM provided replication on an enterprise-wide basis, offering geographic redundancy and resiliency to the local backups completed in each of Textron's business regions. If recovery were ever necessary, Textron could switch over to IBM hardware to run any part of its enterprise. Three times a year, the company did a practice run at IBM’s fully hardened recovery site in Boulder, Colorado.
Operational Impact
Related Case Studies.
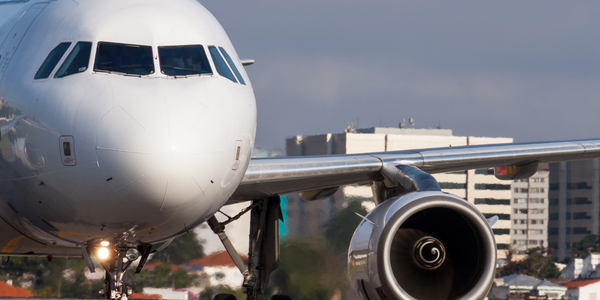
Case Study
Airbus Soars with Wearable Technology
Building an Airbus aircraft involves complex manufacturing processes consisting of thousands of moving parts. Speed and accuracy are critical to business and competitive advantage. Improvements in both would have high impact on Airbus’ bottom line. Airbus wanted to help operators reduce the complexity of assembling cabin seats and decrease the time required to complete this task.
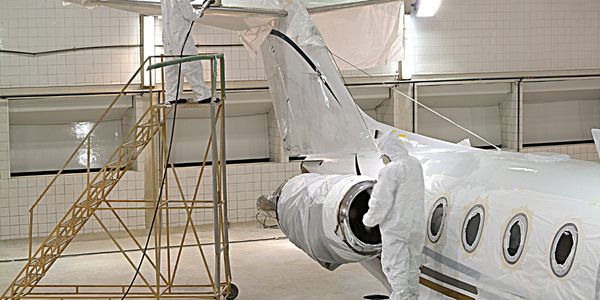
Case Study
Aircraft Predictive Maintenance and Workflow Optimization
First, aircraft manufacturer have trouble monitoring the health of aircraft systems with health prognostics and deliver predictive maintenance insights. Second, aircraft manufacturer wants a solution that can provide an in-context advisory and align job assignments to match technician experience and expertise.
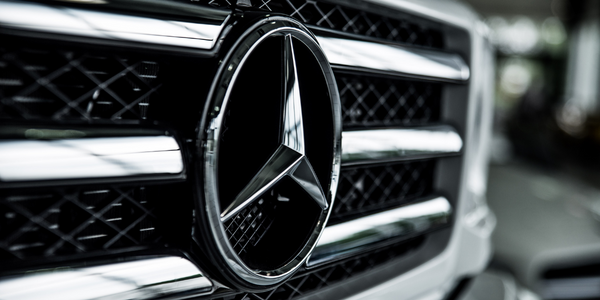
Case Study
Integral Plant Maintenance
Mercedes-Benz and his partner GAZ chose Siemens to be its maintenance partner at a new engine plant in Yaroslavl, Russia. The new plant offers a capacity to manufacture diesel engines for the Russian market, for locally produced Sprinter Classic. In addition to engines for the local market, the Yaroslavl plant will also produce spare parts. Mercedes-Benz Russia and his partner needed a service partner in order to ensure the operation of these lines in a maintenance partnership arrangement. The challenges included coordinating the entire maintenance management operation, in particular inspections, corrective and predictive maintenance activities, and the optimizing spare parts management. Siemens developed a customized maintenance solution that includes all electronic and mechanical maintenance activities (Integral Plant Maintenance).
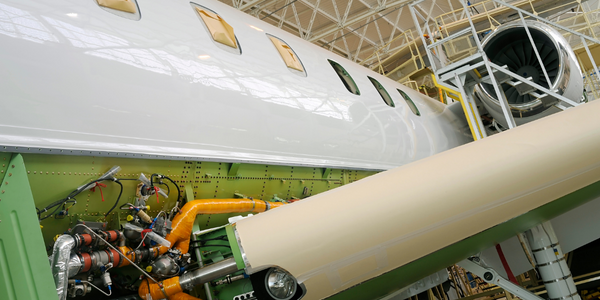
Case Study
Aerospace & Defense Case Study Airbus
For the development of its new wide-body aircraft, Airbus needed to ensure quality and consistency across all internal and external stakeholders. Airbus had many challenges including a very aggressive development schedule and the need to ramp up production quickly to satisfy their delivery commitments. The lack of communication extended design time and introduced errors that drove up costs.