Download PDF
Cenovus Brings New Approaches to Emissions and Energy Management Across 1,000 Facilities
Technology Category
- Platform as a Service (PaaS) - Data Management Platforms
Applicable Industries
- Oil & Gas
Applicable Functions
- Discrete Manufacturing
Use Cases
- Continuous Emission Monitoring Systems
- Energy Management System
Services
- Data Science Services
The Challenge
Cenovus Energy, a Canadian oil company, was facing the challenge of collecting, aggregating, and reporting emissions and energy consumption data across more than 1,000 facilities spread across a vast geographic area. The process was complex and difficult due to the use of numerous spreadsheets and systems to compile emissions data and reports. It was an onerous and labor-intensive process, involving collection and aggregation of data from multiple sources for a very large number of facilities. Much of the data would require additional pre-calculation or other conditioning to be suitable for emissions calculation and compliance report compilation. Cenovus envisioned a single, automated integrated enterprise-wide solution to manage air environmental reporting.
About The Customer
Cenovus Energy is a Canadian oil company that began independent operations in December 2009. The company is committed to using fresh, progressive thinking to safely and responsibly unlock energy resources the world needs. Its operations include oil sands projects in northern Alberta that use specialized methods to bring oil to the surface. It also owns established oil and natural gas properties in southern Alberta and Saskatchewan, as well as interests in two major U.S. refineries. Cenovus is demonstrating a commitment to innovation and responsibility while addressing the interrelated challenges of environmental compliance, greenhouse gas (GHG) emissions, and improving energy efficiency within its own operations.
The Solution
Cenovus implemented the Environmental Performance and Compliance Assurance Solutions, including Air & GHG Emissions and Compliance Assurance. The company transitioned to a self-contained, all-inclusive internal reporting system that provided a lot of detailed output with minimal effort on the data input task. The system used more science and fewer estimates, and received physical operating data directly from existing platforms wherever possible. All necessary calculations, such as fuel apportionment between multiple consumers from a single metered source, were totally accomplished within the system, and were based on traceable operational measurement. The company also used the enterprise-wide opsInfo platform to aggregate data from the bottom up, including public databases, data from internal measurement systems, and data from production accounting systems, and automatically integrated all of that data into a detailed emissions data set.
Operational Impact
Related Case Studies.
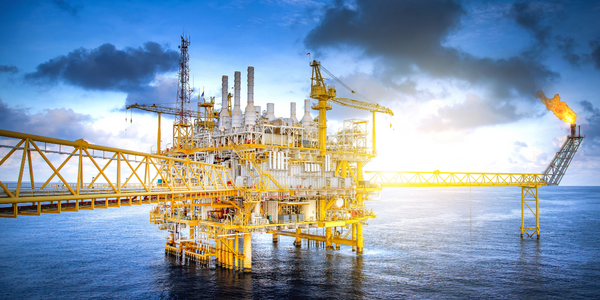
Case Study
Taking Oil and Gas Exploration to the Next Level
DownUnder GeoSolutions (DUG) wanted to increase computing performance by 5 to 10 times to improve seismic processing. The solution must build on current architecture software investments without sacrificing existing software and scale computing without scaling IT infrastructure costs.
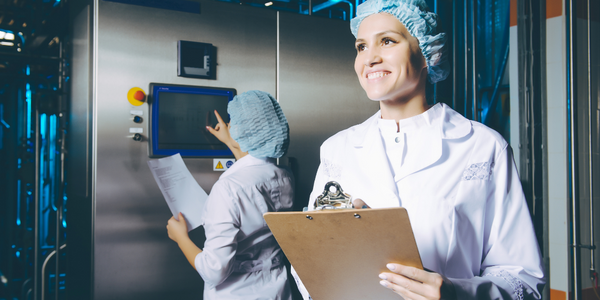
Case Study
Remote Wellhead Monitoring
Each wellhead was equipped with various sensors and meters that needed to be monitored and controlled from a central HMI, often miles away from the assets in the field. Redundant solar and wind generators were installed at each wellhead to support the electrical needs of the pumpstations, temperature meters, cameras, and cellular modules. In addition to asset management and remote control capabilities, data logging for remote surveillance and alarm notifications was a key demand from the customer. Terra Ferma’s solution needed to be power efficient, reliable, and capable of supporting high-bandwidth data-feeds. They needed a multi-link cellular connection to a central server that sustained reliable and redundant monitoring and control of flow meters, temperature sensors, power supply, and event-logging; including video and image files. This open-standard network needed to interface with the existing SCADA and proprietary network management software.
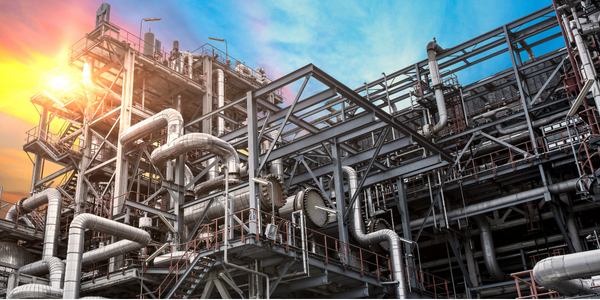
Case Study
Refinery Saves Over $700,000 with Smart Wireless
One of the largest petroleum refineries in the world is equipped to refine various types of crude oil and manufacture various grades of fuel from motor gasoline to Aviation Turbine Fuel. Due to wear and tear, eight hydrogen valves in each refinery were leaking, and each cost $1800 per ton of hydrogen vented. The plant also had leakage on nearly 30 flare control hydrocarbon valves. The refinery wanted a continuous, online monitoring system that could catch leaks early, minimize hydrogen and hydrocarbon production losses, and improve safety for maintenance.