Download PDF
CFD Advances Racing Bike Performance: A Case Study
Technology Category
- Application Infrastructure & Middleware - Data Visualization
- Sensors - Optical Sensors
Applicable Industries
- Aerospace
- Automotive
Applicable Functions
- Product Research & Development
- Quality Assurance
Use Cases
- Intelligent Packaging
- Smart Lighting
Services
- Testing & Certification
The Challenge
In the competitive world of bicycle racing, the design and aerodynamics of the bike play a crucial role in a cyclist's performance. Manufacturers constantly strive to reduce the weight and aerodynamic drag of bikes by experimenting with different materials and shapes for the frames, wheels, and tires. However, evaluating the drag force at the system level and isolating the impact of hundreds of design variables at the component level has been a challenge. Traditional methods like wind tunnel testing are expensive, and computational fluid dynamics (CFD) analysis workflows have been too lengthy to be practical. The challenge was to develop a highly automated, repeatable workflow methodology to accelerate the entire CFD process and provide new insights into the role various components play in bike performance.
About The Customer
The customer in this case study is Zipp Speed Weaponry, an Indianapolis-based manufacturer of advanced bicycle racing wheels and cycling components. After reading the research papers presented at the American Institute of Aeronautics and Astronautics (AIAA) conference, Zipp was inspired to apply CFD technology in the design of its Firecrest line of racing wheels. The company was particularly interested in the findings that challenged conventional wisdom about the factors influencing drag force on a bike. The insights from the study helped Zipp to re-characterize their approach to designing wheels, with a focus on balancing the competing requirements for speed and stability.
The Solution
Technologists developed a highly automated, repeatable workflow methodology to accelerate the CFD process. They used various simulation tools including Altair’s AcuSolve, a finite-element based, general-purpose solver, and Intelligent Light’s FieldView 13 CFD post-processing and visualization package. The team studied the aerodynamic flow around a rotating bike wheel and components, evaluating multiple wheel and fork/frame combinations at 10 yaw angles. The steady-state simulations generated approximately 3.6 GBs of AcuSolve data while the unsteady simulations resulted in nearly 1.2 TBs of data. The use of FieldView provided the team with the tools needed to accelerate the analysis, mine the most valuable information, and create compelling images and animations. The team also leveraged the FieldView FVX programming language to automate many post-processing tasks, significantly reducing the time required for iterations.
Operational Impact
Quantitative Benefit
Related Case Studies.
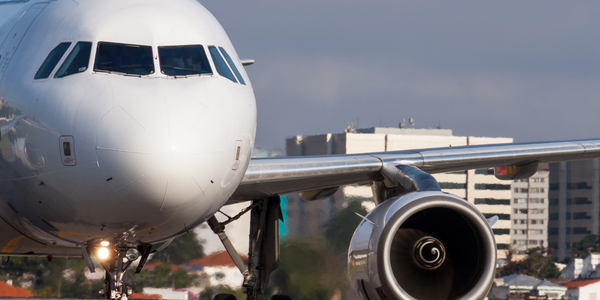
Case Study
Airbus Soars with Wearable Technology
Building an Airbus aircraft involves complex manufacturing processes consisting of thousands of moving parts. Speed and accuracy are critical to business and competitive advantage. Improvements in both would have high impact on Airbus’ bottom line. Airbus wanted to help operators reduce the complexity of assembling cabin seats and decrease the time required to complete this task.
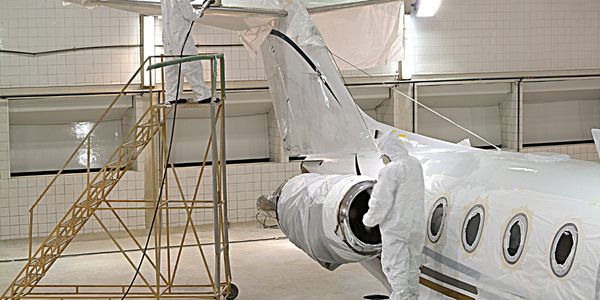
Case Study
Aircraft Predictive Maintenance and Workflow Optimization
First, aircraft manufacturer have trouble monitoring the health of aircraft systems with health prognostics and deliver predictive maintenance insights. Second, aircraft manufacturer wants a solution that can provide an in-context advisory and align job assignments to match technician experience and expertise.
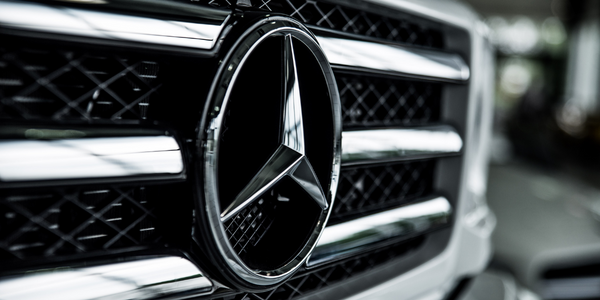
Case Study
Integral Plant Maintenance
Mercedes-Benz and his partner GAZ chose Siemens to be its maintenance partner at a new engine plant in Yaroslavl, Russia. The new plant offers a capacity to manufacture diesel engines for the Russian market, for locally produced Sprinter Classic. In addition to engines for the local market, the Yaroslavl plant will also produce spare parts. Mercedes-Benz Russia and his partner needed a service partner in order to ensure the operation of these lines in a maintenance partnership arrangement. The challenges included coordinating the entire maintenance management operation, in particular inspections, corrective and predictive maintenance activities, and the optimizing spare parts management. Siemens developed a customized maintenance solution that includes all electronic and mechanical maintenance activities (Integral Plant Maintenance).
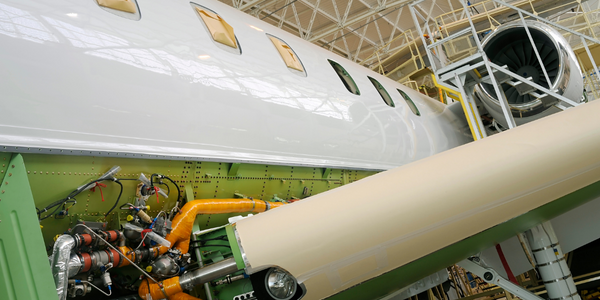
Case Study
Aerospace & Defense Case Study Airbus
For the development of its new wide-body aircraft, Airbus needed to ensure quality and consistency across all internal and external stakeholders. Airbus had many challenges including a very aggressive development schedule and the need to ramp up production quickly to satisfy their delivery commitments. The lack of communication extended design time and introduced errors that drove up costs.