Download PDF
Data is the New Oil, and This Enterprise Keeps its Competitive Edge by Protecting Both with Forcepoint
Technology Category
- Cybersecurity & Privacy - Database Security
Applicable Industries
- Oil & Gas
Applicable Functions
- Discrete Manufacturing
- Quality Assurance
Use Cases
- Cybersecurity
- Asset Health Management (AHM)
Services
- Cybersecurity Services
- Data Science Services
The Challenge
The company, a Fortune U.S. 50 enterprise oil and gas company, was facing a significant challenge in securing its critical proprietary data from people-based vulnerabilities. The company's task force identified that the biggest risk was employees leaving the company, who could potentially exfiltrate proprietary information. The company was aware of data leaks but lacked the ability to understand if they were accidental or malicious. The company needed a solution that could provide irrefutable evidence in case of litigation and help them get ahead of potential leaks.
About The Customer
The customer is a Fortune U.S. 50 enterprise oil and gas company engaged in the industry at every level from production to retail. The company is deeply engaged in every aspect of oil, natural gas, and geothermal energy. The company relies on a staggering amount of critical proprietary data. A leak of this enterprise’s most critical information, including invaluable geographical data and retail market pricing strategies, could directly undermine its competitive position, revenue, and market share for years to come.
The Solution
The company deployed Forcepoint Insider Threat (FIT) to gain visibility into employee interactions with sensitive data and provide detailed reporting and video playback to capture context and intent. FIT provides complete visibility into user behavior at the endpoint, including monitoring of communications channels, to help identify potential flight risks or disgruntled workers. It also provides visibility into user attempts to change file names, screen-capture sensitive documents, and attempt system process changes while offline. The solution also met the organization’s investigative needs with detailed forensics like timelines, live video capture, and replay of individual user actions. The company is also undertaking a proof of concept for Forcepoint Data Loss Prevention and Behavioral Analytics.
Operational Impact
Quantitative Benefit
Related Case Studies.
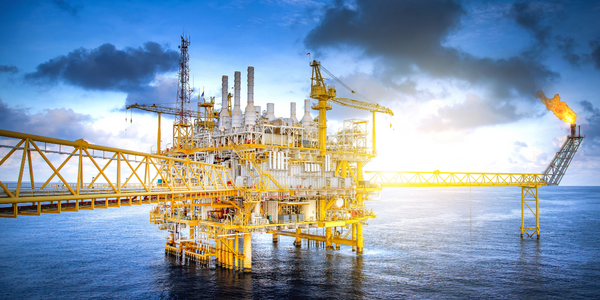
Case Study
Taking Oil and Gas Exploration to the Next Level
DownUnder GeoSolutions (DUG) wanted to increase computing performance by 5 to 10 times to improve seismic processing. The solution must build on current architecture software investments without sacrificing existing software and scale computing without scaling IT infrastructure costs.
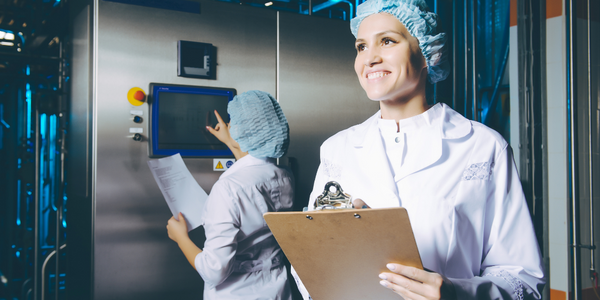
Case Study
Remote Wellhead Monitoring
Each wellhead was equipped with various sensors and meters that needed to be monitored and controlled from a central HMI, often miles away from the assets in the field. Redundant solar and wind generators were installed at each wellhead to support the electrical needs of the pumpstations, temperature meters, cameras, and cellular modules. In addition to asset management and remote control capabilities, data logging for remote surveillance and alarm notifications was a key demand from the customer. Terra Ferma’s solution needed to be power efficient, reliable, and capable of supporting high-bandwidth data-feeds. They needed a multi-link cellular connection to a central server that sustained reliable and redundant monitoring and control of flow meters, temperature sensors, power supply, and event-logging; including video and image files. This open-standard network needed to interface with the existing SCADA and proprietary network management software.
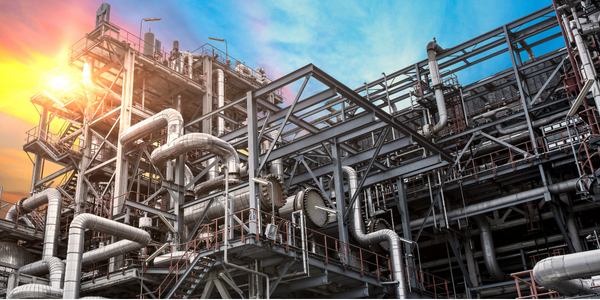
Case Study
Refinery Saves Over $700,000 with Smart Wireless
One of the largest petroleum refineries in the world is equipped to refine various types of crude oil and manufacture various grades of fuel from motor gasoline to Aviation Turbine Fuel. Due to wear and tear, eight hydrogen valves in each refinery were leaking, and each cost $1800 per ton of hydrogen vented. The plant also had leakage on nearly 30 flare control hydrocarbon valves. The refinery wanted a continuous, online monitoring system that could catch leaks early, minimize hydrogen and hydrocarbon production losses, and improve safety for maintenance.