Download PDF
Driving Energy Efficiency: TUfast Eco Team's Success with HyperWorks
Technology Category
- Analytics & Modeling - Digital Twin / Simulation
- Robots - Autonomous Guided Vehicles (AGV)
Applicable Industries
- Automotive
- Life Sciences
Applicable Functions
- Product Research & Development
Use Cases
- Transportation Simulation
- Vehicle Performance Monitoring
Services
- System Integration
- Training
The Challenge
The TUfast Eco team from the Technical University Munich, consisting of about 30 students from various fields of study, was tasked with designing, developing, and manufacturing an energy-efficient vehicle to compete in various energy-efficiency contests, including the Shell Eco-marathon. The challenge was to create an entirely new vehicle each year, with no component of the previous year's vehicle allowed to be used. This was to ensure that the technical expertise and development approaches of previous years were passed on to the new team. One of the most important aspects in the development of an energy-efficient vehicle was to reduce the mass of the vehicle. Therefore, the team members were constantly looking for weight-saving potentials, especially when designing the suspension and chassis.
About The Customer
The TUfast Eco team is a group of about 30 highly motivated students from the Technical University Munich. The team is divided into one administrative and three technical groups – chassis, suspension and powertrain. The students design and develop all vehicle components and assemblies, which are then manufactured in the team’s workshop or in cooperation with external partners. The team has been one of the most successful teams in the Shell Eco-marathon, an international contest for sustainable mobility, where student teams from schools and universities all over the world design vehicles that are as energy-efficient as possible.
The Solution
The TUfast Eco team used Altair Engineering’s HyperWorks software suite to develop, analyze and optimize the vehicle's components prior to production. Almost every part of each vehicle of the TUfast Eco team’s eLi series was designed, simulated and optimized with CAE software prior to production. The team employed the tools of the HyperWorks suite, including HyperMesh for geometry creation and meshing, OptiStruct as their FEA solver and optimization tool, and HyperView for post-processing tasks. The team used simulation to investigate how the plies of the vehicle could be positioned best to fully benefit from the chosen material, carbon (CFRP). To optimize the composite material and components, the students applied a three-step optimization approach, developed by Altair especially for the design and optimization of composite materials.
Operational Impact
Quantitative Benefit
Related Case Studies.
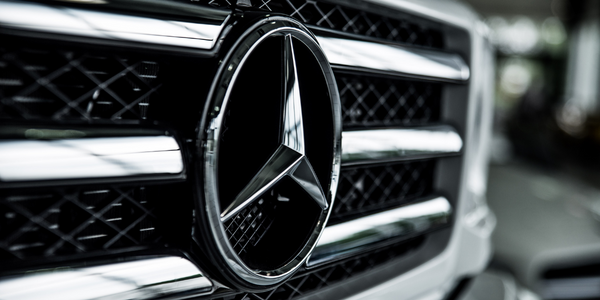
Case Study
Integral Plant Maintenance
Mercedes-Benz and his partner GAZ chose Siemens to be its maintenance partner at a new engine plant in Yaroslavl, Russia. The new plant offers a capacity to manufacture diesel engines for the Russian market, for locally produced Sprinter Classic. In addition to engines for the local market, the Yaroslavl plant will also produce spare parts. Mercedes-Benz Russia and his partner needed a service partner in order to ensure the operation of these lines in a maintenance partnership arrangement. The challenges included coordinating the entire maintenance management operation, in particular inspections, corrective and predictive maintenance activities, and the optimizing spare parts management. Siemens developed a customized maintenance solution that includes all electronic and mechanical maintenance activities (Integral Plant Maintenance).
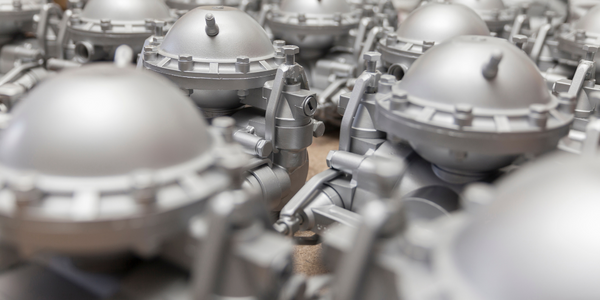
Case Study
Monitoring of Pressure Pumps in Automotive Industry
A large German/American producer of auto parts uses high-pressure pumps to deburr machined parts as a part of its production and quality check process. They decided to monitor these pumps to make sure they work properly and that they can see any indications leading to a potential failure before it affects their process.