Download PDF
DS PLM SUCCESS STORY Clip-Lok International Ltd. Danish box maker packs a punch with CATIA PLM Express
Technology Category
- Functional Applications - Product Lifecycle Management Systems (PLM)
Applicable Industries
- Automotive
- Aerospace
Applicable Functions
- Product Research & Development
- Logistics & Transportation
Use Cases
- Digital Twin
- Virtual Prototyping & Product Testing
Services
- Software Design & Engineering Services
- System Integration
The Challenge
Clip-Lok International, a Copenhagen-based manufacturer of reusable, flat-packable wooden boxes, needed to secure its competitive edge by custom designing boxes that are cost effective, match the precise size and shape of their contents, and can be flattened for return shipment. The boxes are custom-made, posing many design challenges for the engineers. They had to design a box that has the optimum shape and size with respect to the products to be packaged, that is cost efficient to produce, assemble and flatten and that occupies as little space as possible during return shipment. These design challenges were met thanks to CATIA PLM Express.
About The Customer
Clip-Lok International is a Copenhagen-based manufacturer with offices in over 14 countries. They produce innovative, cost-effective, environmentally friendly Clip-Lok boxes. These boxes are reusable flat-packable wooden boxes for companies that need to ship their products over any distance. Sturdy, Clip-Lok boxes can be reused on the average 100 times. Companies build the boxes through an ingenious system of clip “locks” and hinges, pack their products in the boxes and ship them to their destination. Once unpacked, the boxes can then be flattened, or flat-packed, loaded onto a truck, plane or any other transportation vehicle and shipped back to their point of origin for reuse. The majority of Clip-Lok's customers work in automotive, aerospace or defense industries.
The Solution
Clip-Lok upgraded its existing CATIA solution to CATIA PLM Express because it needed a more complete all-in-one solution for design and data management, as well as the ability to integrate STEP files into the CATIA environment. Many of Clip-Lok’s customers provide digital files in STEP, IGES, or native CATIA data. Its designers then use CATIA to design the box. Clip-Lok sales representatives present the resulting digital 3D model to the customer as a first design proposal. Once approved, drawings of the prototype are automatically generated in CATIA from the 3D model and the physical prototype of the box is produced. The customer can then test it in real life before ordering the box in series.
Operational Impact
Quantitative Benefit
Related Case Studies.
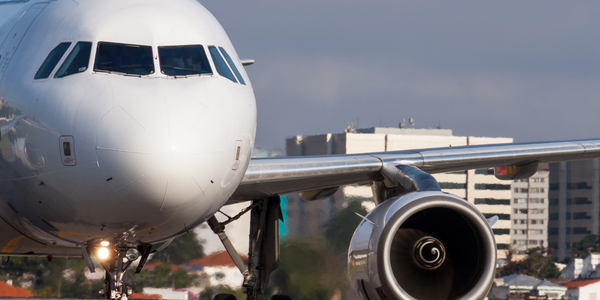
Case Study
Airbus Soars with Wearable Technology
Building an Airbus aircraft involves complex manufacturing processes consisting of thousands of moving parts. Speed and accuracy are critical to business and competitive advantage. Improvements in both would have high impact on Airbus’ bottom line. Airbus wanted to help operators reduce the complexity of assembling cabin seats and decrease the time required to complete this task.
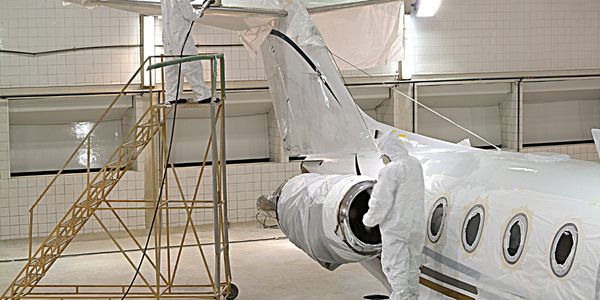
Case Study
Aircraft Predictive Maintenance and Workflow Optimization
First, aircraft manufacturer have trouble monitoring the health of aircraft systems with health prognostics and deliver predictive maintenance insights. Second, aircraft manufacturer wants a solution that can provide an in-context advisory and align job assignments to match technician experience and expertise.
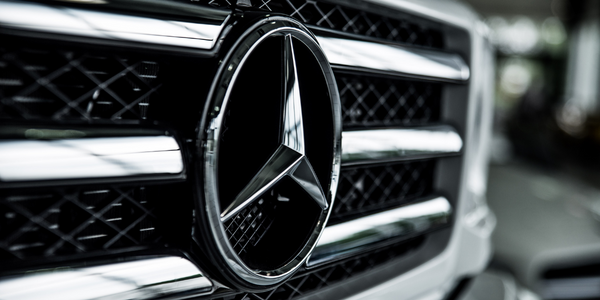
Case Study
Integral Plant Maintenance
Mercedes-Benz and his partner GAZ chose Siemens to be its maintenance partner at a new engine plant in Yaroslavl, Russia. The new plant offers a capacity to manufacture diesel engines for the Russian market, for locally produced Sprinter Classic. In addition to engines for the local market, the Yaroslavl plant will also produce spare parts. Mercedes-Benz Russia and his partner needed a service partner in order to ensure the operation of these lines in a maintenance partnership arrangement. The challenges included coordinating the entire maintenance management operation, in particular inspections, corrective and predictive maintenance activities, and the optimizing spare parts management. Siemens developed a customized maintenance solution that includes all electronic and mechanical maintenance activities (Integral Plant Maintenance).
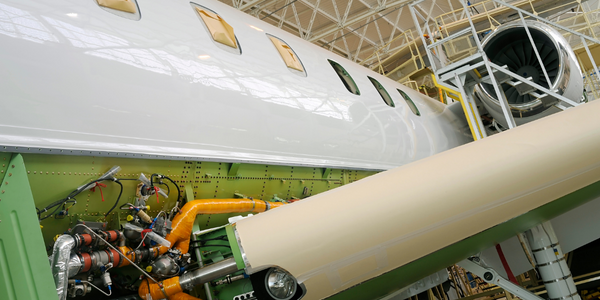
Case Study
Aerospace & Defense Case Study Airbus
For the development of its new wide-body aircraft, Airbus needed to ensure quality and consistency across all internal and external stakeholders. Airbus had many challenges including a very aggressive development schedule and the need to ramp up production quickly to satisfy their delivery commitments. The lack of communication extended design time and introduced errors that drove up costs.