Download PDF
Earth Signal: Helping clients strike oil with ultra-fast, ultra-dense computing
Technology Category
- Infrastructure as a Service (IaaS) - Cloud Computing
Applicable Industries
- Oil & Gas
Applicable Functions
- Discrete Manufacturing
Use Cases
- Predictive Maintenance
Services
- System Integration
The Challenge
Earth Signal Processing, a global leader in seismic data processing, was facing a challenge. Their clients in the oil and gas industry needed the results of their 2D and 3D seismic programs as quickly as possible to make informed decisions about land purchases and drilling locations. However, Earth Signal was constrained by the physical limits of its data center in terms of floor space and rack space. They needed to increase their data-crunching capabilities to meet the demands of their clients. The company was also under pressure to keep costs low, which meant they needed to find a solution that could maximize core and thread count within their existing infrastructure.
About The Customer
Earth Signal Processing is a global leader in seismic data processing. Founded in 1993, the company helps clients in the oil and gas industry to process their data faster and in greater detail to find new opportunities for profit. The company specializes in interpreting seismic data to construct models of what lies underground. All but the largest exploration firms engage partners like Earth Signal to perform 2D and 3D seismic programs and to process the results into a form their geologists can interpret. The company is based in Calgary and is known for its highly optimized Linux-based software.
The Solution
Earth Signal decided to deploy IBM Power Systems S822L servers with IBM POWER8 CPUs running Linux. This solution allowed them to maximize core and thread count within the physical limits of their data center. The company also ran tests which showed that the 2U IBM Power Systems solution could complete a job in 60 hours versus 100 hours for a 21U Xeon processor-based option, and using just 40 percent of the electrical energy. Earth Signal is now deploying a further two Power Systems S822L servers running Red Hat Enterprise Linux, each also with two 12-core POWER8 processors running at 3.01 GHz and offering up to eight threads per core.
Operational Impact
Quantitative Benefit
Related Case Studies.
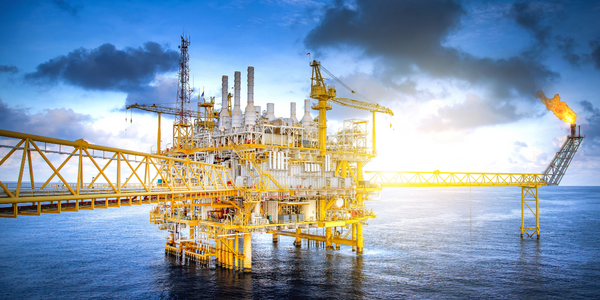
Case Study
Taking Oil and Gas Exploration to the Next Level
DownUnder GeoSolutions (DUG) wanted to increase computing performance by 5 to 10 times to improve seismic processing. The solution must build on current architecture software investments without sacrificing existing software and scale computing without scaling IT infrastructure costs.
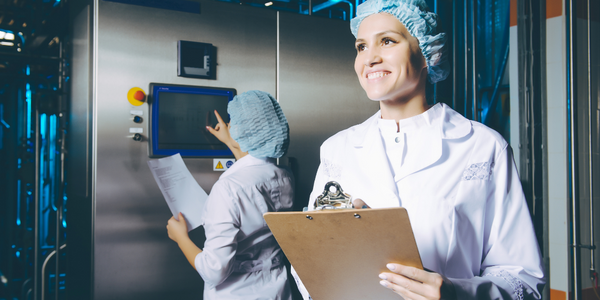
Case Study
Remote Wellhead Monitoring
Each wellhead was equipped with various sensors and meters that needed to be monitored and controlled from a central HMI, often miles away from the assets in the field. Redundant solar and wind generators were installed at each wellhead to support the electrical needs of the pumpstations, temperature meters, cameras, and cellular modules. In addition to asset management and remote control capabilities, data logging for remote surveillance and alarm notifications was a key demand from the customer. Terra Ferma’s solution needed to be power efficient, reliable, and capable of supporting high-bandwidth data-feeds. They needed a multi-link cellular connection to a central server that sustained reliable and redundant monitoring and control of flow meters, temperature sensors, power supply, and event-logging; including video and image files. This open-standard network needed to interface with the existing SCADA and proprietary network management software.
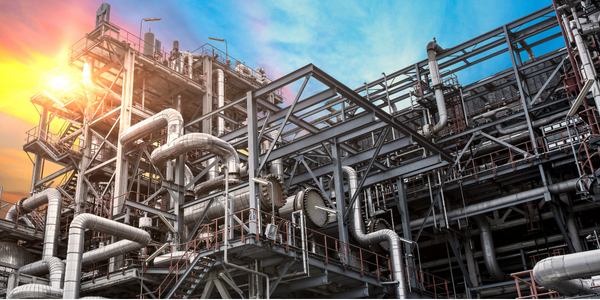
Case Study
Refinery Saves Over $700,000 with Smart Wireless
One of the largest petroleum refineries in the world is equipped to refine various types of crude oil and manufacture various grades of fuel from motor gasoline to Aviation Turbine Fuel. Due to wear and tear, eight hydrogen valves in each refinery were leaking, and each cost $1800 per ton of hydrogen vented. The plant also had leakage on nearly 30 flare control hydrocarbon valves. The refinery wanted a continuous, online monitoring system that could catch leaks early, minimize hydrogen and hydrocarbon production losses, and improve safety for maintenance.