Download PDF
European Engineering Company Saves $400,000 USD on CAPEX Using aspenONE Engineering
Technology Category
- Platform as a Service (PaaS) - Application Development Platforms
Applicable Industries
- Oil & Gas
- Agriculture
- Chemicals
Applicable Functions
- Discrete Manufacturing
- Quality Assurance
Use Cases
- Predictive Maintenance
- Process Control & Optimization
Services
- Software Design & Engineering Services
- System Integration
The Challenge
PETROLTERV, a Hungarian engineering design and consulting company, was tasked with revamping the gas treatment technology at Hungary’s largest underground gas storage facility to meet new European (EN) standards. The new standards imposed more stringent hydrocarbon and water dew point requirements for natural gas handling systems than what was previously prevailing in Hungary. The site had three gas treatment trains each employing a TEG (Triethylene glycol) dehydration unit and a low temperature separation (LTS) unit which employed a propane refrigeration system and brazed aluminum heat exchangers (BAHX).
About The Customer
PETROLTERV is an engineering design and consulting company founded in 1967 and based in Szeged, Hungary. The company traditionally delivered projects for the oil and gas industry; however, with the aid of state-of-the-art software such as aspenONE Engineering, they also serve other industries including chemical, agriculture and heavy. PETROLTERV consists of in-house teams focused on process control system engineering, mechanical engineering, equipment design, civil engineering, electrical engineering and GIS/geodesy. Using the expertise of these teams, PETROLTERV can provide full service on complex projects for their clients, and consider environmental responsibility during the preparatory and planning phases of those projects. Their mission is to provide high-quality and reliable engineering designs and services, as well as consultancy for their existing and future partners.
The Solution
PETROLTERV used the aspenONE Engineering suite from Aspen Technology, which included Aspen HYSYS and Aspen Exchanger Design & Rating (EDR), to rigorously simulate and design improvements to their gas treatment process that met new EN standards. The team was able to rigorously simulate the propane-based refrigeration system and the brazed aluminum heat exchanger operation to determine new design alternatives in order to meet new stringent standards. The following key modifications were proposed to meet the new requirements: Increase the capacity of the refrigeration units, Replace the refrigerant medium, Change existing BAHX units and install filter separators to protect the new heat exchangers.
Operational Impact
Quantitative Benefit
Related Case Studies.
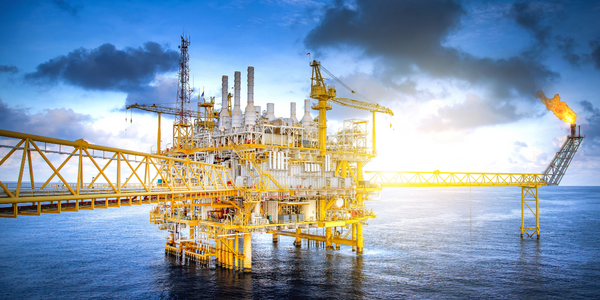
Case Study
Taking Oil and Gas Exploration to the Next Level
DownUnder GeoSolutions (DUG) wanted to increase computing performance by 5 to 10 times to improve seismic processing. The solution must build on current architecture software investments without sacrificing existing software and scale computing without scaling IT infrastructure costs.
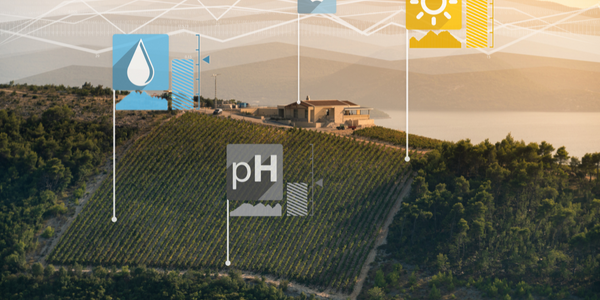
Case Study
Intelligent Farming with ThingWorx Analytics
Z Farms was facing three challenges: costly irrigation systems with water as a limited resource, narrow optimal ranges of soil moisture for growth with difficult maintenance and farm operators could not simply turn on irrigation systems like a faucet.
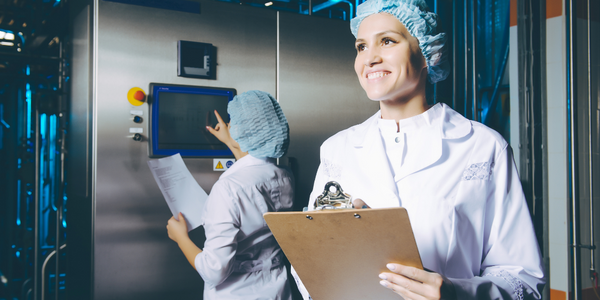
Case Study
Remote Wellhead Monitoring
Each wellhead was equipped with various sensors and meters that needed to be monitored and controlled from a central HMI, often miles away from the assets in the field. Redundant solar and wind generators were installed at each wellhead to support the electrical needs of the pumpstations, temperature meters, cameras, and cellular modules. In addition to asset management and remote control capabilities, data logging for remote surveillance and alarm notifications was a key demand from the customer. Terra Ferma’s solution needed to be power efficient, reliable, and capable of supporting high-bandwidth data-feeds. They needed a multi-link cellular connection to a central server that sustained reliable and redundant monitoring and control of flow meters, temperature sensors, power supply, and event-logging; including video and image files. This open-standard network needed to interface with the existing SCADA and proprietary network management software.
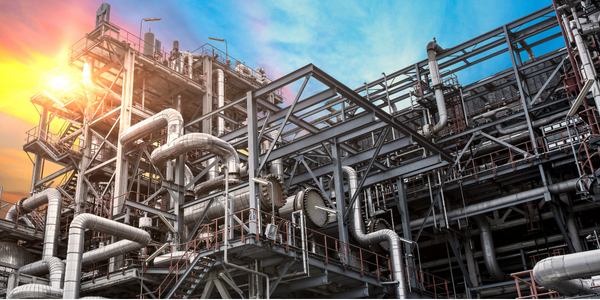
Case Study
Refinery Saves Over $700,000 with Smart Wireless
One of the largest petroleum refineries in the world is equipped to refine various types of crude oil and manufacture various grades of fuel from motor gasoline to Aviation Turbine Fuel. Due to wear and tear, eight hydrogen valves in each refinery were leaking, and each cost $1800 per ton of hydrogen vented. The plant also had leakage on nearly 30 flare control hydrocarbon valves. The refinery wanted a continuous, online monitoring system that could catch leaks early, minimize hydrogen and hydrocarbon production losses, and improve safety for maintenance.