Download PDF
Fully Automated Optimization and Manufacturing of CFRP Components
Technology Category
- Functional Applications - Manufacturing Execution Systems (MES)
- Networks & Connectivity - Ethernet
Applicable Industries
- Aerospace
- Automotive
Applicable Functions
- Facility Management
- Product Research & Development
Use Cases
- Manufacturing Process Simulation
- Manufacturing System Automation
Services
- System Integration
- Training
The Challenge
The production of carbon fiber reinforced plastic (CFRP) components in high volume and economically is a significant challenge due to complex design shapes and primarily manual manufacturing processes. This has limited the production of fiber composite materials to small series or single products. Despite the desirable properties of CFRP components, such as their lightweight potential and excellent mechanical properties, their complex design and cost-intensive manufacturing processes have been a disadvantage. The Fiber Patch Preforming (FPP) method, developed under the leadership of Airbus Group Innovations, enabled the automated production of composite preforms from a software lay-up plan. However, the next challenge was creating a manufacturing facility suitable for mass production and efficient processing of the fiber patches. This led to the SOWEMA research project, which aimed to develop a flexible and fully automated manufacturing process using the FPP method.
About The Customer
Manz AG, based in Reutlingen, Germany, is a leading high-tech engineering company that has grown in recent years from an automation specialist into a supplier of production lines. With four main business divisions in Battery/Fuel Cell, Display, Electronics, and Solar applications, Manz provides turn-key production plants for various industries. The company’s New Business division was already involved in the SOWEMA project and had experience in lightweight design and composites. The New Business division was one of the driving forces behind the collaboration with Altair to extend the process of flexible FPP manufacturing with preceded component optimization.
The Solution
Manz AG, a leading high-tech engineering company, partnered with Altair and its engineering services division, Altair ProductDesign, to extend the process of flexible FPP manufacturing with preceded component optimization. The overall goal of the SOWEMA project was to shorten the entire development and production cycle, from CAD drawing to final product, while maintaining the flexibility and repeatability the FPP facility offers. To study the feasibility and assess the advantages and disadvantages of the entire process, including an automated optimization, the combined Manz Altair ProductDesign team used a bicycle seat as their first test object. The optimization process was completely automated, with the user only needing to insert the CAD model and the occurring loads. The result of the automated optimization was a file containing the optimized structure of the component, including load-specific fiber orientation and laminate structure. This file was subsequently complemented with process and machine data, and the Manz production machine then manufactured the part using the FPP method.
Operational Impact
Quantitative Benefit
Related Case Studies.
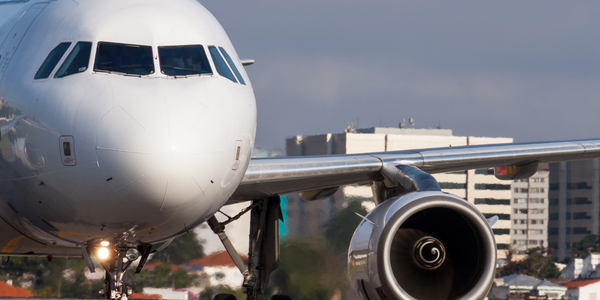
Case Study
Airbus Soars with Wearable Technology
Building an Airbus aircraft involves complex manufacturing processes consisting of thousands of moving parts. Speed and accuracy are critical to business and competitive advantage. Improvements in both would have high impact on Airbus’ bottom line. Airbus wanted to help operators reduce the complexity of assembling cabin seats and decrease the time required to complete this task.
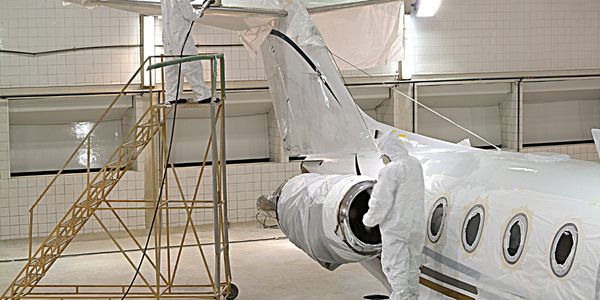
Case Study
Aircraft Predictive Maintenance and Workflow Optimization
First, aircraft manufacturer have trouble monitoring the health of aircraft systems with health prognostics and deliver predictive maintenance insights. Second, aircraft manufacturer wants a solution that can provide an in-context advisory and align job assignments to match technician experience and expertise.
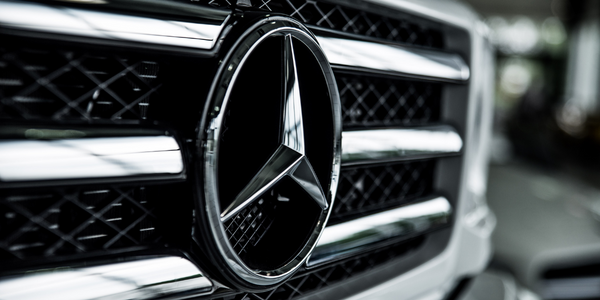
Case Study
Integral Plant Maintenance
Mercedes-Benz and his partner GAZ chose Siemens to be its maintenance partner at a new engine plant in Yaroslavl, Russia. The new plant offers a capacity to manufacture diesel engines for the Russian market, for locally produced Sprinter Classic. In addition to engines for the local market, the Yaroslavl plant will also produce spare parts. Mercedes-Benz Russia and his partner needed a service partner in order to ensure the operation of these lines in a maintenance partnership arrangement. The challenges included coordinating the entire maintenance management operation, in particular inspections, corrective and predictive maintenance activities, and the optimizing spare parts management. Siemens developed a customized maintenance solution that includes all electronic and mechanical maintenance activities (Integral Plant Maintenance).
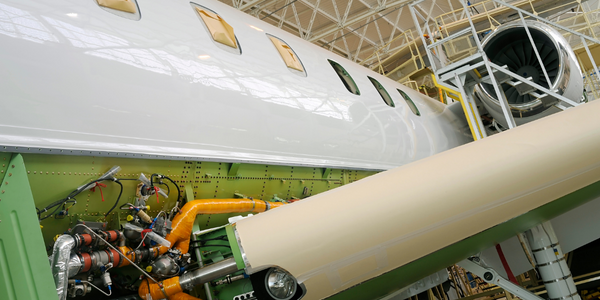
Case Study
Aerospace & Defense Case Study Airbus
For the development of its new wide-body aircraft, Airbus needed to ensure quality and consistency across all internal and external stakeholders. Airbus had many challenges including a very aggressive development schedule and the need to ramp up production quickly to satisfy their delivery commitments. The lack of communication extended design time and introduced errors that drove up costs.