Download PDF
GKN Land System: Business intelligence proactively manages supply chain performance
Technology Category
- Analytics & Modeling - Big Data Analytics
- Analytics & Modeling - Real Time Analytics
Applicable Industries
- Automotive
Applicable Functions
- Logistics & Transportation
- Procurement
Use Cases
- Supply Chain Visibility
- Inventory Management
Services
- Cloud Planning, Design & Implementation Services
- Data Science Services
The Challenge
GKN Land Systems, a global supplier of integrated powertrain components, systems, solutions and services, faced a challenge as it grew through acquisitions. The complexity of its ERP system increased, making it difficult to maintain high-level oversight of key performance indicators (KPIs) for supply chain management, inventory management, procurement and customer satisfaction. The company needed a solution that could provide a comprehensive view of its operations and help it monitor its performance against KPIs.
About The Customer
GKN Land Systems is a global supplier of integrated powertrain components, systems, solutions and services. The company has 39 manufacturing facilities worldwide. As the company grew through acquisitions, it faced the challenge of managing the increasing complexity of its ERP system. This complexity made it difficult for the company to maintain high-level oversight of key performance indicators (KPIs) for supply chain management, inventory management, procurement and customer satisfaction.
The Solution
GKN Land Systems implemented a data warehouse and business intelligence solution that enables the company to monitor how it and its manufacturing facilities are meeting KPIs. The solution triggers automated alerts when deviations occur. For example, if customer satisfaction scores are dropping, GKN Land Systems can use the BI solution to drill down into both facility and business process data along several dimensions to find the root cause and implement measures to quickly resolve the problem. The solution components include IBM Netezza 1000, IBM Cognos Business Intelligence V10, IBM InfoSphere DataStage, and IBM Global Business Services— Business Consulting Services.
Operational Impact
Quantitative Benefit
Related Case Studies.
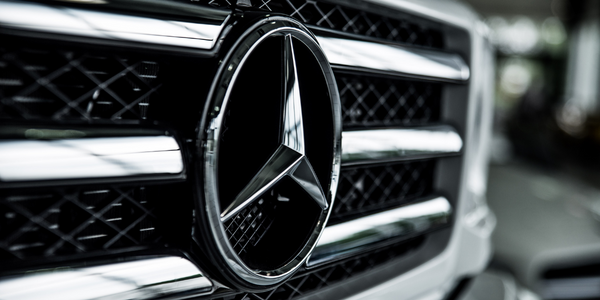
Case Study
Integral Plant Maintenance
Mercedes-Benz and his partner GAZ chose Siemens to be its maintenance partner at a new engine plant in Yaroslavl, Russia. The new plant offers a capacity to manufacture diesel engines for the Russian market, for locally produced Sprinter Classic. In addition to engines for the local market, the Yaroslavl plant will also produce spare parts. Mercedes-Benz Russia and his partner needed a service partner in order to ensure the operation of these lines in a maintenance partnership arrangement. The challenges included coordinating the entire maintenance management operation, in particular inspections, corrective and predictive maintenance activities, and the optimizing spare parts management. Siemens developed a customized maintenance solution that includes all electronic and mechanical maintenance activities (Integral Plant Maintenance).
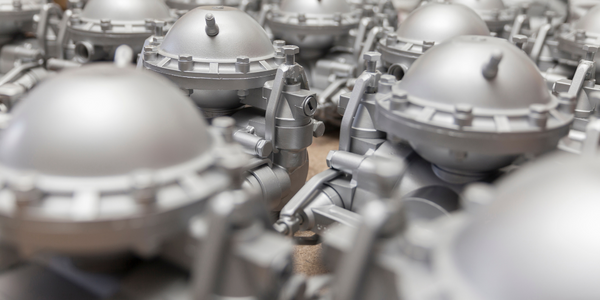
Case Study
Monitoring of Pressure Pumps in Automotive Industry
A large German/American producer of auto parts uses high-pressure pumps to deburr machined parts as a part of its production and quality check process. They decided to monitor these pumps to make sure they work properly and that they can see any indications leading to a potential failure before it affects their process.