Download PDF
Graham Hart Delivers Highly Engineered Heat Transfer Equipment with aspenONE Engineering Suite
Technology Category
- Application Infrastructure & Middleware - Data Exchange & Integration
Applicable Industries
- Oil & Gas
- Chemicals
Applicable Functions
- Product Research & Development
- Quality Assurance
Use Cases
- Predictive Maintenance
- Process Control & Optimization
Services
- Software Design & Engineering Services
The Challenge
Graham Hart, a UK-based supplier of engineered process systems, needed to deliver optimized designs that meet stringent performance conditions. The company's value proposition is in the supply of highly-reliable, high-performance heat exchangers. To achieve and maintain this differentiated market position, the ability of its engineering team to propose and deliver best-fit designs to meet stringent performance conditions is paramount. The engineering team needed to depend on the quality, accuracy, reliability, and predictability of the software tools used to conduct the modeling and analysis to develop and verify designs. This includes the actual layout and design of heat exchanger systems, including temperatures, configurations, and materials.
About The Customer
Graham Hart (Process Technology) Limited is a UK-based company known for its high level of commitment to customer service and for its excellent standards of technical expertise and product quality. The company is a privately held supplier of engineered process systems, supplying heat exchangers and high-pressure equipment to clients worldwide. Its core business is in the bespoke design and fabrication of high-integrity heat transfer systems, as well as pressure vessel systems and other packaged process systems in certain applications. The company enjoys a strong record of repeat business from its key EPC and owner-operator clients.
The Solution
Graham Hart has used the Aspen Exchanger Design & Rating (EDR) product suite as a core component of its heat exchanger design process since the company was founded. This dates back to Graham Hart’s selection of the original BJAC software, about 30 years ago, which was the original thermal design software product that later evolved into the Aspen Shell and Tube Exchanger Design software module. In addition to shell and tube heat exchangers (of various designs and types), Graham Hart also produces air cooled heat exchangers, which are also designed using Aspen EDR. Since the original selection of that software, Graham Hart has consistently used the Aspen EDR suite as the core thermal design tool for virtually all of the heat exchanger systems that it designs and delivers, gaining excellent results and a strong record of repeat business from its key EPC and owner-operator clients.
Operational Impact
Quantitative Benefit
Related Case Studies.
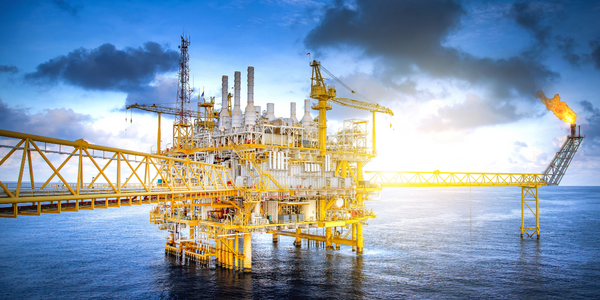
Case Study
Taking Oil and Gas Exploration to the Next Level
DownUnder GeoSolutions (DUG) wanted to increase computing performance by 5 to 10 times to improve seismic processing. The solution must build on current architecture software investments without sacrificing existing software and scale computing without scaling IT infrastructure costs.
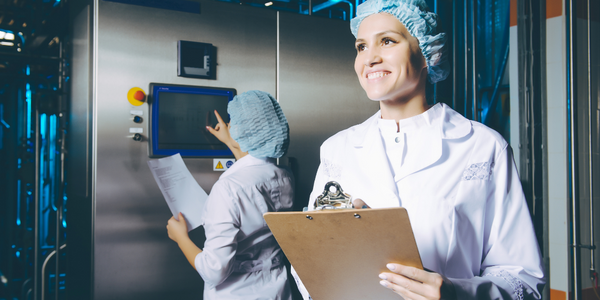
Case Study
Remote Wellhead Monitoring
Each wellhead was equipped with various sensors and meters that needed to be monitored and controlled from a central HMI, often miles away from the assets in the field. Redundant solar and wind generators were installed at each wellhead to support the electrical needs of the pumpstations, temperature meters, cameras, and cellular modules. In addition to asset management and remote control capabilities, data logging for remote surveillance and alarm notifications was a key demand from the customer. Terra Ferma’s solution needed to be power efficient, reliable, and capable of supporting high-bandwidth data-feeds. They needed a multi-link cellular connection to a central server that sustained reliable and redundant monitoring and control of flow meters, temperature sensors, power supply, and event-logging; including video and image files. This open-standard network needed to interface with the existing SCADA and proprietary network management software.
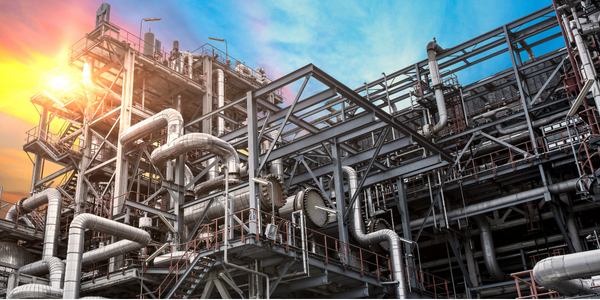
Case Study
Refinery Saves Over $700,000 with Smart Wireless
One of the largest petroleum refineries in the world is equipped to refine various types of crude oil and manufacture various grades of fuel from motor gasoline to Aviation Turbine Fuel. Due to wear and tear, eight hydrogen valves in each refinery were leaking, and each cost $1800 per ton of hydrogen vented. The plant also had leakage on nearly 30 flare control hydrocarbon valves. The refinery wanted a continuous, online monitoring system that could catch leaks early, minimize hydrogen and hydrocarbon production losses, and improve safety for maintenance.
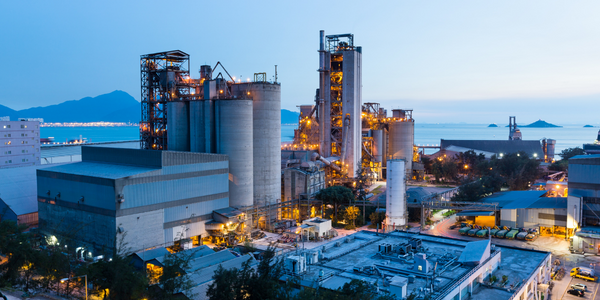
Case Study
Honeywell - Tata Chemicals Improves Data Accessibility with OneWireless
Tata was facing data accessibility challenges in the cement plant control room tapping signals from remote process control areas and other distant locations, including the gas scrubber. Tata needed a wireless solution to extend its control network securely to remote locations that would also provide seamless communication with existing control applications.